Определение момента затяжки бола (гайки)
Определение момента затяжки бола (гайки)
Момент затяжки болта можно определить по таблице приведенной ниже, но для этого необходимо знать, что означает маркировка на головке болта
На головке болта должна быть нанесена следующая маркировка:
– клеймо завода изготовителя
– класс прочности;
– правая резьба не маркируется, если резьба левая – маркируется стрелкой против часовой стрелки.
Для изделий из углеродистой стали, класс прочности обозначают двумя цифрами через точку.
Пример: 4.6; 8.8; 10.9; 12.9
Первая цифра: обозначает 0,01 номинальной величины предела прочности на разрыв, измеренную в МПа. В случае класса 8.8 первая 8 обозначает 8 х 100 = 800 МПа = 800 Н/мм2 = 80 кгс/мм2
Вторая цифра: это отношение предела текучести к пределу прочности, умноженному на 10. Из пары цифр можно узнать предел текучести материала 8 х 8 х 10 = 640 Н/мм2,
Пример для класса 5. 8 : предел прочности на разрыв = 500 Н/мм2, предел текучести = 5*8*10=400 Н/мм2)
Значение предела текучести имеет важное практическое значение, поскольку это и есть максимальная рабочая нагрузка болта. В случае превышения данного значения болт «потечет» – вытянется в длину и соединение будет непрочным, что недопустимо на конструкциях ответственного значения (мосты, перекрытия и пр).
Для изделий из нержавеющей стали наносится маркировка стали – А2 или А4 – и предел прочности – 50, 60, 70, 80, например: А2-50, А4-80.
Число в этой маркировке означает – 1/10 соответствия пределу прочности углеродистой стали.
Перевод единиц измерения: 1 Па = 1Н/м2; 1 МПа = 1 Н/мм2 = 10 кгс/см2.
В таблице 1 приведены практические моменты затяжки болтов из углеродистой стали Н*м. У болта при этом остается запас прочности, достаточный для того, чтобы он гарантированно не “потек”. Естественно, это не означает, что все соединения следует затягивать до этой величины.
Таблица 1. Практические моменты затяжек болтов из углеродистой стали
Резьба/шаг мм |
Класс прочности болтов |
||||
4,6 |
5,8 |
8,8 |
10,9 |
12,9 |
|
момент затяжки Н*м |
|||||
5/0.8 |
2,1 |
3,5 |
5,5 |
7,8 |
9,3 |
6/1. |
3,6 |
5,9 |
9,4 |
13,4 |
16,3 |
8/1.25 |
8,5 |
14,4 |
23,0 |
31,7 |
38,4 |
10/1.5 |
16,3 |
27,8 |
45,1 |
62,4 |
75,8 |
12/1.75 |
28,8 |
49,0 |
77,8 |
109,4 |
130,6 |
14/2. |
46,1 |
76,8 |
|
173,8 |
208,3 |
16/2.0 |
71,0 |
118,1 |
189,1 |
265,9 |
319,7 |
18/2.5 |
98,9 |
165,1 |
264,0 |
370,6 |
444,5 |
20/2.5 |
138,2 |
230,4 |
369,6 |
519,4 |
623,0 |
22/2. |
186,2 |
311,0 |
497,3 |
698,9 |
839,0 |
24/3.0 |
239,0 |
399,4 |
638,4 |
897,6 |
1075,2 |
27/3.0 |
345,6 |
576,0 |
922,6 |
|
1555,2 |
30/3.5 |
472,3 |
786,2 |
1257,6 |
1766,4 |
2121,6 |
33/3. |
636,5 |
1056,0 |
1699,2 |
2380,8 |
2860,8 |
36/4.0 |
820,8 |
1363,2 |
2188,8 |
3081,6 |
3696,0 |
39/4.0 |
1056,0 |
1756,8 |
2820,2 |
3955,2 |
4742,4 |
Таблица 2. Предельные моменты затяжки для болтов (гаек)
Резьба/шаг мм |
Класс прочности болта |
||
8,8 |
10,9 |
12,9 |
|
предельный момент затяжки Н*м |
|||
5/0. |
2,1 |
3,5 |
5,5 |
6/1.0 |
3,6 |
5,9 |
9,4 |
8/1.25 |
8,5 |
14,4 |
23,0 |
10/1.5 |
16,3 |
27,8 |
45,1 |
12/1.75 |
28,8 |
49,0 |
77,8 |
14/2. |
46,1 |
76,8 |
122,9 |
16/2.0 |
71,0 |
118,1 |
189,1 |
18/2.5 |
98,9 |
165,1 |
264,0 |
20/2.5 |
138,2 |
230,4 |
369,6 |
22/2.5 |
186,2 |
311,0 |
497,3 |
24/3. |
239,0 |
399,4 |
638,4 |
27/3.0 |
345,6 |
576,0 |
922,6 |
30/3.5 |
472,3 |
786,2 |
1257,6 |
33/3.5 |
636,5 |
1056,0 |
1699,2 |
36/4.0 |
820,8 |
1363,2 |
2188,8 |
39/4. |
1056,0 |
1756,8 |
2820,2 |
Выше перечисленные величины даются для стандартных болтов и гаек, имеющих
метрическую резьбу. Для нестандартного и специального крепежа смотрите руководство по ремонту ремонтируемой техники.
Затяжка резьбовых соединений
Технический уровень и качество крепёжных деталей и соединений имеют важное значение для обеспечения высоких потребительских характеристик машин, механизмов, строительных конструкций, бытовой техники, другой продукции. Известно, что большинство отказов в автотранспортных средствах так или иначе связано с крепёжными деталями, ослаблением соединений, а любые ремонты и обслуживание – с отвинчиванием и завинчиванием болтов, гаек, винтов и т.д.
Надёжность соединений узлов зависит от технического уровня конструкции в целом, качества крепёжных деталей и качества сборки [1].
Надёжность резьбовых соединений — это, в первую очередь, гарантия длительного сохранения усилия предварительной затяжки в период эксплуатации. Как обеспечить это?
Силовые параметры резьбовых соединений. Надёжность крепежа.
Чтобы ответить на поставленный вопрос, сначала назовём основные силовые параметры резьбовых соединений. ГОСТ 1759.4 устанавливает для крепёжных деталей минимальную разрушающую нагрузку(Рр, Н) и пробную нагрузку(N, Н), которая для классов прочности 6.8 и выше составляет 74-79% от минимальной разрушающей нагрузки. Пробная нагрузка является контрольной величиной, которую стержневая крепёжная деталь должна выдержать при испытаниях.
Усилие предварительной затяжки (далее – усилие затяжки – Q, Н), на которое производится затяжка резьбового соединения, обычно принимаетсяв пределах 75-80%, в отдельных случаях и 90%, от пробной нагрузки[1]. Нередко возникает вопрос почему «предварительной»? Дело в том, что затяжка соединений подразумевает создание во всех деталях – и крепёжных, и соединяемых, некоторых напряжений. При этом в упруго напряжённых телах проявляются некоторые механизмы пластических деформаций, ведущие к убыванию напряжений во времени (явление релаксации напряжений). Поэтому по истечении некоторого времени усилие затяжки соединения несколько снижается без каких либо дополнительных силовых воздействий на него. В табл. 1 для справок приведены значения усилий затяжки нескольких размеров соединений.
Таблица 1
Значения усилий затяжки,Q, Н | |||
Размер резьбы болта | Класс прочности 6.8 | Класс прочности 8.8 | Класс прочности 10.9 |
М6 | 7540 | 8700 | 12530 |
М8 | 12750 | 15900 | 22800 |
М10 | 19130 | 25280 | 36080 |
М12 | 27230 | 36680 | 52500 |
Существует несколько способов затяжки резьбовых соединений: затяжка до определённого момента, затяжка до определённого угла, затяжка до предела упругости, затяжка в области пластических деформаций и другие.
Затяжка соединений до определённого момента
В отечественной практике чаще всего применяется затяжка путём приложения к крепёжной детали необходимого крутящего момента затяжки (далее – момента затяжки, Мкр, Н*м), который обычно указывается в чертежах или технологии сборки. В автомобильной промышленности для назначения моментов затяжки используются отраслевые стандарты [2; 3] и руководящий документ [4], которые распространяются на резьбовые соединения с болтами, шпильками и гайками с цилиндрической метрической резьбой номинальным диаметром от М3 до М24 в зависимости от размеров, класса прочности крепёжной детали и класса соединения.
В зависимости от степени ответственности соединений назначаются классы резьбовых соединений и соответствующие им величины максимальных и минимальных моментов затяжки, объёма их контроля (проверки), приведенные в табл.2.
Таблица 2. Классы резьбовых соединений по [3]
Класс соедин. | Наименование | Допускаемое отклон. от расчетного Мкр, % | Объем контроля затяжки | |
Максим. | Минимум | |||
I | Особо ответственные | +5 | -5 | 100% соединений |
II | Ответственные | +5 | -15 | |
III | Общего назначения | +5 | -35 | Периодически, согласно техдок. |
IV | Малоответственные | +5 | -65 |
Несколько иные, но во многом аналогичные классы резьбовых соединений приводит, например, стандарт фирмы Renault[5], называя их классами точности прилагаемого момента:
класс А | имеет поле допуска Мкр на инструменте | ±5% |
класс В | имеет поле допуска Мкр на инструменте | ±10% |
класс М | имеет поле допуска Мкр на инструменте | ±15% |
класс С | имеет поле допуска Мкр на инструменте | ±20% |
класс D | имеет поле допуска Мкр на инструменте | ±35% |
класс Е | имеет поле допуска Мкр на инструменте | ±45% |
Видно, что классы А, В, С, D соответствуют по полю допуска классам по табл. 2.
Номинальный крутящий момент рассчитывается по известной формуле [1; 4;7]:
Мкр = 0,001 Q[0,16 Р + µр 0,58 d2 + µт 0,25 (dт + d0) ],
где µр– коэффициент трения в резьбе;
µт — коэффициент трения на опорном торце;
dт – диаметр опорной поверхности головки болта или гайки,мм;
d0 – диаметр отверстия под крепёжную деталь, мм;
Р – шаг резьбы, мм;
d2– средний диаметр резьбы, мм.
Существенное влияниена затяжку крепёжных соединений оказывают условия контактного трения в резьбе и на опорной поверхности, зависящие от таких факторов, как состояние контактных поверхностей, вид покрытия, наличие смазочного материала, погрешности шага и угла профиля резьбы, отклонение от перпендикулярности опорного торца и оси резьбы, скорость завинчивания и др. Значения коэффициента трения в реальных условиях сборки можно лишь прогнозировать. Как показывают многочисленные эксперименты, они не стабильны. В табл. 3 приведены их справочные значения [6].
Таблица 3. Значения коэффициентов трения в резьбе µри на опорном торце µт
Вид покрытия | Коэффициент трения | Без смазочного материала | Машинное масло | Солидол синтетический | Машинное масло с МоS2 |
Без покрытия | µр | 0,32-0,52 | 0,19-0,24 | 0.16-0,21 | 0,11-0,15 |
µт | 0,14-0,24 | 0,12-0.14 | 0,11-0,14 | 0,07-0,10 | |
Цинкование | µр | 0,24-0,48 | 0,15-0,20 | 0,14-0,19 | 0,14-0,19 |
µт | 0,07-0. | 0.09-0,12 | 0,08-0,10 | 0,06-0,09 | |
Фосфатирование | µр | 0,15-0,50 | 0,15-0,20 | 0,15-0.19 | 0.14-0,16 |
µт | 0,09-0,12 | 0,10-0,13 | 0,09-0,13 | 0,07-0,13 | |
Оксидирование | µр | 0.50-0,84 | 0,39-0.51 | 0,37-0,49 | 0.15-0,21 |
µт | 0,20-0,43 | 0,19-0.29 | 0.19-0,29 | 0,07-0,11 |
Для упрощения расчётов Мкр коэффициенты трения обычно усредняют. В качестве примера в табл. 4 приведены результаты сравнительного расчёта моментов затяжки соединения болт-гайка размером М8, класса прочности 8. 8-8. Значения коэффициентов трения µриµт взяты средними от приведённых в табл.3. Конечные результаты расчётов достаточно близки.
Таблица 4. Результаты сравнительного расчёта момента затяжки крепежа
Вид смазки и покрытия | Разные коэффициенты трения | Усреднен. к-ты трения | |||
µр | µт | Мкр.разд, Н?м | µ=0,5(µр+µт) | Мкр.сред, Н?м | |
6Ц хр | 0,36 | 0,09 | 34,9 | 0,22 | 36,8 |
6Ц хр, солидол | 0,165 | 0,09 | 21,9 | 0.13 | 23,0 |
Без смазки и покрытия | 0,42 | 0,19 | 47,6 | 0,30 | 48,9 |
Для понимания и правильного назначения режимов сборки резьбовых соединений важно знать на что расходуется Мкр. В табл. 5 приведены результаты расчёта момента затяжки в целом и по составляющим. Три составляющие момента затяжки (см. формулу) отражают их доли, идущие на создание усилия затяжки (12-15%), на преодоление сил трения в резьбе (32-39%) и на преодоление сил трения под головкой болта или под гайкой (47-54%) [1].
Как видим на создание усилия затяжки расходуется лишь до 15% Мкр.
Таблица 5. Моменты затяжки соединений и их составляющие, Мкр, Н*м
Размер резьбы ишестигр., мм | Всего | На создание усилия затяжки | На трение в резьбе | На трение под головкой | ||||
Класс прочности | ||||||||
6.8 | 8.8 | 6.8 | 8.8 | 6.8 | 8.8 | 6.8 | 8.8 |
М6; S=10 | 8. | 9,6 | 1.2 | 1,4 | 3,0 | 3,5 | 4,1 | 4,7 |
М8; S=13 | 18,4 | 23 | 2.6 | 3,2 | 6.9 | 8.6 | 8,9 | 11,2 |
М10; S=17 | 35 | 46,3 | 4,6 | 6,0 | 13,0 | 17,2 | 17,4 | 23,5 |
При применении соединений с фланцевыми болтами и гайками важно учитывать влияние на момент затяжки увеличенной опорной поверхности под головкой. Момент требуется на 10-15% выше, чем без фланца.
Крепёж. Точность способа затяжки по моменту
Итак, все действия разработчиков крепёжных соединений в машинах и механизмах сводится к назначению Мкр. Но обеспечит ли этот момент получение необходимого усилия затяжки? Зная сильное влияние условий трения и класса соединения на зависимость между усилием и моментом затяжки, покажем каков может быть разброс достигаемых значений Q при сборке. В качестве примера рассмотрим соединение болт-гайка М8 класса прочности 8.8-8, покрытие цинковое с хроматированием без смазочного материала. Номинальное усилие затяжки Q= 15900 Н.По [4] имеемМкр макс = 24,4 Н*м.
Близкие значения Q и Мкр приводятся в материалах фирм Renault, Gedore, Facom и других.
Рассчитаемпри возможных значениях коэффициентов трения 0,3, 0,14 и 0,10 величины достигаемого усилия затяжки при названных моментах затяжки для соединений II и III классов (табл. 6) и построим диаграмму в координатах Q– Мкр (рис. 1). Виден весьма существенный разброс достигаемых значений усилия затяжки (заштрихованная четырехугольная зона) при заданных крутящих моментах. Для соединений II класса это А2ВСD2, а III класса – А3ВСD3.
Минимально достигаемое усилие затяжки Qминполучается при приложении минимального крутящего момента затяжки Мкр. мин при максимальном коэффициенте трения µмакс(точки А2 и А3 на диаграмме).
Таблица 6. Результаты расчётов усилия затяжки, Q, Н
Момент затяжки, Н/м | Коэффициент трения, µ | ||
0,3 | 0,14 | 0,10 | |
Мкр. макс = 24,4 | 7870 | 15900 | 21030 |
Мкр.мин = 19,8;11 класс | 6390 | 12860 | 17070 |
Мкр. мин = 15,1; 111класс | 4870 | 9800 | 13020 |
Максимальное усилие затяжки Qмакс достигается при приложении максимального крутящего момента Мкр. макс при наименьшем коэффициенте трения µмин (точка С на диаграмме).
Подобные графические изображения могут быть построены для каждого конкретного резьбового соединения. Точка соответствующего соотношения Мкр – Q находится внутри четырёхугольника.
Еще одна характеристика резьбовых соединений, влияющая на точность затяжки по моменту, назовём её «плотность» или «герметичность» стыка соединяемых деталей. Чем больше в пакете деталей (слоев), тем сильнее влияние заусенцев, неровностей, шероховатости контактных поверхностей.
Минимальное удельное усилие на контактных поверхностях должно устанавливаться из условия плотности стыкови не должно быть меньше s0 мин=(0,4 – 0,5)sт. Максимальное значение удельных усилий, обеспечивающих надёжность затяжки должно быть s0 макс=(0,8 – 0,9)sт.
Ранее мы приводили данные [1] о нежелательности применения плоских и пружинных шайб в соединениях и приводили варианты перехода, в частности, на фланцевый крепёж, что существенно повышает надёжность. Там же показаны отрицательные стороны применения болтов с шестигранной уменьшенной головкой, у которых контактные напряжения под головкой превышают sт.
Как видно способ затяжки с контролем момента даже при его точной фиксации не обладает необходимой надёжностью, далеко не всегда обеспечивает нужное усилие затяжки.
Методы контроля затяжки крепежа
Наиболее распространен метод контроля при помощи динамометрических ключей, имеющих точность в пределах ±5%. Ошибка в измерении величины момента зависит от принятого метода его определения. В [4] предусматриваются следующие методы.
Метод А. Момент измеряется непосредственно в начале вращения болта или гайки в направлении затягивания, измеренный таким образом момент называется «моментом страгивания с места». Метод применяется для быстрого контроля и осуществляется не позднее 30 минут после затяжки.
Метод В. Момент измеряется во время вращения при повороте на 10о – 15о в направлении завинчивания. Момент, полученный при этом, называется «моментом вращения». Метод применяется для периодического, но более точного контроля.
Метод С. Соединение освобождается и снова затягивается в прежнем положении, которое должно быть отмечено риской. Этот момент называется «моментом повторной затяжки» и применяется для контроля соединений, имеющих оксидные пленки, окраску, загрязнения.
Величины моментов затяжки при контрольных измерениях должны находитьсяв следующих диапазонах :
| Метод А | Метод В | Метод С |
От | 1,25 Мкр. макс | 1,08 Мкр. макс | 1,05 Мкр. макс |
До | 1,05 Мкр.мин | 0,92 Мкр.мин | 0,88 Мкр. |
В случае недостаточной величины момента затяжки производится подтяжка резьбового соединения до заданной величины момента. Заметим, что контроль качества затяжки особо ответственных соединений (класс 1 ) с допускаемым отклонением момента ±5% динамометрическим ключом, имеющим такую же точность, едва ли корректен.
Таким образом, показано, что как затяжка резьбовых соединений, так и её контроль базируются на косвенных методах путём приложения к крепёжной детали крутящего момента, но это далеко не всегда обеспечивает получение необходимого усилия затяжки.
Поэтому разработчики конструкции вынуждены для обеспечения требуемого усилия сжатия соединяемых деталей применять большее количество недозатянутых крепёжных деталей и увеличивать их диаметр.
Приведем примеры ошибок, которые стали возможными из-за указания в техдокументации только момента затяжки.
На автомобилях семейства ГАЗель при сборке крепления задней опоры двигателя имели место случаи разрушения болтов М10х6gх30 (210406) с полукруглой головкой и квадратным подголовком. Испытания болтов показывали, что они соответствуют требованиям ОСТа и имеют класс прочности 4.8. Оказалось, что, указанный в чертежах узла крутящий момент затяжки Мкрравнялся 28-36 Нм. Это соответствует соединению класса прочности 6.8.в результате усилие затяжки при Мкр. минзавышалось в 1,4 раза, а при Мкр.макс в 1,9 раза! После замены класса прочности болта на 6.8 дефекты сборки были исключены.
При сборке суппорта переднего тормоза автомобилей ВАЗ 2108(09) разрушался болт 2108-3501030 М12х1,25х30, имеющий класс прочности 10.9. Болт, имеющий покрытие фосфат с промасливанием, опирается на шайбу с таким же покрытием и закручивается в чугунный суппорт с цинковым покрытием. По чертежу Мкр.макс=118,4 Нм. В стандартах ВАЗа не было данных по коэффициенту трения для данного сочетания контактных поверхностей. По разным источникам отклонение Мкр могут составлять от ±10% до ±30%. Проведённые исследования этого резьбового соединения и условий его сборки на конвейере позволили выявить, объяснить и устранить причины разрушения болтов[1]. На рис. 2 показана диаграмма Q– Мкр, рассчитанная по методике Фиат-ВАЗ, где n — коэффициент использования предела текучести (n=s:sт, где s — суммарное напряжение в болте, создаваемое при затяжке). Для ответственного соединения (11 класса) коэффициент трения в резьбе и на опорной поверхности варьировался в пределах 0,1–0,18. Было определено, что при m=0,1 момент Мкр.мин=96,5 Нм, а усилие затяжки Q=59536 Н. При Мкр.макс=118,4 Нм усилие Q=73130 Н, что выше нагрузки до предела пропорциональности Qупр=72750 Н, то есть возможна пластическая деформация болта или его разрушение при сборке. Известно, что при случайном попадании масла и колебаниях толщины покрытий коэффициент трения может уменьшится до значения 0,08 и даже 0,06. В то же время было выявлено,что перед сборкой болты проходили операции мойки и промасливания, что недопустимо, ибо ещё больше увеличивало усилие затяжки.
Результаты исследований показали также целесообразность замены цилиндрической головки с внутренним шестигранником у болтана головку с волнистым приводом (типа ТОRХ) и 2-х радиусной поднутренной галтелью под головкой. За счёт этого удалось снизить напряжения под головкой и еще больше повысить надёжность крепления.
Приведённые примеры показывают, что исследования конструкций узлов и технологии сборки позволяют выяснить и исключить возможные дефекты, а также подтверждают необходимость перенесения внимания с момента на усилие затяжки.
О затяжке крепёжных соединений с контролем усилий
В мировой практике используются методы и инструменты, которые непосредственно контролируют усилие затяжки в ходе сборки. Осуществить затяжку резьбового соединения с контролем по усилию в лабораторных условиях несложно. Исследования показывают, что наибольшая точность обеспечения усилий затяжки в производственных усло
Таблицы моментов затяжки болтов динамометрическим ключом
Момент затяжки – это усилие, которое прикладывается к резьбовому соединению при его завинчивании. Если закрутить крепеж с меньшим усилием, чем это необходимо, то, под воздействием вибраций, резьбовое соединение может раскрутиться, не обеспечивая нужную герметичность между скрепляемыми деталями, что может привести к тяжелым последствиям.
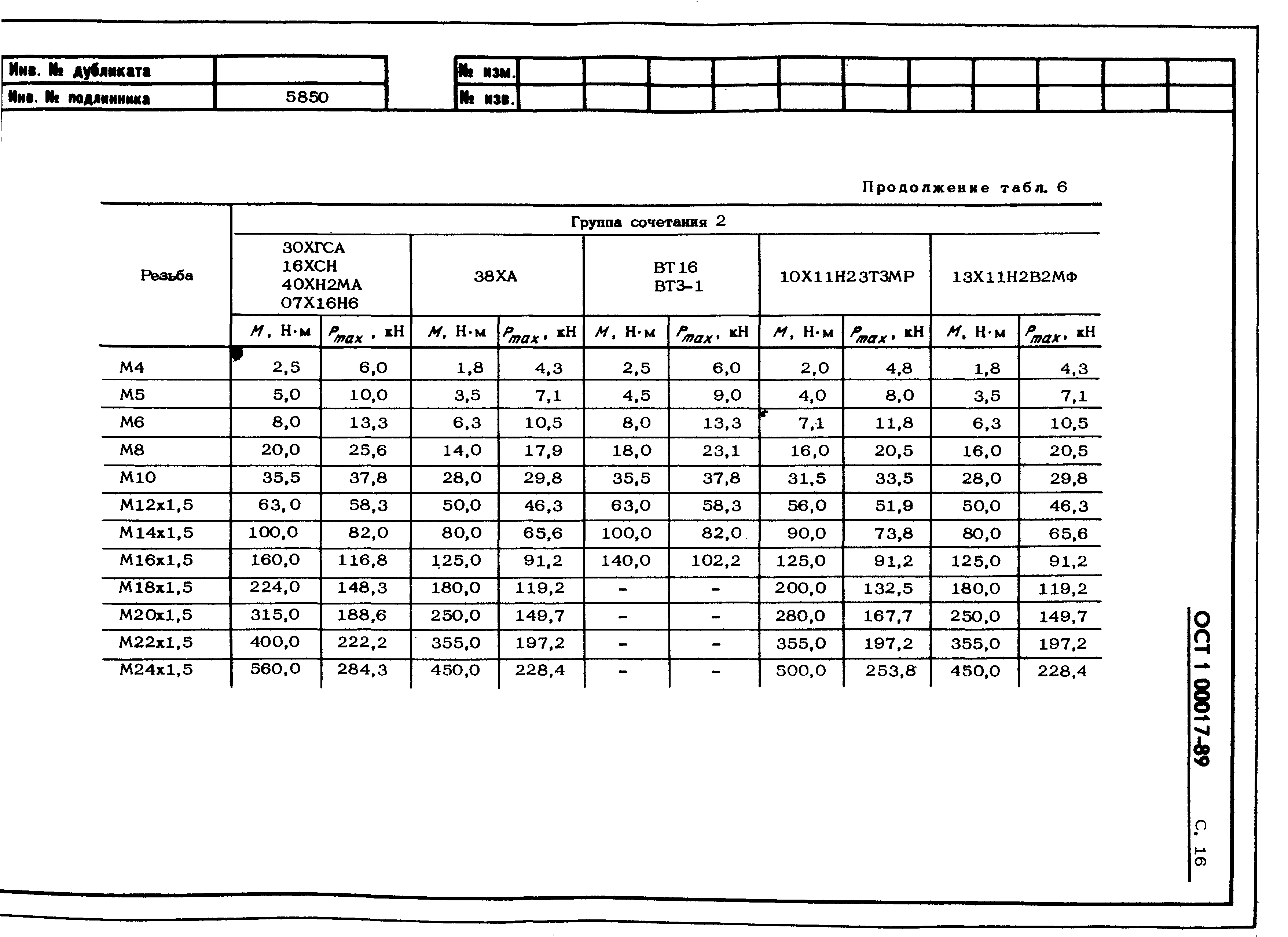
Для каждого размера и класса прочности резьбового соединения указаны определенные моменты затяжки. Все значения занесены в специальную таблицу усилий для затяжки динамометрическим ключом. Обычно, класс прочности болта указывается на его головке.
Классы прочности для метрических болтов
Класс прочности указывается цифрами на головке.
Классы прочности для дюймовых болтов
Информация о прочности выполнена в виде насечек на головке.
Маркировка деталей
Этот параметр указывается на головке болта. Для деталей, выполненных на основе углеродистой стали с классом прочности — 2, указываются цифры через точку, например: 3.5, 4.8 и т. д.
Первая цифра указывает 1/100 номинального размера прочностного предела на разрыв, измеряется в МПа. Например, если на головке болта, указано — 10. 1, то первое число означает 10*100 = 1000 МПа.
Вторая цифра — отношение пределов текучести к прочности, умножается на 10, по вышеуказанному примеру — 1*10*10= 100 МПа.
Предел текучести — это максимальная нагрузка на болт. Для элементов, выполненных из нержавеющей стали, наносится тип стали А2 или А4, и далее предел прочности. Например: А4—40. Число в данной маркировке характеризует 1/10 предела прочности углеродистой стали.
Редакторы сайта рекомендуют ознакомиться с системами выравнивания плитки СВП и DLS.
Как правильно затягивать ступичный подшипник
Величина затяжки переднего и заднего подшипника исчисляется на основании ряда факторов, таких как:
- Минимальный и максимально допустимый размер (параметр) подшипника.
- Величина осевого зазора.
- Тип шага резьбы (крупный или мелкий).
Вышеприведенный перечень данных носит шаблонный характер и в каждой конкретной ситуации может дополняться новыми факторами. Однако вышеупомянутые причины остаются неизменными, независимо от возникшей ситуации.
Единицы измерения
Основной величиной является Паскаль, единица измерения давления, механического напряжения, согласно международной системе «СИ». Паскаль равняется давлению, вызванному силой в один ньютон, равномерно распределяющейся по плоской к ней поверхности с площадью в один квадратный метр.
Рассмотрим, как конвертируются единицы измерения:
- 1 Па = 1Н/м2.
- 1 МПа = 1 н/мм2.
- 1 н/мм2 = 10кгс/см2.
Как подтянуть ступичный подшипник
Для проведения профилактических и ремонтных работ принято использовать динамометрический ключ. Такая практика существует в СТО. В конструкцию ключа вмонтирован прибор со шкалой. Зная нужный показатель, можно с легкостью затянуть гайку. Главное не переусердствовать, так как можно сорвать резьбу на крепежном элементе.
В зависимости от модификации ключа, установлены различные ограничители:
- нерегулируемый;
- с регулировкой;
- с показателем затяжки;
- с установленным цифровым дисплеем.
В зависимости от выбранного типа динамометрического ключа проводится регулировка ступичных подшипников.
Часто владельцы задают вопрос: можно ли подтягивать ступичные подшипники без фактического наличия динамометрического ключа. Запретить нельзя, но и не рекомендовано. Так как можно не рассчитать усилие. Последствия такой затяжки очевидны: люфт и преждевременный выход из строя.
Теперь Вы знаете, как отрегулировать ступичный подшипник своими силами. Несмотря на всю простоту действий и конструкцию механизма, рекомендовано обслуживать свое техническое средство в специализированных автомастерских во избежание негативных последствий и повреждения смежных деталей.
Перед тем, как проводить профилактические мероприятия, не забывайте приобретать только качественные и оригинальные комплектующие, рекомендованные или одобренные самым изготовителем. Это позволит увеличить срок эксплуатации технического средства и сократить до минимума количество поломок.
Источник: automorum.ru
Моменты затяжки резьбовых соединений
Ниже приведена таблица затяжки болтов динамометрическим ключом.
Прочность болта, в Нм | |||
Размер резьбы | 8.8 | 10.9 | 12.9 |
М6 | 10 | 13 | 16 |
М8 | 25 | 33 | 40 |
М10 | 50 | 66 | 80 |
М12 | 85 | 110 | 140 |
М14 | 130 | 180 | 210 |
М16 | 200 | 280 | 330 |
М18 | 280 | 380 | 460 |
М20 | 400 | 540 | 650 |
Таблица усилия затяжки болтов для дюймовой резьбы стандарта США для крепежных деталей SAE класса 5 и выше.
Дюймы | Нм | фунт |
¼ | 12±3 | 9±2 |
5/16 | 25±6 | 18±4,5 |
3/8 | 47±9 | 35±7 |
7/16 | 70±15 | 50±11 |
½ | 105±20 | 75±15 |
9/16 | 160±30 | 120±20 |
5/8 | 215±40 | 160±30 |
¾ | 370±50 | 275±37 |
7/8 | 620±80 | 460±60 |
1 ньютон метр (Нм) равняется 0,1кГм.
ISO -Международный стандарт.
Важность правильной затяжки болтов или гаек ГБЦ
Головка блока цилиндров (ГБЦ) — один из важнейших узлов автомобиля. Она закрывает блок цилиндров. В ней расположены распределительные валы, клапанные крышки и другие детали газораспределительного механизма. На ГБЦ постоянно воздействуют огромные переменные силы давления и температуры. Поэтому к её резьбовому креплению предъявляются особые требования.
Читать также: Кромочный фрезер для снятия свесов
Головка блока постоянно должна испытывать силу сжатия, которая задаётся определённым моментом затяжки резьбового крепления. Для того чтобы сила сжатия была равномерно распределена по поверхностям стыка головки с блоком цилиндров предусмотрено большое количество стяжных болтов или шпилек с гайками. Равномерность прижатия ГБЦ к блоку цилиндров обеспечивается определённой схемой порядка затяжки резьбовых соединений. Для уплотнения стыка используется прокладка головки блока, сделанная из особого материала, устойчивого к высокой температуре. При затяжке крепления головки она даёт усадку в тысячные доли миллиметра, что обеспечивает надёжную герметизацию стыка.
Соблюдения правильного порядка затяжки болтов ГБК гарантирует правильность её прижатия к блоку цилиндров
Последствия от перетяжки болтов крепления ГБЦ
Если затяжка резьбовых соединений головки блока ведётся с превышением усилия от номинального, то сила растяжения, которая воздействует на болт или шпильку, начнёт разрушать резьбу в блоке или вытягивать тело крепёжного элемента. Наступает так называемый момент текучести, когда при дальнейшем увеличении силы затяжки сила прижатия начнёт уменьшаться. Итог: быстрое прогорание прокладки в месте наихудшего сжатия.
Если же резьба в отверстиях блока будет сильно повреждена, то она уже не сможет обеспечить необходимое прижатие головки при правильном моменте затяжки. Её потребуется восстанавливать, а это дополнительные затраты. Опытные ремонтники мотористы на практике чувствуют предельную силу затяжки, которую может выдержать резьбовое соединение. Они никогда не допустят дефектов от перетяжки болтов или гаек.
Работа динамометрическим ключом
Что будет, если недостаточно затягивать болты крепления ГБЦ
Если крепление головки выполняется с минимальным усилием, то это приведёт к слабому прижатию её к поверхности блока цилиндров. Между прокладкой и прилегающими к ней плоскостями блока и головки образуются микроскопические зазоры, которые обязательно приведут к прогоранию уплотняющего материала.
Проверка плосткости головки блока специальной линейкой
Недостаточная затяжка болтов крепления не обеспечивает нормального прилегания головки, что может вызвать коробление её стыковой поверхности.
Моменты затяжки ленточных хомутов с червячным зажимом
В нижеуказанной таблицеприведены данные для первоначальной установки на новом шланге, а также для повторной затяжки уже обжатого шланга.
Размер хомута | Нм | фунт / дюйм |
16мм — 0,625 дюйма | 7,5±0,5 | 65±5 |
13,5мм — 0,531 дюйма | 4,5±0,5 | 40±5 |
8мм — 0,312 дюйма | 0,9±0,2 | 8±2 |
Момент затяжки для повторной стяжки | ||
16мм | 4,5±0,5 | 40±5 |
13,5мм | 3,0±0,5 | 25±5 |
8мм | 0,7±0,2 | 6±2 |
Динамометрический ключ своими руками
При ремонте автомобиля практически у каждый автолюбитель сталкивается с проблемой затянуть резьбовое соединение с определенной силой, а динамометрического ключа нет. А стоит такой не малых денег. Вот и столкнулся с такой проблемой, на покупку денег нет, а очень нужен. Принял решение об изготовлении такого ключа. И так начнем.
Для изготовления динамометрического ключа (далее ДМК) мне понадобится следующие:
- старый ключ-трещотка
- шестигранный ключ на 10 мм.
- две гайки на 8 мм.
- весы с цифровым циферблатом до 40 кг. (покупал здесь)
- кусок полосы 4*40 мм
- сварочный аппарат
- УШМ (болгарка)
- плоскогубцы, молоток, напильник и другой слесарный инструмент.
Разбираю трещотку и убираю из нее механизм фиксации, он мне не понадобится.
Отрезаю ключ шестигранник как показано на фото
Теперь привариваю шестигранник к головке трещотки таким образом чтобы ручка ключа и шестигранник в собранном состоянии были параллельны.
Перехожу к изготовлению крепления для весов. Мне понадобится железная полоса 4*40 мм. длинной 11 см. Делаю прорезь для крючка весов. Оставшиеся «усы» загибаю под углом 90 градусов. Чтобы ровно и легко согнуть полосу, я сделал надрез примерно до половины затем согнул и заварил. Вот так у меня получилось:
Теперь привариваю крепление к ручке ключа.
К шестиграннику привариваю две гайки. Две потому что шестигранник оказался короткий, таким образом решил удлинить. За гайку будет цепляться крючок весов. Мой ДМК практически готов, можно приступать к сборке.
И покраске
Осталось дождаться пока краска высохнет и крепить весы. Краска высохла. Закрепил весы и вот что получилось.
Это еще не все, осталось произвести расчет. При каких показаниях весов будет тот или иной момент затяжки. Это и есть главный минус самодельного ДМК.
Из школьного курса физики нам известно: 1 Н (Ньютон) = 0,1019716212978 кг. 1 кг. = 9.806649999999 Н (Ньютонов).
Момент затяжки можно рассчитать по следующей формуле: кгс•м = m / (1 / L) где: кгс•м – килограмм силы на метр (прилагаемое усилие в килограммах) m – показания весов L – длина плеча в метрах (расстояние от центра болта до крепления весов)
Чтобы перевести прилагаемое усилие в Ньютоны нужно: Н•м = кгс•м * 9,81 где: Н•м – Ньютон на метр кгс•м – килограмм на метр силы
Чаще всего момент затяжки пишут в Ньютонах, а наш ДМК показывает усилие в килограммах. Например, мне нужно затянуть гайку с усилием в 20 Н. для того что бы узнать какие показания должны быть на весах воспользуемся формулой
: m = Н * 0,102 * (1 / L) где: m – показания весов Н – момент затяжки с которым нужно затянуть резьбовое соединение L – длина плеча в метрах (расстояние от центра болта до крепления весов).
m = 20 * 0.102 * (1 / 0.114) = 17.89 кг.
Отсюда следует, чтобы затянуть гайку с усилием 20 Н на весах должно быть 17,89 кг.
Сделал не большую таблицу в Excel с формулами, можно скачать здесь. Для удобства можно составить таблицу с нужными значениями, тогда не нужно будет каждый раз высчитывать.
Заключение Конечно данный ключ не подойдет для использования на СТО, а для дома вполне не плохо. Характеристики данного ключа не большие. Плечо 11,4 см, максимальный момент затяжки получился 4,5 кг или 44 Н. Данные характеристики можно улучшить изменив размеры ключа или установить более мощные весы. Собирал данный данный ключ из того что было. Надеюсь вам понравилась данная самоделка.
Доставка новых самоделок на почту Получайте на почту подборку новых самоделок. Никакого спама, только полезные идеи!
*Заполняя форму вы соглашаетесь на обработку персональных данных
Становитесь автором сайта, публикуйте собственные статьи, описания самоделок с оплатой за текст. Подробнее здесь.
Таблицы разболтовок колесных дисков и подбор по маркам автомобилей
Многим автомобилистам время от времени приходится сталкиваться с непростой задачей – разболтовкой колесных дисков, что напрямую влияет на безопасность передвижения. Поэтому автолюбителям стоит уделять разболтовке колесных дисков предельное внимание. При несоблюдении параметров правильной установки относительно оси колесный диск недостаточно надежно фиксируется, не достигается оптимальное значение момента затяжки.
Основными критериями, на которые следует ориентироваться при выполнении работы, являются количество болтов и диаметр окружности посадочных мест. Среди водителей популярно сразу несколько способов определения последнего параметра. Однако не все способы можно назвать эффективными.
Наиболее простым и понятным является следующий прием:
- Сначала необходимо установить расстояние между стенками отверстий при помощи штангенциркуля.
- Затем нужно прибавить к определенному значению диаметр отверстия для фиксации.
Полученный размер будет определять расстояние между соседними отверстиями.
Большое количество автомобилистов подгоняет разболтовку под новые диски, диаметр которых немного больше исходного варианта. При монтаже таких изделий в ход идут центровочные кольца.
Основная задача владельца авто – подобрать колесные диски оптимальной массы и прочности. Последний фактор играет определяющую роль, поскольку колеса постоянно воспринимают серьезную нагрузку и удары. Также не стоит пренебрегать балансировкой, которая позволит избежать биения дисков во время движения.
Разболтовка производится при строгом соблюдении трех главных параметров:
- PCD – диаметр окружности;
- ET – вылет диска;
- DIA – диаметр центрального отверстия.
Для каждой модели авто болты крепления колеса подбираются по уникальной комбинации трех показателей. При выборе определенных дисков и болтов необходимо опираться на данные таблицы. Пример значений:
Отечественные авто
Audi
BMW
Ford
Hyundai
Пример разболтовки:
Как затянуть ступичную гайку нужным моментом
Для затягивания резьбовых соединений, где рекомендуется соблюдать определённый момент, используют специальные динамометрические ключи. Внутри инструмента расположен динамометр со шкалой или специальное устройство с ограничителем, которое срабатывает при достижении требуемой силы затягивания. Ключи так же бывают с интервалами значений, например 5-25 (минимум 5 Н•м, максимум 25 Н•м). Резьбовое соединение затягивают до тех пор, пока стрелка не покажет необходимую величину или не сработает ограничитель. Имеются так же дорогие и точные аналоги – с электронным дисплеем, но для эксплуатации и ремонта легковых авто подойдёт механический вариант.
На фото представлены основные виды таких ключей.
- С предустановленным моментом, не регулируемые.
- С предварительно настроенной величиной момента, регулируемые.
- С индикатором усилия при затяжке.
- С цифровым дисплеем прилагаемой силы закручивания.
Посмотрите видео как пользоваться динамометрическим инструментом:
Процесс затягивания колесных болтов: поэтапные действия
Чтобы конструкции надежно были зафиксированы с необходимым моментом, существует специальная таблица затяжки болтов динамометрическим ключом. Например, если их количество четыре (1-3-4-2), 5 болтов (1-4-2-5-3) или 6 болтов (1-4-5-2-3-6).
Сам процесс осуществляется следующим образом:
- Требуется надеть колесо на выступ центральной части ступицы, и поставить направляющие шпильки напротив соответствующих отверстий.
- Далее придется вручную закрутить болты достаточно крепко, чтобы колесо не соскочило с места.
- После выполнения всех действий необходимо взять инструмент с выставленным моментом и затянуть колеса в правильном порядке.
Смазка колесных дисков
Существует несколько проблем, с которыми автолюбители сталкиваются. Прежде всего, это ржавчина. Со временем коррозия повреждает не только резьбу, но и саму шляпку. Однако эта проблема не касается тех метизов, которые с завода покрыты антикоррозийным составом.
Довольно часто болты прикипают. Это явление делает затруднительным использование электрического гайковерта. Сложно откручивать метизы и вручную. Когда головка болта при откручивании обламывается, многие владельцы транспортных средств говорят о недостаточном уровне смазки. Но относительно целесообразности применения смазочных материалов для резьбовой части колесных болтов ведутся споры. Одни автовладельцы утверждают, что смазывающие составы позволяют значительно продлить срок службы болтов. Другие являются противниками использования различных смазок для колесных болтов, поскольку считают, что масло может способствовать раскручиванию метизов во время движения авто.
Колесные болты обрабатывают смазывающими материалами, чтобы избежать коррозии и прикипания. Слой смазки препятствует негативному влиянию воды и воздуха, так как результатом такого взаимодействия может быть закисание и чрезмерная фиксация болтов в ступице.
Но большое количество смазки снижает уровень трения. Возможным также является и ослабление крепежа в результате применения смазывающего состава. Это основная причина, почему нельзя смазывать колесный болт. В результате постоянного воздействия вибрации метизы откручиваются, и потеря колеса на ходу становится неизбежной.
На практике такие ситуации происходят редко. К примеру, причиной чрезмерной фиксации крепежей является перетяжка во время предыдущего обслуживания колес. Водители могут самостоятельно дотянуть метиз до того уровня, когда демонтаж подручными средствами становится невозможным. Подобную ошибку допускают и специалисты на сервисных станциях. Используя гайковерты для колесных болтов, они не рассчитывают возможности пневматических устройств.
Смазка не является основной причиной откручивания метизов. Конусная часть болта предназначена для выполнения сразу нескольких функций:
- Центрируется колесо.
- Плотно фиксируется диск.
- Конус при монтаже создает клин, препятствующий самопроизвольному откручиванию на ходу.
Многие эксперты утверждают, что смазкой пользоваться можно. Это необязательная процедура, однако, состав может защитить резьбу от появления коррозии.
Практическое применение: как правильно пользоваться инструментом
Индикаторные приборы не вызывают сложностей. Вы просто читаете показания, и видите крутящий момент. А вот щелчковый механизм требует привыкания и правильного понимания разметки шкалы. Грубые показания нанесены на неподвижный стержень рукоятки. Точные деления на поворотной части.
На иллюстрации изображены метки в 98 Nm и 2 Nm (на поворотной ручке). Значения складываются: итоговый показатель – 100 Nm. Чтобы протянуть таким динамометрическим ключом болты колес автомобиля (например, значение 120 Nm), необходимо выставить 112 Nm на неподвижной рукоятке и 8 Nm на поворотной части.
Если понять общий принцип, пользоваться инструментом будет удобно.
Существуют различные варианты исполнения разметки:
При этом для всех типов рукояток есть общее правило: на торце откручивается стопорное колесико, производится установка значения, после чего крепление механизма снова затягивается. Большинство динамометрических ключей такого типа, устроены еще проще.
Прокручивания трещотки не происходит, вы просто слышите громкий щелчок. Принципиально, это ничего не меняет: просто после характерного звука следует прекратить затяжку.
Моменты затяжки болтов и гаек указываются в инструкциях по ремонту и обслуживанию автомобиля. Таблица не универсальна: крепеж с одинаковой метрической размерностью, на различных узлах может иметь разные показатели.
Даже усилие затяжки колесных болтов на автомобилях одного производителя (собранных на одной платформе) может отличаться. Например, Volkswagen Passat – 120 Nm, а одноплатформенный Volkswagen Sharan – 170 Nm.
Крайне желательно соблюдать заводские установки, иначе можно повредить узлы и детали. Но бывают ситуации, когда информация не доступна. В таких случаях поможет таблица затяжки болтов динамометрическим ключом.
Закручиваем болты правильно
Любое резьбовое соединение рассчитано на определённый момент затяжки. Он регламентирован отраслевыми стандартами качества, например, «ОСТ 37.001.050–73 Затяжка резьбовых соединений. Нормы затяжки» и руководящими документами заводов-изготовителей транспортных средств. Иностранные производители используют другие стандарты, но в основном они сходны с отечественными. Приведённая ниже информация будет излагаться, опираясь на российские стандарты.
До какой степени можно затягивать резьбовые соединения
Почему важно выдерживать правильный момент затяжки? Только грамотное затягивание обеспечит надёжную фиксацию детали, с одной стороны, и предотвратит повреждение резьбы и/или самой детали — с другой стороны.
Рассмотрим, что произойдёт при превышении момента затяжки на примере болта с гайкой:
Гайки момент затяжки
Расчет момента затяжки гайки
Определенная степень закрутки резьбовых элементов выполняется с целью увеличения срока службы, прочности и повышению сопротивления различным влияющим факторам. Для каждого крепежного элемента есть определенная степень затяжки на каждом посадочном месте, рассчитывается она на основе нагрузок, температурных режимов и свойств материалов.
Например, при воздействии температуры металлу свойственно расширяться, при условии влияния вибрации — крепеж получает дополнительную нагрузку, и чтобы минимизировать ее, закручивать нужно с правильным усилием. Рассмотрим силу затяжки болтов, таблицы, методы и инструменты для проведения работ
Маркировка деталей
Этот параметр указывается на головке болта. Для деталей, выполненных на основе углеродистой стали с классом прочности — 2, указываются цифры через точку, например: 3.5, 4.8 и т. д.
Первая цифра указывает 1/100 номинального размера прочностного предела на разрыв, измеряется в МПа. Например, если на головке болта, указано — 10.1, то первое число означает 10*100 = 1000 МПа.
Вторая цифра — отношение пределов текучести к прочности, умножается на 10, по вышеуказанному примеру — 1*10*10= 100 МПа.
Предел текучести — это максимальная нагрузка на болт. Для элементов, выполненных из нержавеющей стали, наносится тип стали А2 или А4, и далее предел прочности. Например: А4—40. Число в данной маркировке характеризует 1/10 предела прочности углеродистой стали.
Единицы измерения
Основной величиной является Паскаль, единица измерения давления, механического напряжения, согласно международной системе «СИ». Паскаль равняется давлению, вызванному силой в один ньютон, равномерно распределяющейся по плоской к ней поверхности с площадью в один квадратный метр.
Рассмотрим, как конвертируются единицы измерения:
- 1 Па = 1Н/м2.
- 1 МПа = 1 н/мм2.
- 1 н/мм2 = 10кгс/см2.
Моменты затяжки резьбовых соединений
Ниже приведена таблица затяжки болтов динамометрическим ключом.
Прочность болта, в Нм | |||
Размер резьбы | 8.8 | 10.9 | 12.9 |
М6 | 10 | 13 | 16 |
М8 | 25 | 33 | 40 |
М10 | 50 | 66 | 80 |
М12 | 85 | 110 | 140 |
М14 | 130 | 180 | 210 |
М16 | 200 | 280 | 330 |
М18 | 280 | 380 | 460 |
М20 | 400 | 540 | 650 |
Таблица усилия затяжки болтов для дюймовой резьбы стандарта США для крепежных деталей SAE класса 5 и выше.
Дюймы | Нм | фунт |
¼ | 12±3 | 9±2 |
5/16 | 25±6 | 18±4,5 |
3/8 | 47±9 | 35±7 |
7/16 | 70±15 | 50±11 |
½ | 105±20 | 75±15 |
9/16 | 160±30 | 120±20 |
5/8 | 215±40 | 160±30 |
¾ | 370±50 | 275±37 |
7/8 | 620±80 | 460±60 |
1 ньютон метр (Нм) равняется 0,1кГм.
ISO -Международный стандарт.
Моменты затяжки ленточных хомутов с червячным зажимом
В нижеуказанной таблицеприведены данные для первоначальной установки на новом шланге, а также для повторной затяжки уже обжатого шланга.
Размер хомута | Нм | фунт / дюйм |
16мм — 0,625 дюйма | 7,5±0,5 | 65±5 |
13,5мм — 0,531 дюйма | 4,5±0,5 | 40±5 |
8мм — 0,312 дюйма | 0,9±0,2 | 8±2 |
Момент затяжки для повторной стяжки | ||
16мм | 4,5±0,5 | 40±5 |
13,5мм | 3,0±0,5 | 25±5 |
8мм | 0,7±0,2 | 6±2 |
Как определить момент затяжки
- С помощью динамометрического ключа.
Этот инструмент должен быть подобран таким образом, чтобы момент затяжки крепежного элемента был на 20−30% меньше, чем максимальный момент на вашем ключе. При попытке превысить предел, ключ быстро выйдет из строя.
Усилие на затяжку и тип стали указывается на каждом болте, как расшифровывать маркировку описывалось выше. Для вторичной протяжки болтов нужно учитывать несколько правил:
- Всегда знать точное необходимое усилие для затяжки.
- При контрольной проверке затяжки стоит выставить усилие и проверить в круговом порядке все крепежные элементы.
- Запрещено использовать динамометрический ключ как обычный, им нельзя производить закрутку деталей, гайку или закручивать болт до примерного усилия, контрольная протяжка производится динамометрическим ключом.
- Динамометрический ключ должен быть с запасом.
- Без динамометрического ключа.
Для этого потребуется:
- Ключ накидной или рожковый.
- Пружинный кантер или весы, с пределом в 30 кг.
- Таблица, в которой указывается усилие затяжки болтов и момент затяжки гаек.
Момент затяжки — это усилие, приложенное на рычаг размерами в 1 метр. Например, нам требуется затянуть гайку с усилием 2 кГс/м:
- Измеряем длину нашего накидного ключа, она, к примеру, составила 0,20 метра.
- Делим 1 на 0,20 получаем цифру 5.
- Умножаем полученные результаты, 5 на 2кГс/м и получаем в итоге 10 кг.
Переходя к практике, берем наш ключ и весы, прикрепляем крючок к ключу и производим затяжку до нужного веса, согласно описанного выше расчета. Но даже такой способ в итоге окажется лучше, чем тянуть от «руки — на глаз», с погрешностью, чем выше усилие, тем она меньше. Это будет зависеть от качества весов, но лучше все-таки приобрести специальный ключ.
При проектировании, сборке и монтаже узлов, очень важно учитывать момент затяжки болтов. Момент затяжки болта контролируется динамометрическим ключом, а назначается исходя из определённых условий.
Читайте также: Сварочный полуавтомат трансформаторного типаТребуемое осевое усилие болта
По сути, момент затяжки болта создает силу прижатия поверхностей. Усилие очень важно, так как соединения бывают разные, в некоторых случаях важно прижать поверхности, например при контакте метал-метал, а в некоторых излишнее усилие может навредить соединению, например установка крышки через резиновую прокладку, или установка пластиковой детали на металлический каркас.
Сначала конструктор определяет необходимое усилие прижатия поверхностей, затем определяет диаметр болтов или их количество. О том, как определить диаметр и количество, я рассказывал в уроке «Расчет болтов». Затем назначается момент затяжки. Тут есть маленькая хитрость: Когда требуется небольшое усилие (прокладка или пластик), лучше назначить чуть больше болтов меньшего диаметра, что позволит их расположить с меньшим шагом и более равномерно прижать поверхности. И, чем ближе момент затяжки болта к рекомендуемому значению, тем меньше шансов, что произойдет самопроизвольное откручивание.
Прочность болта
Рекомендуемые значения затяжки болтов назначаются из условия прочности болтов. В уроке «Прочность болтов» я рассказывал про прочность, какие бывают болты и как маркируются. Обычно рекомендуемый момент затяжки обеспечивает осевое усилие болта в 2/3 от предела текучести, то есть затянутый болт будет иметь запас прочности.
Ниже представлена таблица для затяжки болтов и гаек со стандартным шагом метрической резьбы.
Как видим из таблицы, момент затяжки любого болта прочностью 12.9 в разы выше момента затяжки болта класса прочности 4.6. Обращаю Ваше внимание, что данные моменты затяжек действуют только для болтов и гаек из углеродистых сталей со стандартным шагом. Ни в коем случае нельзя затягивать с такими значениями в алюминиевый или чугунный корпус. Данная таблица также не распространяется на самоконтрящиеся гайки и на элементы с мелким шагом резьбы.
Контроль момента затяжки болтов
Как я писал выше, требуемый момент затяжки обеспечивается динамометрическим ключом или иным настраиваемым инструментом (пневматический или электрический гайковерт). При затяжке обращаем внимание на качество резьбы, следим, чтобы гайка или болт закручивались от усилия пальцев и без закусывания.
Иногда, при осуществлении контролируемой затяжки, смазывают резьбу и поверхность под головкой болта или гайки. Раскрутить соединение обычно сложнее, может понадобиться значительно больший момент. Связано это с деформациями, окислением между болтом и поверхностью, коррозией в резьбе. Если требуется проверить, с нужным моментом затянут болт или нет, достаточно просто настроить ключ и попробовать подтянуть болт.
Читайте также: Как разобрать ударную отверткуВ соединениях с несколькими болтами, контролируемая затяжка осуществляется в несколько приёмов, о том, как это сделать, я расскажу в уроке «Порядок затяжки болтов».
Прочитав данный урок, Вы знаете, с каким усилием можно тянуть болты в обычных соединениях. Помимо простых соединений, меня часто спрашивают какой момент затяжки болтов ГБЦ (головки блока цилиндров) и некоторых других ответственных узлов. Этому вопросу будет посвящен отдельный урок.
В одной из следующих статей мы более подробно обсудим момент затяжки гаек на конкретных примерах, а на сегодня все, спасибо за внимание.
РАСЧЕТ МАКСИМАЛЬНО-ДОПУСТИМОГОГО МОМЕНТА ЗАТЯЖКИ МЕТРИЧЕСКОЙ РЕЗЬБЫ
Номинальный диаметр (D, d), диаметр цилиндра, описанного вокруг вершин наружной (d) или впадин внутренней резьбы (D).
Шаг (P) — расстояние между одноимёнными боковыми сторонами профиля, измеряется в долях метра. Выражается числом от 0.25 до 6.
Размер (S) рабочего профиля ключа, который охватывает крепежную деталь.
Длина свинчивания (Lсв) — длина (высота) соприкосновения поверхностей болта и гайки (детали), измеренная вдоль оси.
Механические свойства болтов, крепёжных винтов и шпилек из углеродистых нелегированных и легированных сталей по ГОСТ 1759.4-87 (ISO 898/1-78) при нормальных условиях характеризуют 11 классов прочности: 3.6; 4.6; 4.8; 5.6; 5.8; 6.6; 6.8; 8.8; 9.8; 10.9; 12.9. Первое число умноженное на 100, определяет номинальное временное сопротивление в Н/мм?, второе число (отделённое точкой от первого) умноженное на 10, — отношение предела текучести к временному сопротивлению в процентах. Произведение чисел, умноженное на 10, определяет номинальный предел текучести в Н/мм?.
Коэффициент запаса прочности (коэффициент безопасности) вводится для того, чтобы обеспечить безопасную, надежную работу соединений, несмотря на возможные неблагоприятные отклонения действительных условий их работы от расчетных.
Основной характеристикой трения является коэффициент трения, который определяется материалами, из которых изготовлены поверхности взаимодействующих тел.
Разрушение резьбового соединения при перезатяжке может произойти либо вследствие разрыва стержня болта, либо из-за срыва резьбы гайки и (или) болта. Разрушение стержня болта происходит внезапно и легко может быть обнаружено. Срыв резьбы гайки происходит постепенно, его труднее обнаружить, поэтому имеется опасность наличия в соединениях частично разрушенных крепежных изделий, Представляется целесообразным конструировать резьбовые соединения таким образом, чтобы возможное разрушение всегда имело место по стержню болта. Однако, чтобы гарантировать такой вид разрушения во всех случаях, потребуется непомерно большая высота гайки из-за наличия многих переменных факторов, влияющих на стойкость резьбы к срыву.
Момент затяжки гаек
Момент затяжки гаек также важен, как и момент затяжки болтов, ведь в некоторых ситуация мы затягиваем болт, а в некоторых гайку. Чем отличается затяжка гайки от затяжки болта? Отличий не так много. В соединении действуют те же самые силы трения в резьбе и между гайкой с поверхностью. Отличия только в том, что иногда, если резьба болта выступает на большое количество витков над гайкой, не удаётся воспользоваться головкой. При соединении болт-гайка, приходится один из элементов удерживать ключом, а второй затягивать. В остальном процесс ничем не отличается от закручивания болта в резьбовое отверстие. Поэтому для гаек можно использовать момент затяжки болтов, за исключением случаев, когда момент затяжки гайки оговорен инструкцией, или же гайка имеет исполнение, предотвращающее откручивание. Обычно такие гайки дают повышенное сопротивление при закручивании, поэтому момент затяжки нужно смотреть в инструкции к таким гайкам.
Куда интереснее момент затяжки колесных гаек, уделим внимание этому вопросу. Честно говоря, ни разу не видел, чтобы кто-то на своём авто менял колесо и пользовался динамометрическим ключом, а вот в сервисах, практически во всех, момент затяжки колесных гаек контролируют либо ключом, который не имеет настройки, но щелкает при достижении требуемой нагрузки, либо затягивают пневматическим пистолетом с определенным моментом. Я и сам ни разу не тянул колесные болты/гайки динамометрическим ключом. Знающие люди вообще утверждают, что в комплекте с новым автомобилем идёт ключ, длинна, которого рассчитана так, чтобы среднестатистический мужчина руками (не прыгая на ключе) затягивал гайки до нужного момента и при этом не вредил резьбу. Я не знаю, как затягиваете колесные гайки Вы, но на всякий случай выложу таблицу с указанием положенных моментов.
Допускается погрешность затяжки 10%. Порядок затяжки болтов рассматривали в одной из прошлых статей.
Теперь затронем такую тему, как момент затяжки ступичной гайки. Ступичная гайка имеет определенный момент затяжки, и тут немного сложнее, чем с затяжкой колесных гаек. Сильно затянутая, ровно, как и слабо затянутая гайка, приведёт к повышенному износу подшипника. Автолюбители предпочитают затягивать по ощущениям, оставляя маленький люфт, но гайка ступицы все же имеет благоприятный момент затяжки, при котором ресурс подшипника будет максимальным. На современных автомобилях в ступицах стоят подшипники, ресурс которых практически не зависит от силы затяжки и просто осуществляется затяжка гайку ШРУСа. Ниже приведена таблица, в которой отображен момент затяжки гайки ступицы.
Если на ШРУСе машины есть паз под юбку гайки (юбка гайки заминается в паз), то подшипник нечувствителен к затяжке и, можно затягивать гайку около 100-150 Ньютонов. В любом случаи, после затяжки гайки, обязательно проверяем вращение колеса, колесо должно легко крутиться от руки и иметь минимальный люфт, или не иметь люфта вовсе. Гайку затягиваем плавно и без рывков, постоянно контролируя вращение колеса. Если гайка стопорится шплинтом, и отверстие под шплинт не совпадает с зубцами гайки, то немного ослабляем гайку до совпадения. Неверно затянутая гайка даст о себе знать нагревом ступицы или сильным люфтом колеса поэтому, после затяжки и пробега 2-3 километра, рекомендуется проверить состояние подшипника и ступицы, убедиться, что нет большого люфта и повышенного нагрева ступицы.
А как Вы затягиваете колесные и ступичные гайки? На этом всё! Интересующие Вас вопросы задавайте в комментариях.
Моменты затяжки болтов и гаек — DRIVE2
Зная собственную мускульную силу и размеры инструментов, можно приблизительно рассчитать моменты усилий затяжки болтов и гаек.
На предмет массой 1 кг действует сила тяжести, равная 1 кгс. В новой системе мер 1 кгс соответствует 9,8 Н (ньютона). Другими словами, на предмет массой 1 кг действует динамическое ускорение 9,8 м/с2.
На рисунках показана зависимость значения момента затяжки от длины рычага. В первом случае к концу ключа прикладывается усилие 10 кг. Длина ключа равна 10 см. Таким образом, на болт действует момент затяжки, равный 10 Нм. Если длину ключа увеличить в два раза, а усилие оставить неизменным, то на болт будет действовать в два раза больший момент, т. е. 20 Нм.
Обычно момент затяжки указывается в Нм. В Руководстве по ремонту крутящий момент также указывается в фунтах или фунт-сила-фут. При большом количестве разнообразных деталей, закрепленных с помощью болтов и гаек, важное значение приобретают правильные значения моментов затяжки. Для затяжки болтов и гаек определенным моментом используется динамометрический ключ.
Таблица нормативных моментов затяжки резьбовых соединений
1. | Таблица моментов затяжки для болтов и гаек a Если нет специальных указаний, затягивайте гайки и болты с метрической резьбой до мо’ |
мента, указанного в таблице ниже. a Приводимая ниже таблица применима к болтам, показанным на рис. А.
2. Таблица моментов затяжки болтов фланцевых соединений a Если нет особых указаний, при затяжке болтов фланцевых соединений пользуйтесь нор’ мативами, приведенными ниже.
3. Таблица моментов затяжки втулок трубных соединений с уплотнительным кольцом a Если нет особых указаний, при затяжке втулок разъемов трубопроводов с уплотнительным кольцом пользуйтесь нормативами, приведенными ниже.
4. Таблица моментов затяжки заглушек с уплотнительным кольцом a Если нет особых указаний, при затяжке заглушек с уплотнительным кольцом пользуйтесь нормативами, приведенными ниже.
5. Таблица моментов затяжки для шлангов (с коническим и торцевым уплотнениями) a Если нет особых указаний, при затяжке шлангов (с коническим и торцевым уплотнениями) пользуйтесь нормативами, приведенными ниже a Приведенные ниже моменты применяются при нанесении на резьбу моторного масла.
6. Таблица моментов затяжки для соединений с торцевым уплотнением a Затягивайте соединения с торцевым уплотнением (накидные гайки) на трубах низкого давления из плакированной стали, используемые на двигателях, до моментов, представ’ ленных в следующей таблице. a Прикладывайте следующие моменты затяжки к соединениям с торцевым уплотнением, предварительно нанеся на их резьбовые участки слой моторного масла.
Для справки: В зависимости от конкретных технических характеристик используются соединения с торцевым уплотнением, размеры которых указаны в скобках ( ).
7. Таблица моментов затяжки для двигателей серии 102, 107 и 114 (болты и гайки) a Если нет особых указаний, при затяжке болтов и гаек с метрической резьбой на
двигателях серии 102, 107 и 114 пользуйтесь нормативами, приведенными ниже.
8. Таблица моментов затяжки для двигателей серии 102, 107 и 114 (шарнирные соединения) a Если нет особых указаний, при затяжке шарнирных соединений с метрической резьбой на двигателях серии 102, 107 и 114 пользуйтесь нормативами, приведенными ниже.
9. Таблица моментов затяжки для двигателей серии 102, 107 и 114 (Винты с конической резьбой) a Если нет особых указаний, при затяжке винтов с конической резьбой (ед. изм: дюйм) на двигателях серии 102, 107 и 114 пользуйтесь нормативами, приведенными ниже.
Моменты затяжки основных резьбовых соединений
МОМЕНТЫ ЗАТЯЖКИ ОСНОВНЫХ РЕЗЬБОВЫХ СОЕДИНЕНИЙ ПРИ ТЕХНИЧЕСКОМ ОБСЛУЖИВАНИИ И РЕМОНТЕНаименование | Момент затяжки, Н-м (кгс-м) | Примечание |
Двигатель | ||
Болты крепления: | ||
головок цилиндров | 186-206 (19-21) | М16 |
крышек коренных подшипников коленчатого вала: -вертикальные М16 -стяжные | 275-295 (28-30) 147-167 (15-17) | |
картера маховика | 43,1-54,9 (4,4-5,6) 88-108 (9-11) | для М10 для М12 |
направляющих толкателей | 73,3-93,2 (7,3-9,5) | |
фланца оси ведущей шестерни привода распределительного вала | 49-60,8 (5-6,2) 88,3-98 (9-10) | для М10 для М12 |
масляного картера | 8-17,8 (0,8-1,8) | М8 |
радиатора системы охлаждения на раме | 54-59 (5,5-6,0) | |
корпуса масляного фильтра теплообменника к блоку цилиндров | 88-122 (9-12,5) | |
выпускных коллекторов | 43-55 (4.4-5,6) | М10 |
корпуса компрессора | 4.9-7,8 (0,5-0,8) | М6 |
корпуса турбины | 23,5-29,4 (2,4-3) | М8 |
Гайки: | ||
крепления стоек коромысел | 41-53 (4,2-5,4) | М10 |
регулировочного винта коромысла | 33-41 (3,4-4.2) | М10 |
скобы крепления форсунки | 31-39 (3,2-4,0) | М10 |
крепления муфты опережения впрыскивания топлива | 98-118 (10-12) | |
крепления турбокомпрессора | 44-56 (4,4-5,6) | |
крепления передних и задних опор силового агрегата | 54-59 (5,5-6,0) |
крепления насосного агрегата и теплообменника предпускового подогревателя | 44-53 (4,5-5.4) | |
крепления выпускной трубы | 15-25 (1,5-2,5) | |
крепления патрубков предпускового подогревателя | 44-53 (4,5-5,4) 15-25 (1.5-2,5) | для М10 для М8 |
крепления фланцев приемных труб глушителя | 44-53 (4,5-5,4) | |
болтов крепления поперечной балки поддерживающей опоры к раме | 98-137 (10-14) | |
шпилек крепления задних опор двигателя | 118-137 (12-14) | |
болтов крепления задних опор двигателя к раме | 196-265 (20-27) | |
крепления выпускных патрубков | 43-54 (4,4-5,5) | |
Винты заглушки корпуса муфты опережения впрыскивания топлива | 7.84-9,81 (0,8-1,0) | |
Гайки болтов крепления кронштейнов топливного бака к раме | 49-59 (5-6) | |
Сливная пробка картера масляного | 40-58,8 (4-6) | |
Сцепление | ||
Болты крепления: | ||
пневмоусилителя сцепления | 88-98 (9-10) | |
нажимного диска с кожухом в сборе к маховику: | 53,9-61.8 (5,5-6,3) 24.5-29,4 (2,5-3,0) | для М10 для М8 |
Коробка передач | ||
Болты крепления: | ||
кронштейна поддерживающей опоры к коробке передач | 73,5-93 (7,5-9,5) | |
картера коробки передач к картеру сцепления | 137-196 (14-20) | |
рычагов тяг дистанционного привода управления коробкой | 54-69 (5,5-7,0) | для коробки передач мод. 142, 152 |
Гайка крепления: | ||
рычага переключения передач | 39-55 (4.0-5,6) | |
фланца первичного вала коробки передач | 196-235 (20-24) |
Стяжные болты регулировочного фланца механизма переключения передач | 39-55 (4,0-5,6) | |
Карданная передача | ||
Гайка крепления фланца: | ||
вала промежуточного моста | 186-206 (18,6-20,6) | М 14 с торцевыми шлицами |
вала заднего моста | 118-132(11,8-13,2) | М 12 с торцевыми шлицами |
Мосты | ||
Болты крепления: | ||
задних крышек мостов | 35-49 (3,6-5,0) | |
крышек подшипников межколесного дифференциала | 343-392 (35-40) | |
Гайки крепления: | ||
фланца ведущего конического зубчатого колеса | 235-353 (24-36) | |
подшипников ведущего цилиндрического зубчатого колеса | 588-686 (60-70) | |
заднего фланца промежуточного моста | 245-294 (25-30) | |
фланца межосевого дифференциала | 245-294 (25-30) | |
чашек межколесного дифференциала | 137-157 (14-16) | |
главной передачи промежуточного и заднего мостов | 157-176 (16-18) | |
полуосей промежуточного и заднего мостов | 118-137(12-14) | |
Контргайки крепления подшипников ступиц: | ||
передних колес | 137-157 (14-16) | |
заднего и промежуточного мостов | 137-157 (14-16) | |
Подвеска | ||
Гайки: | ||
стремянок передних рессор | 431-539 (44-55) | для М20 |
637-735 (65-75) | для М24 | |
стремянок задних рессор | 637-735 (65-75) | для М24 |
785-883 (80-90) | для М27 | |
950-1050 (97-107) | для М30 | |
пальцев амортизаторов | 176-216(18-22) |
шпилек соединения кронштейнов осей балансира с кронштейнами задней подвески | 490-549 (50-56) | |
стяжки кронштейнов оси балансира | 490-549 (50-56) | |
пальцев реактивных штанг | 550-650 (56-66) | |
шпилек крепления верхних рычагов и кронштейнов реактивных штанг | 440-550 (44-55) | |
крепления кронштейнов задней подвески к раме | 176-216(18-22) 440-550 (44-55) | для М16 для М20 |
Болты крепления: | ||
ушков передних рессор | 314-392 (32-40) | М20 |
накладки ушка передних рессор | 49-98 (5-10) | |
Стяжные болты: | ||
проушин передних кронштейнов передних рессор | 118-157(12-16) | М14 |
задних кронштейнов передних рессор | 118-157(12-16) | М14 |
Колеса | ||
Гайки крепления бездисковых колес к ступицам | 245-294 (25-30) | |
Гайки крепления дисковых колес | 529-658 (54-67) | с центрированием по центральному отверстию в диске |
Гайки крепления держателя запасного колеса | 118-142 (12.0-14,5) | |
Рулевое управление и рулевой привод | ||
Гайки: | ||
рулевого колеса | 59-79 (6-8) | |
шаровых пальцев продольной и поперечной рулевых тяг | 276-352 (28-36) | |
болтов наконечников поперечной рулевой тяги | 47-59 (4,8-6.0) | |
крепления сошки | 490-551 (50-56) | |
Гайка регулировочного винта вала сошки | 59-64 (6,0-6.5) | |
Болты крепления: | ||
механизма рулевого управления | 245-314(25-32) 412-470 (42-48) | для механизмов мод. RBL |
крышки насоса | 43,2-54.9 (4,4-5,6) | |
рулевой колонки | 41,2-51.9 (4,2-5.3) | |
Гайки вилки карданного вала | 21.6-26,5 (2,2-2,6) 53-59 (5.4-6,0) | для механизма мод. RBL |
Магнитная пробка | 29,4-40,0 (3-4) | |
Тормозные системы | ||
болтов крепления кронштейнов тормозных камер к суппортам | 74-98 (7,5-10,0) | |
болтов крепления передних тормозных камер к кронштейнам | 137,2-176.4 (14,0-18,0) | |
болтов крепления задних тормозных камер к кронштейнам | 137,2-176.4 (14,0-18,0) | |
болтов крепления головки цилиндра компрессора | 30,0-33,0 (3.0-3,4) | |
болтов крепления осей колодок тормозного механизма | 39,2-49,0 (4,0-5,0) | |
болтов крепления грязезащитного щитка к суппорту | 17,6-23.5 (1,8-2,5) | |
крепления кронштейнов ресиверов к раме | 167,7-185,3 (17.1-18,9) | М16 |
крепления хомутов кронштейнов ресиверов | 15-25 (1,5-2,5) | |
соединений трубок пневмосистемы диаметром, мм: 6 8 12 | 9-12 (0,9-1,2) 14-21 (1.4-2,1) 15-25 (1,5-2,5) | |
Электрооборудование | ||
Гайки крепления электропроводов к выводам стартера: – цепь питания – цепь управления | 17.6-21,6 (1,8-2,2) 2.9-4,6 (0,3-0,47) | М12 М6 |
Кабина | ||
Гайки: | ||
стремянки рессоры задней опоры кабины к кронштейну | 53-77,5 (5,4-7,9) | |
опор рычагов торсионов | 150-219 (15,3-22,3) | |
кронштейнов заднего крепления кабины | 98,3-137,5 (10-14) | |
кронштейнов переднего крепления кабины к поперечине | 168-207 (17-21) | М14 |
246,5-315 (25-32) | М16 | |
Платформа | ||
Гайки: | ||
хомутов крепления брусьев платформы | 35-40 (3,5-4,0) | |
болтов крепления надрамника к раме | 68,6-98 (7-10) | для М12 |
176-216 (18-22) | для М16 | |
117,7-157 (12-15) | для М14 | |
крепления передних кронштейнов надрамника | 68,6-98 (7-10) | |
крепления ловителя-амортизатора | 117,7-147 (12-15) | |
крепления амортизатора платформы к опорам | 39,2-55 (4,0-5,6) | |
крепления гидроцилиндра | 176-216 (18-22) | |
крепления масляного насоса к коробке отбора мощности | 39-49 (4-5) | |
крепления коробки отбора мощности | 39-49 (4-5) |
Моменты затяжки резьбовых соединений классики Классика
Регистрация: 22.11.2009
Сообщения: 1209
Авто: ВАЗ-2113
Откуда: Москва
Моменты затяжки резьбовых соединений классики Руководство по ремонту и эксплуатации – Моменты затяжки резьбовых соединений ВАЗ-2101 – ВАЗ-2107 Моменты затягивания резьбовых соединенийДеталь | Резьба | Момент затягивания, Н·м (кгс·м) | ||
номинальный | минимальный | максимальный | ||
Двигатель | ||||
Болт крепления крышек коренных подшипников | М10 х 1,25 | 80,36 (8,2) | 68,31 (6,97) | 84,38 (8,61) |
Болт крепления масляного картера | М6 | 7,8 (0,8 ) | 5,4 (0,52) | 8,23 (0,84) |
Шпилька крепления крышки сапуна | М8 | 19,6 (2,0) | 16,66 (1,7) | 20,58 (2,1) |
Гайка крепления крышки сапуна | М8 | 13,72 (1,4) | 8,92 (0,91) | 14,41 (1,4) |
Болт крепления головки цилиндров: | ||||
– предварительное затягивание | М12 х 1,25 | 39,2 (4,0) | 33,3 (3,4) | 41,16 (4,2) |
– окончательное затягивание | – | 112,7 (11,5) | 95,94 (9,8 ) | 118,4 (12,1) |
Болт крепления головки цилиндров* | М8 | 37,24 (3,8 ) | 36,67 (3,13) | 39,1 (4,0) |
Гайка крепления впускного и выпускного трубопроводов | М8 | 24,5 (2,5) | 20,87 (2,13) | 25,77 (2,6) |
Гайка болта крышки шатуна | М9 х 1 | 50,96 (5,2) | 43,32 (4,42) | 53,51 (5,5) |
Болт крепления маховика | М10 х 1,25 | 83,3 (8,5) | 60,96 (6,22) | 87,42 (8,9) |
Болт крепления, башмака натяжителя цепи | М10 х 1,25 | 44,1 (4,5) | 36,75 (3,75) | 46,55 (4,7) |
Гайка шпилек крепления корпуса подшипников распределительного вала | М8 | 21,5 (2,2) | 18,33 (1,87) | 22,64 (2,3) |
Болт крепления звездочки распределительного вала и вала привода масляного насоса* | М10 х 1,25 | 48,62 (4,9) | 46,1 (4,7) | 58,8 (6,0) |
Гайка регулировочного болта клапана | М12 х 1,25 | 50,96 (5,2) | 43,3 (4,42) | 53,5 (5,46) |
Втулка регулировочного болта клапана | М18 х 1,5 | 98 (10) | 83,3 (8,5) | 102,9 (10.5) |
Свеча зажигания | М14 х 1,25 | 37,24 (3,8 ) | 30,67 (3,13 | 39 (4,0) |
Болт крепления насоса охлаждающей жидкости | М8 | 25,48 (2,6) | 21,66 (2,2) | 26,75 (2,7) |
Гайка крепления выпускного патрубка рубашки охлаждения | М8 | 21,56 (2,2) | 15,97 (1,63) | 22,64 (2,3) |
Храповик коленчатого вала | М20 х 1,5 | 119,6 (12,2) | 101,33 (10,34) | 125,6 (12,8 ) |
Болт кронштейна генератора | М10 х 1,25 | 51,94 (5,3) | 44,1 (4,5) | 58,31 (5,9) |
Гайка крепления установочной планки генератора | М10 х 1,25 | 43,12 (4,4) | 28,63 (2,9) | 45,27 (4,6) |
Гайка болта крепления генератора к кронштейну | М12 х 1,25 | 68,6 (7,0) | 58,3 (5,95) | 72 (7,35) |
Гайка крепления установочной планки к генератору | М10 х 1,25 | 43,12 (4,4) | 28,63 (2,86) | 45,27 (4,6) |
Гайка крепления подушки опоры к кронштейну двигателя | М10 х 1,25 | 33,3 (3,4) | 21,6 (2,2) | 35 (3,57) |
Гайка крепления подушки к поперечине передней подвески | М10 х 1,25 | 32,3 (3,3) | 27,4 (2,8 ) | 34 (3,46) |
Гайка крепления пластины к подушке | М6 | 8,8 (0,90) | 5,7 (0,58 ) | 9,2 (0,94) |
Гайка крепления поперечины задней подвески двигателя | М8 | 17,6 (1,8 ) | 15 (1,53) | 18,6 (1,9) |
Гайка крепления задней опоры к коробке передач | М8 | 27,4 (2,8 ) | 23,3 (2,4) | 28,8 (2,94) |
Гайка болта крепления задней опоры к поперечине | М8 | 24,5 (2,5) | 15,9 (1,62) | 25,7 (2,62) |
Сцепление | ||||
Болт крепления сцепления | М8 | 29,4 (3,0) | 19,1 (1,95) | 30,9 (3,15) |
Гайка болта крепления педалей сцепления и тормоза | М12 х 1,25 | 19,6 (2,0) | 12,7 (1,3) | 20,6 (2,1) |
Гайки крепления главны х цилиндров сцепления и тормозов | М8 | 14,7 (1,5) | 9,8 (1,0) | 15,7 (1,6) |
Гайка трубопровода сцепления | М12 | 29,4 (3,0) | 24,5 (2,5) | 31,4 (3,2) |
Коробка передач | ||||
Выключатель света заднего хода | М14 х 1,5 | 43,1 (4,4) | 28,4 (2,9) | 45,1 (4,6) |
Болты крепления картера сцепления к двигателю | М12 х 1,25 | 83,3 (8,5) | 53,9 (5,5) | 87,2 (8,9) |
Гайка крепления картера сцепления к коробке передач | М10 х 1,25 | 49 (5,0) | 31,8 (3,2) | 51,4 (5,2) |
Гайка крепления картера сцепления к коробке передач | М8 | 24,5 (2,5) | 15,7 (1,6) | 25,5 (2,6) |
Болт крепления крышки фиксаторов штоков | М8 | 24,5 (2,5) | 15,7 (1,6) | 25,5 (2,6) |
Гайка крепления задней крышки | М8 | 24,5 (2,5) | 15,7 (1,6) | 25,5 (2,6) |
Гайка заднего конца вторичного вала | М20 х 1 | 78,4 (8,0) | 66,6 (6,8 ) | 82,3 (8,4) |
Болт зажимной шайбы подшипника промежуточного вала | М12 х 1,25 | 93,1 (9,5) | 79,4 (8,1) | 98 (10) |
Болт крепления вилки к штоку переключения передач | М6 | 17,6 (1,8 ) | 11,7 (1,2) | 18,6 (1,9) |
Карданная передача | ||||
Гайка вилки переднего карданного вала | М16 х 1,5 | 93,1 (9,5) | 79,4 (8,1) | 98 (10) |
Гайки болтов крепления эластичной муфты | М12 х 1,25 | 67,6 (6,9) | 57,8 (5,9) | 71,5 (7,3) |
Гайка болта крепления фланца карданного вала к фланцу редуктора | М8 | 32,3 (3,3) | 27,4 (2,8 ) | 34,3 (3,5) |
Задний мост | ||||
Болт крепления редуктора | М8 х 1,25 | 41,2 (4,2) | 35 (3,6) | 43,2 (4,4) |
Болт крепления крышки подшипника дифференциала | М10 х 1,25 | 51 (5,2) | 43,3 (4,42) | 53,5 (5,46) |
Болт крепления ведомой шестерни | М10 х 1,25 | 98 (10) | 83,3 (8,5) | 102,9 (10,5) |
Гайка крепления фланца к ведущей шестерне | М16 х 1,5 | См. установка и регулировка ведущей шестерни | ||
Гайка экцентрика регулировки колодок заднего тормоза | М10 х 1,25 | 49 (5,0) | 41,6 (4,25) | 51,4 (5,25) |
Рулевое управление | ||||
Гайка болта крепления картера рулевого механизма | М10 х 1,25 | 39,2 (4,0) | 33,3 (3,4) | 41,2 (4,2) |
Гайка болта крепления кронштейна маятникового рычага | М10 х 1,25 | 39,2 (4) | 33,3 (3,4) | 41,2 (4,2) |
Гайка шарового пальца тяг рулевого привода | М13 х 1,5 | 50 (5,1)* | 42,1 (4,3) | 53 (5,4) |
Болт крепления вала рулевого управления к валу червяка | М8 | 24,5 (2,5) | 15,7 (1,6) | 25,5 (2,6) |
Гайка крепления рулевого колеса | М16 х 1,5 | 49 (5) | 31,4 (3,2) | 51 (5,2) |
Гайка крепления кронштейна вала рулевого управления и выключателя зажигания | М8 | 17,6 (1,8 ) | 15 (1,53) | 18,6 (1,9) |
Гайка крепления сошки | М20 х 1,5 | 235,2 (24) | 199,9 (20,4) | 247 (25,2) |
Гайка оси маятникового рычага | М14 х 1,5 | 98 (10) | 63,7 (6,5) | 102,9 (10,5) |
Передняя подвеска | ||||
Болт крепления поперечины к лонжерону кузова | М12 х 1,25 | 93,1 (9,5) | 78,4 (8,0) | 98 (10) |
Гайка нижни х болтов крепления поперечины к лонжерону кузова | М12 х 1,25 | 78,4 (8,0) | 66,6 (6,8 ) | 82,3 (8,4) |
Гайка болта крепления оси нижнего рычага | М12 х 1,25 | 78,4 (8 ) | 66,6 (6,8 ) | 82,3 (8,4) |
Гайка оси нижнего рычага | М14 х 1,5 | 98 (10) | 63,7 (6,5) | 102,9 (10,5) |
Гайка оси верхнего рычага | М14 х 1,5 | 88,2 (9,0) | 57,3 (5,8 ) | 92,1 (9,4) |
Гайка крепления верхнего конца амортизатора | М10 х 1,25 | 32,3 (3,3) | 27,4 (2,8 ) | 34 (3,46) |
Гайка крепления нижнего конца амортизатора | М10 х 1,25 | 58,8 (6,0) | 50 (5,1) | 61,7 (6,3) |
Гайка подшипников ступицы переднего колеса | М18 х 1,5 | См. проверка и регулировка углов установки передних колес | ||
Болт крепления суппорта к кронштейну | М10 х 1,25 | 34,3 (3,5) | 29,1 (2,97) | 36 (3,67) |
Гайка крепления штанги стабилизатора поперечной устойчивости | М8 | 17,6 (1,8 ) | 15 (1,53) | 18,6 (1,9) |
Гайка крепления шаровы х пальцев к поворотному кулаку | М14 х 1,5 | 98 (10) | 83,3 (8,5) | 102,9 (10,5) |
Болт крепления колеса | М12 х 1,25 | 68,6 (7,0) | 58,8 (6,0) | 72, (7,35) |
Гайка болтов крепления поворотного кулака | М10 х 1,25 | 58,8 (6,0) | 50 (5,1) | 61,7 (6,3) |
Задняя подвеска | ||||
Гайки крепления амортизаторов | М12 х 1,25 | 58,8 (6,0) | 38,2 (3,9) | 61,7 (6,3) |
Гайки болтов крепления поперечной и продольных штанг | М12 х 1,25 | 78,4 (8,0) | 66,6 (6,8 ) | 82,3 (8,4) |
Тормоза | ||||
Гайки соединений трубопроводов привода тормозов | М10 | 17,6 (1,8 ) | 14,7 (1,5) | 18,6 (1,9) |
Цитата
Степень и моменты затяжки болтов и гаек автомобиля.
СИСТЕМА ВЫПУСКА ОТРАБОТАВШИХ ГАЗОВНаименование деталей Момент затяжки, Н-м
Гайки крепления выпускного коллектора 22
Болты крепления термозащитного экрана 8
Гайки крепления приемной трубы к выпускному коллектору 45
Наименование деталей Момент затяжки, Н м
Болты крепления задней крышки ремня привода ГРМ 6
Болты крепления верхней и нижней крышек ремня привода ГРМ 3
Болт крепления натяжного устройства ремня привода ГРМ 35
Болты крепления крышки головки блока цилиндров 8
Болты крепления крышек подшипников распределительных валов 8
Болты крепления головки блока цилиндров 25 + 90° + 90° + 90° + 45°
Болт шкива коленчатого вала 95 + 30° + 15°
Болты крепления шкивов распределительных валов 50 + 60° + 15°
Болты крепления маховика 35 + 30° + 15°
Болты крепления кронштейна ресивера к блоку цилиндров 35
Болт крепления кронштейна к ресиверу 20
Болты крепления ресивера к впускному трубопроводу 8
Гайки крепления впускного трубопровода к головке блока цилиндров 22
Гайки крепления выпускного коллектора 22
Болты крепления поддона картера двигателя 10
Пробка сливного отверстия поддона картера двигателя 14
Болты крепления масляного насоса 10
Винты крепления задней крышки масляного насоса 6
Болты крепления маслозаборника 10
Пробка редукционного клапана 50
Болты и гайки опор силового агрегата 55
Тип масла АСЕА АЗ/ВЗ, SAE 5W30 или SAE 0W30 (для эксплуатации при
температурах ниже —25 °С
Объём масла в системе смазки, л:
— 1,4 и 1,6 DOHC 3,5
— 1,8 DOHC 4,25
КОРОБКА АВТОМАТИдентификационные номера (модификации):
— 1,4; 1,6
— 1,8
AF13
AF17
Тип рабочей жидкости ATF Opel 09120 541
Заправочный объём, л 4,0
Наименование деталей Момент затяжки, Нм
Сливная пробка 35
Болты крепления каркаса селектора к кузову 5
Болты крепления корпуса механизма переключения передач 20
Болты крепления коробки передач к блоку цилиндров 60
Болты крепления коробки передач к поддону картера двигателя 40
Болты крепления кронштейна нижней штанги силового агрегата 90
Болты крепления кронштейна левой опоры силового агрегата 48
МЕХАНИЧЕСКАЯ КОРОБКА ПЕРЕДАЧТрансмиссионное масло:
— группа по АР 1
— класс вязкости по SAE
GL-4
80W или 75W
Заправочный объём, л 1,8
Наименование деталей Момент затяжки, Н-м
Выключатель света заднего хода 20
Болты крепления крышки дифференциала 40
Болты крепления каркаса рычага механизма переключения передач 7
Болты крепления корпуса механизма переключения передач 22
Болт стяжного хомута штока привода механизма переключения передач 14
Болты крепления коробки передач к блоку цилиндров 73
Задний болт крепления коробки передач к поддону картера 31
Болты крепления коробки передач к поддону картера (кроме заднего) 21
Болты крепления кронштейна нижней штанги силового агрегата 90
Болты крепления кронштейна левой опоры силового агрегата 48
ПРИВОДЫ ПЕРЕДНИХ КОЛЁССПРАВОЧНЫЕ ДАННЫЕ
ОСНОВНЫЕ ДАННЫЕ ДЛЯ КОНТРОЛЯ, РЕГУЛИРОВКИ И ОБСЛУЖИВАНИЯ
Тип смазки Opel P/N 90094176 или специальная смазка для ШРУСов (Special
Grease for Constant Velocity Joints, российский аналог — ШРУС-4)
Необходимое количество смазки, г: 110-130
наружный шарнир 120-140 (для ШРУСов шарикового типа)
внутренний шарнир 195—215 (для ШРУСов трехшипового типа)
МОМЕНТЫ ЗАТЯЖКИ РЕЗЬБОВЫХ СОЕДИНЕНИЙНаименование деталей Момент затяжки, Н-м
Гайки крепления колеса 110
Гайка подшипника ступицы переднего колеса 120, полностью ослабить, 20, довернуть на 80°
Гайка стяжного болта пальца шаровой опоры 100
СИСТЕМА ОХЛАЖДЕНИЯОСНОВНЫЕ ДАННЫЕ ДЛЯ КОНТРОЛЯ И ОБСЛУЖИВАНИЯТип охлаждающей жидкости На основе этиленгликоля
Объём охлаждающей жидкости 6,3 л; на автомобилях с кондиционером 6,6 л
Температура начала открытия термостата
— двигатели 1,4 и 1,6 DOHC 92 “С
— двигатель 1,8 DOHC 80 °С
Температура полного открытия термостата 107 “С
Температура включения элекгровентидятора системы охлаждения 100 “С
Температура выключения электровентилятора системы охлаждения 95 “С
Наименование деталей Момент затяжки, Нм
Болты крепления насоса охлаждающей жидкости 10
Винты крепления электродвигателя вентилятора 4
Болты крепления кожуха элетровентилятора 4
Болты крепления радиатора 8
Гайки крепления расширительного бачка 5
Болты крепления крышки термостата 20
Топливо (по ГОСТ 51105-97) Бензин с октановым числом 91 и выше
Ёмкость топливного бака, л 52
Рабочее давление топлива в топливной рампе, кПа: 300-380
Сопротивление обмотки топливной форсунки при температуре 20 °С, Ом 15,5-16,5
Тип свечей зажигания (изготовитель) BKR6E-11 (NGK)
Резьба свечи зажигания М 14×1,25
Зазор между электродами свечи зажигания, мм 1,0-1, !
Сопротивление высоковольтных проводов зажигания не более, кОм 3
МОМЕНТЫ ЗАТЯЖКИ РЕЗЬБОВЫХ СОЕДИНЕНИЙ ДВИГАТЕЛЯ
Наименование деталей Момент затяжки, Н м
Болты датчика положения распределительного вала 7
Болт датчика положения коленчатого вала 6,5
Болты крепления модуля зажигания 10
Болты клапана рециркуляции отработавших газов 30
Болты крепления ЭБУ 12
Датчик температуры охлаждающей жидкости 17,5
Винт фланца адсорбера системы улавливания паров топлива 4
Винт крепежного кронштейна топливного фильтра 4
Болты крепления топливного бака 20
Болты крепления топливной рампы 25
Болт крепления датчика детонации 20
Винты крепления датчика абсолютного давления 8
Датчики кислорода 42
Свечи зажигания 25
Гайки и болты крепления дроссельного узла 1
Допустимое биение накладок ведомого диска не более, мм 0,5
Минимальное расстояние между рабочей поверхностью накладок ведомого диска
и заклепками их крепления, мм 0,3
МОМЕНТЫ ЗАТЯЖКИ РЕЗЬБОВЫХ СОЕДИНЕНИЙ
Наименование деталей Момент затяжки, Нм
Гайки крепления главного цилиндра выключения сцепления 20
Болты крепления рабочего цилиндра выключения сцепления 5
Болты крепления нажимного диска к маховику 15
Таблица усилий затяжки дюймовых болтов
(Нажмите на изображение чтобы увеличить)
Таблица усилий затяжки метрических болтов
(Нажмите на изображение чтобы увеличить)
ГОСТ Р 50271-92 Гайки шестигранные стальные самостопорящиеся. Механические и эксплуатационные свойства
ГОСУДАРСТВЕННЫЙ СТАНДАРТ РОССИЙСКОЙ ФЕДЕРАЦИИ
ГАЙКИ ШЕСТИГРАННЫЕ СТАЛЬНЫЕ САМОСТОПОРЯЩИЕСЯ |
ГОСТ P |
Механические и эксплуатационные свойства |
|
Prevailing torque type steel hexagon nuts. Mechanical and performance properties |
Дата введения 1994-01-01
Предисловие
1 ПОДГОТОВЛЕН И ВНЕСЕН Техническим комитетом по стандартизации ТК 229 «Крепежные изделия»
2 УТВЕРЖДЕН И ВВЕДЕН В ДЕЙСТВИЕ Постановлением Госстандарта России от 16 сентября 1992 г. № 1184
Настоящий стандарт подготовлен методом прямого применения международного стандарта ИСО 2320-83 «Гайки шестигранные стальные с преобладающим крутящим моментом. Механические и эксплуатационные свойства» с дополнительными требованиями, отражающими потребности народного хозяйства
3 ВВЕДЕН ВПЕРВЫЕ
4 ПЕРЕИЗДАНИЕ
Содержание
1 Общие сведения и область применения 2 Определения 3 Обозначения 4 Механические и эксплуатационные свойства 5 Методы испытаний 6 Маркировка ПРИЛОЖЕНИЕ 1 (рекомендуемое) РЕКОМЕНДУЕМАЯ ТЕХНОЛОГИЯ ПРОВЕДЕНИЯ ИСПЫТАНИЙ С ИСПОЛЬЗОВАНИЕМ ДИНАМОМЕТРИЧЕСКИХ КЛЮЧЕЙ ДЛЯ ОПРЕДЕЛЕНИЯ ВЕЛИЧИН КРУТЯЩИХ МОМЕНТОВ ЗАТЯЖКИ СТАЛЬНЫХ ШЕСТИГРАННЫХ ГАЕК С ПРЕОБЛАДАЮЩИМ КРУТЯЩИМ МОМЕНТОМ ПРИЛОЖЕНИЕ 2 (рекомендуемое) Дополнительные требования, отражающие потребности народного хозяйства ИНФОРМАЦИОННЫЕ ДАННЫЕ |
1.1 Настоящий стандарт устанавливает требования к механическим и эксплуатационным свойствам шестигранных стальных самостопорящихся гаек и шестигранных стальных самостопорящихся гаек с фланцем, (далее – гайки):
– с резьбой от М3 до М39 включительно;
– с требованиями к прочностным характеристикам, указанным в таблице 1;
Таблица 1
Механические свойства
Размер резьбы d , мм |
Класс прочности |
|||||||||||||||
5 |
8 |
9 |
||||||||||||||
Напряжение от пробной нагрузки σ f , Н/мм2 |
Твердость по Виккерсу HV |
Твердость по Роквеллу HRC э |
Напряжение от пробной нагрузки σ f , Н/мм2 |
Твердость по Виккерсу HV |
Твердость по Роквеллу HRC э |
Напряжение от пробной нагрузки σ f , Н/мм2 |
Твердость по Виккерсу HV |
Твердость по Роквеллу HRC э |
||||||||
от |
до |
не менее |
не более |
не менее |
не более |
не менее |
не более |
не менее |
не более |
не менее |
не более |
не менее |
не более |
|||
– |
4 |
520 |
130 |
302 |
– |
30 |
800 |
170 |
302 |
– |
30 |
900 |
170 |
302 |
– |
30 |
4 |
7 |
580 |
810 |
183 |
– |
915 |
188 |
– |
||||||||
7 |
10 |
590 |
830 |
940 |
||||||||||||
10 |
16 |
610 |
840 |
950 |
||||||||||||
16 |
39 |
630 |
146 |
– |
920 |
233 |
353 |
– |
36 |
920 |
Продолжение таблицы 1
Размер резьбы d , мм |
Класс прочности |
||||||||||
10 |
12 |
||||||||||
Напряжение от пробной нагрузки σ f , Н/мм2 |
Твердость по Виккерсу HV |
Твердость по Роквеллу HRC э |
Напряжение от пробной нагрузки σ f , Н/мм2 |
Твердость по Виккерсу HV |
Твердость по Роквеллу HRC э |
||||||
от |
до |
не менее |
не более |
не менее |
не более |
не менее |
не более |
не менее |
не более |
||
– |
4 |
1040 |
272 |
353 |
28 |
36 |
1150 |
295 |
353 |
29 |
36 |
4 |
7 |
1040 |
1150 |
||||||||
7 |
10 |
1040 |
1160 |
||||||||
10 |
16 |
1050 |
1190 |
||||||||
16 |
39 |
1060 |
1200 |
– |
– |
– |
– |
Примечание – Минимальная твердость обязательна для гаек, которые не могут быть испытаны на пробную нагрузку, или для гаек термически обработанных. Для всех других гаек величина минимальной твердости дана для справок.
– с размерами в соответствии со стандартами на изделия;
– для следующих диапазонов температур:
1) от минус 50 °С до плюс 300 °С для цельнометаллических гаек, не имеющих гальванопокрытия;
2) от минус 50 °С до плюс 230 °С для цельнометаллических гаек с гальванопокрытием;
3) от минус 50 °С до плюс 120 °С для гаек с неметаллическими вставками.
Требования настоящего стандарта являются обязательными.
Стандарт не распространяется на гайки, обладающие особыми свойствами, удовлетворяемыми за счет применения специальных материалов и покрытий, которые способствуют улучшению таких характеристик, как:
– свариваемость;
– коррозионная стойкость;
– способность противостоять температурам сверх диапазонов, указанных выше.
1.2 Для гаек с мелким шагом установлены требования только по преобладающим крутящим моментам.
1.3 Дополнительные требования, отражающие потребности народного хозяйства, приведены в приложении 2.
2.1 Самостопорящимися гайками называются гайки, обеспечивающие стопорение в резьбовом соединении за счет дополнительных сил трения, возникающих между деформированными участками резьбы гайки или неметаллической вставки гайки и резьбой стержневой детали.
Стопорение гаек характеризуется способностью сохранять преобладающие крутящие моменты при повторных завертываниях и отвертываниях.
2.2 Преобладающие крутящие моменты – это крутящие моменты завертывания гайки на болт до приложения момента затяжки или отвертывания после снятия усилия затяжки.
Величина преобладающего крутящего момента измеряется во время вращения гайки.
2.3 Гайки типа NF с нормальным трением
Гайки данного типа должны иметь цинковое покрытие с хроматированием или фосфатированием, с дополнительной смазкой или без нее, чтобы отвечать предъявляемым требованиям к усилиям затяжки.
2.4 Гайки типа LF с пониженным трением
Гайки данного типа должны иметь кадмиевое покрытие с дополнительной смазкой или фосфатное покрытие с антикоррозионной смазкой, чтобы отвечать предъявляемым требованиям к усилиям затяжки.
Примечание – Рекомендуется ограничить использование гаек с пониженным трением ( LF ), имеющих кадмиевое гальванопокрытие.
Гайки с нормальной высотой равной или более 0,8 d (эффективная высота резьбы равна или более 0,6 d ) обозначаются цифрой, указывающей наибольший класс прочности болтов, с которыми они могут сопрягаться в соединении.
Болт или винт определенного класса прочности, сопряженный с гайкой эквивалентного класса прочности в соответствии с таблицей 2 обеспечит получение резьбового соединения, способного подвергаться затяжке до величины напряжения болта, равной минимальной величине пробной нагрузки, либо нагрузке предела текучести болта без срыва резьбы.
Таблица 2
Класс прочности гайки |
5 |
8* |
9* |
10* |
12 |
Класс прочности сопрягаемого болта или винта |
5.8 и ниже |
8.8 и ниже |
9.8, 8.8 и ниже |
10.9 9.8 8.8 |
12.9 10.9 |
* Не рекомендуется термически обработанные цельнометаллические гайки применять с болтами класса прочности ниже 8.8. |
Если соединение будет затянуто выше пробной нагрузки болта, то конструкция гайки должна быть рассчитана так, чтобы в результате перезатяжки обеспечить по крайней мере 10 % разрушений по стержню болта для предупреждения потребителя о неправильном монтаже резьбовых соединений.
При частом срыве резьбы необходимо применять гайки более высокого класса прочности.
4.1 Материалы и технологические требования
4.1.1 Материалы
Гайки должны изготавливаться из сталей, химический состав которых указан в таблице 3. Вставки гаек, создающие преобладающие крутящие моменты, должны изготавливаться из материала, отличного отстали.
4.1.2 Термическая обработка
Гайки класса прочности 5 термической обработке не подлежат. Гайки классов прочности 8 и 9 могут подвергаться термообработке.
Таблица 3
Класс прочности |
Химический состав, % |
|||
С , не более |
Мп, не менее |
P , не более |
S , не более |
|
51) |
0,500 |
– |
0,110 |
0,150 |
8 и 9 |
0,580 |
0,250 |
0,060 |
0,1503) |
102) |
0,580 |
0,300 |
0,048 |
0,0583) |
122) |
0,580 |
0,450 |
0,048 |
0,058 |
1) Допускается изготавливать гайки из автоматной стали, за исключением случаев, оговоренных между потребителем и изготовителем. В таких случаях допустимы максимальные содержания серы, фосфора, свинца: S – 0,34 %, P – 0,12 %, Рв – 0,35 %. 2) Для улучшения механических свойств гаек в состав металла могут добавлять различные легирующие элементы. 3) По соглашению с потребителем для гаек, изготовленных точением, допускается максимальное содержание серы 0,24 %. |
Гайки классов прочности 10 и 12 должны подвергаться термической обработке. Цементация гаек любого класса прочности не допускается.
4.1.3 Покрытие
По требованию потребителя гайки могут изготавливаться с защитным покрытием или без покрытия.
При необходимости гайки должны быть смазаны, чтобы отвечать предъявляемым требованиям по уменьшению трения. Смазка должна быть нетоксичной и не иметь неприятного запаха во время сборки. Смазка должна соответствовать требованиям высокоскоростной сборки.
Эксплуатационные свойства гаек, имеющих защитное покрытие и смазку, не должны ухудшаться после шести месяцев хранения в закрытом помещении. При хранении должна поддерживаться температура от минус 5 °С до плюс 40 °С.
Если очистка гаек от смазки или от защитного покрытия проведена потребителем, то изготовитель не несет ответственности за несоответствие гаек установленным размерам, механическим и эксплуатационным свойствам.
4.1.4 Водородная хрупкость
Гайки не должны разрушаться из-за водородной хрупкости. Если на гайки, прошедшие термическую обработку, наносится цинковое или фосфатное покрытие, то необходимо применять соответствующие технологические процессы, чтобы избежать водородной хрупкости. Гайки после нанесения покрытия гальваническим или другим способом, должны как можно скорее подвергаться обработке, чтобы снять водородную хрупкость.
4.2 Механические свойства
4.2.1 Пробная нагрузка
Гайки должны выдерживать пробную нагрузку, указанную в таблице 4, для соответствующего класса прочности при проведении испытаний, указанных в 5.1 настоящего стандарта.
Таблица 4
Пробные нагрузки, усилия затяжки и преобладающие крутящие моменты для гаек
Гайка |
Пробная нагрузка, кН |
Усилие затяжки, кН |
Преобладающий крутящий момент, Н·м* |
||||||||||||||
Резьба d |
Шаг резьбы P , мм |
Класс прочности |
Класс прочности |
Класс прочности 5, 8, 9 |
Класс прочности 10, 12 |
||||||||||||
5 |
8 |
9 |
10 |
12 |
5 |
8 |
9 |
10 |
12 |
1-е завертывание, не более |
1-е отвертывание, не менее |
5-е отвертывание, не менее |
1-е завертывание, не более |
1-е отвертывание, не менее |
5-е отвертывание, не менее |
||
М3 |
0,5 |
2,97 |
4 |
– |
5,2 |
5,8 |
1,43 |
2,19 |
– |
3,13 |
3,66 |
0,43 |
0,12 |
0,08 |
0,6 |
0,15 |
0,10 |
М4 |
0,7 |
5,18 |
7 |
– |
9,15 |
10,1 |
2,50 |
3,82 |
– |
5,47 |
6,39 |
0,90 |
0,18 |
0,12 |
1,2 |
0,22 |
0,15 |
М5 |
0,8 |
8,34 |
11,5 |
12,8 |
14,8 |
16,3 |
4,05 |
6,17 |
6,92 |
8,85 |
10,4 |
1,6 |
0,29 |
0,20 |
2,1 |
0,35 |
0,24 |
М6 |
1,0 |
11,9 |
16,3 |
18,1 |
20,9 |
23,7 |
5,73 |
8,70 |
9,82 |
12,5 |
14,6 |
3,0 |
0,45 |
0.30 |
4,0 |
0,55 |
0,40 |
М8 |
1,25 |
21,6 |
30,4 |
34,4 |
38,1 |
42,5 |
10,4 |
15,9 |
17,8 |
22,8 |
26,6 |
6,0 |
0,85 |
0,60 |
8,0 |
1,15 |
0,80 |
М10 |
1,5 |
34,2 |
48,1 |
54,5 |
60,3 |
67,3 |
16,5 |
25,3 |
28,3 |
36,1 |
42,2 |
10,5 |
1,5 |
1,0 |
14,0 |
2,0 |
1,4 |
М12 |
1,75 |
49,7 |
70,8 |
80,1 |
88,5 |
100 |
24,0 |
36,7 |
41,1 |
52,5 |
61,4 |
15,5 |
2,3 |
1,6 |
21 |
3,1 |
2,1 |
М14 |
2,0 |
67,8 |
96 |
109 |
121 |
137 |
32,8 |
50,0 |
56,1 |
71,6 |
84 |
24 |
3,3 |
2,3 |
31 |
4,4 |
3,0 |
М16 |
2,0 |
92,6 |
132 |
149 |
165 |
187 |
44,8 |
68,2 |
76,5 |
97,5 |
114 |
32 |
4,5 |
3,0 |
42 |
6,0 |
4,2 |
М18 |
2,5 |
113 |
177 |
– |
204 |
230 |
54,8 |
86,2 |
– |
119 |
140 |
42 |
6,0 |
4,2 |
56 |
8,0 |
5,5 |
М20 |
2,5 |
145 |
225 |
– |
260 |
294 |
69,8 |
110 |
– |
152 |
178 |
54 |
7,5 |
5,3 |
72 |
10,5 |
7,0 |
М22 |
2,5 |
179 |
279 |
– |
321 |
364 |
86,2 |
136 |
– |
189 |
220 |
68 |
9,5 |
6,5 |
90 |
13 |
9,0 |
М24 |
3,0 |
208 |
325 |
– |
374 |
424 |
100,5 |
159 |
– |
220 |
256 |
80 |
11,5 |
8,0 |
100 |
15 |
10,5 |
М27 |
3,0 |
271 |
422 |
– |
487 |
561 |
77,2 |
206 |
– |
286 |
334 |
94 |
13,5 |
10,0 |
123 |
17 |
12 |
М30 |
3,5 |
331 |
516 |
– |
595 |
673 |
94,5 |
253 |
– |
350 |
408 |
108 |
16 |
13 |
140 |
19 |
14 |
М33 |
3,5 |
409 |
638 |
– |
736 |
832 |
117 |
312 |
– |
432 |
505 |
122 |
18 |
14 |
160 |
21,5 |
15,5 |
М36 |
4,0 |
482 |
752 |
– |
866 |
980 |
138 |
368 |
– |
509 |
594 |
136 |
21 |
16 |
180 |
24 |
17,5 |
М39 |
4,0 |
576 |
898 |
– |
1035 |
1171 |
165 |
440 |
– |
608 |
710 |
150 |
23 |
18 |
200 |
26,5 |
19,5 |
* Преобладающий крутящий момент можно применять и для шага резьбы в соответствии с таблицей 8 ГОСТ 1759.4. Примечание – Усилие затяжки гаек класса прочности 5 равно 75 % пробной нагрузки болтов класса прочности 5.8 для размеров от М3 до М24 и 75 % для болтов класса прочности 4.6 для размеров больше М24. Усилие затяжек гаек классов прочности 8, 9 и 10 % равны 75 % пробной нагрузки болтов класса прочности 8.8, 9.8 и 10.9 соответственно. Пробные нагрузки болтов даны в ГОСТ 1759.4. |
4.2.2 Твердость
При проведении испытаний в соответствии с 5.2, гайки должны иметь твердость, соответствующую классам прочности, указанным в таблице 1 .
4.3 Эксплуатационные свойства
Преобладающий крутящий момент
Величины преобладающего крутящего момента, создаваемого гайками (см. 2.2) при первом и последующих завертываниях, не должны превышать максимальной величины преобладающего крутящего момента первого завертывания, указанного для соответствующих классов прочности по таблице 4 при проведении испытаний в соответствии с 5.3 настоящего стандарта.
Величины преобладающего крутящего момента гаек во время первого и пятого отвертывания не должны быть меньше величин преобладающего крутящего момента отвертывания, указанных в таблице 4 , при проведении испытаний в соответствии с 5.3 настоящего стандарта.
5.1 Испытание на пробную нагрузку
Испытуемая гайка должна быть навернута на испытательный болт ( 5.1.1) или закаленную оправку ( 5.1.2) так, чтобы над поверхностью гайки выступало не менее трех витков резьбы болта или оправки.
При арбитражных испытаниях для гаек с неметаллическими вставками используется закаленная оправка, для цельнометаллических гаек – болт.
Максимальный преобладающий крутящий момент при завертывании гайки на испытательный болт или оправку должен быть зафиксирован, как только первый полный виток резьбы пройдет элемент конструкции, создающий преобладающий крутящий момент.
Величина пробной нагрузки в соответствии с таблицей 4 должна быть приложена в течение 15 с в осевом направлении болта или закаленной оправки на опорную поверхность гайки. Гайка должна выдерживать нагрузку без срыва или смятия резьбы.
При проведении арбитражных испытаний проверка на осевое растяжение является решающей.
Максимальный преобладающий крутящий момент, зафиксированный после отвертывания гайки на половину полного оборота и далее до полного отвертывания, не должен превышать максимального преобладающего крутящего момента, зафиксированного во время завертывания гайки на болт или оправку.
5.1.1 Болт, используемый в испытаниях на пробную нагрузку
Болт должен соответствовать требованиям, изложенным в 5.3.5.
Испытательный болт должен выдерживать большую величину пробной нагрузки чем гайка, которая подвергается проверке.
5.1.2 Закаленная оправка, используемая в испытаниях на пробную нагрузку
После допуска резьбы оправки 5 h 6 g за исключением допуска наружного диаметра, который должен составлять 1/4 поля допуска 6 g в его нижней части.
Твердость испытательной оправки должна быть 450 … 510 HV (47 . . . 52 HRC э ).
5.2 Испытание на твердость
При контроле гаек испытание твердости проводится на одной из опорных поверхностей гайки в трех точках, смещенных относительно друг друга на 120°, а значения твердости определяется как среднеарифметическое трех измерений.
В спорных случаях твердость проверяется на продольном сечении, проходящем через ось гайки, в точках, расположенных как можно ближе к наружному диаметру резьбы гайки.
Испытание твердости по Виккерсу является решающим, прилагаемая нагрузка должна составлять 30 HV .
Испытание твердости по Виккерсу, Бринеллю, Роквеллу – по ГОСТ 2999, ГОСТ 9012, ГОСТ 9013 соответственно.
5.3 Испытание преобладающего крутящего момента
Настоящий стандарт предусматривает две программы испытаний: программу А и программу В.
Программа А предназначается для обычной приемки партии гаек с преобладающим крутящим моментом по мере их производства изготовителем и при входном контроле потребителем.
Программа В является продолжением программы А и включает в себя четыре дополнительных завертывания и отвертывания гаек без приложения осевой нагрузки. При пятом отвертывании необходимо зарегистрировать величину преобладающего крутящего момента, как это выполнялось при первом отвертывании гайки в программе А.
Обычно считается, что изделия, отвечающие требованиям программы В выдержали испытание, проведенное по программе А.
5.3.1 Программа А
Программа А предназначена для проведения обычной приемочной проверки партии изделий.
Испытание на величину преобладающего крутящего момента должно производиться при комнатной температуре с использованием устройства для измерения нагрузки ( 5.3.4).
Испытательный болт ( 5.3.5) вставляется в устройство для измерения нагрузки, затем на болт устанавливается шайба ( 5.3.6) и испытываемая гайка. Гайка должна завертываться на болт до тех пор, пока минимум два полных витка резьбы болта не выступят над поверхностью гайки. Завертывание гайки проводится либо вручную с использованием гаечного ключа с регулируемым крутящим моментом (данный рекомендованный способ изложен в приложении 1), либо с использованием специального приспособления, замеряющего крутящий момент ( 5.3.3) (подобное устройство описывается в приложении 2).
Максимальный преобладающий крутящий момент, достигнутый при завертывании гайки на последующие 360°, должен быть зафиксирован. Для гайки, в соответствии с предъявляемыми требованиями, данный максимальный преобладающий крутящий момент не должен превышать величину преобладающего крутящего момента первого завертывания, указанного в таблице 4 для соответствующей гайки.
Завертывание гайки должно проводиться до тех пор, пока она не коснется опорной поверхностью закаленной шайбы. Длина испытательного болта должна быть такой, чтобы при касании гайки с шайбой над ее поверхностью выступало от 4 до 7 витков резьбы болта. Гайка завертывается до тех пор пока в болте не образуется максимальное осевое усилие, равное усилию затяжки, указанному в таблице 4 . При затягивании гайки необходимо предупредить проворачивание шайбы. Гайка отвертывается до тех пор, пока усилие затяжки не уменьшится до нуля. Максимальная величина преобладающего крутящего момента в процессе отвертывания гайки на последующий полный оборот резьбы должна быть измерена. Для гайки, отвечающей предъявляемым требованиям, эта величина преобладающего крутящего момента не должна быть меньше величины преобладающего крутящего момента первого отвертывания гайки, указанной в таблице 4 .
5.3.2 Программа В
Программа В используется при оценке стопорящих свойств гаек, а также при арбитражной проверке.
Испытания по программе А должны быть проведены. После того как измерена величина преобладающего крутящего момента первого отвертывания, гайка отвертывается до тех пор, пока элемент резьбы, создающий преобладающий крутящий момент не выйдет из зацепления с наружной резьбой болта. Затем гайка еще четыре раза завертывается и отвертывается. При каждом завертывании над поверхностью гайки должно выступать от 4 до 7 витков резьбы болта. При каждом отвертывании гайки элемент, создающий преобладающий крутящий момент, выводится из соединения с резьбой болта. Измерение преобладающего крутящего момента при этом не обязательно.
Величина преобладающего крутящего момента во время пятого отвертывания гайки на первый полный оборот должна быть измерена. Для гайки, отвечающей предъявляемым требованиям, данная величина преобладающего крутящего момента не должна быть меньше величины преобладающего крутящего момента пятого отвертывания, указанной в таблице 4 . Кроме того, при четырех дополнительных завертываниях и отвертываниях гайки, величина преобладающего крутящего момента не должна превышать максимальной величины преобладающего крутящего момента первого завертывания гайки, указанной в таблице 4 . Между циклами приложения крутящих моментов должны быть установлены значительные промежутки времени с тем, чтобы предотвратить перегрев проверяемого комплекта гайка – болт.
Скорость завертывания и отвертывания гайки должна быть постоянной и равномерной и не должна превышать 30 оборотов в минуту.
5.3.3 Средство для измерения крутящего момента
Средство для измерения крутящего момента затяжки (гаечный ключ с регулируемым крутящим моментом или иной механизированный инструмент) должно обладать точностью измерения в пределах ±2 % максимальной величины крутящего момента.
При арбитражных проверках гайки считаются годными, если показания измерительного прибора находятся в верхней половине допуска крутящих моментов.
5.3.4 Устройство для измерения усилия затяжки
Устройство для измерения усилия затяжки должно обеспечивать измерение величин действительного усилия, которое возникает в болте по мере затягивания гайки. Точность измерения ±5 % от усилия затяжки. Отверстие для болта в опорной плите должно иметь тот же диаметр и допуски, что и шайба, которая используется в испытании.
5.3.5 Болт, используемый для проверки преобладающего крутящего момента
Резьба болтов до М24 должна быть выполнена накаткой. Длина болта должна быть такой, что когда гайка коснется шайбы, над поверхностью гайки выступало от четырех до семи витков резьбы болта. Длина резьбы должна быть такой, чтобы после затяжки гайки минимум два полных витка резьбы находились в зацеплении. Болт должен иметь плоский конец с фаской.
На поверхности резьбы не допускаются заусенцы и другие дефекты, которые могут повлиять на точное определение величины преобладающего крутящего момента.
Болт должен иметь временное сопротивление, соответствующее механическим свойствам болта по ГОСТ 1759.4 .
При испытаниях каждой гайки должен использоваться новый болт.
5.3.5.1 При испытаниях гаек типа NF с нормальным трением болт должен иметь то же покрытие, что и гайка. Допуски на резьбу болта выбираются в зависимости от типа применяемого покрытия, определенного стандартом. При испытаниях гаек с покрытием, отличающимся от цинкового, кадмиевого или фосфатного, необходимо использовать болт с цинково-фосфатным покрытием и смазкой.
5.3.5.2 При испытаниях гаек типа LF с пониженным трением болт должен иметь цинково-фосфатное покрытие со смазкой и резьбу с полем допуска 6 g по ГОСТ 16093.
5.3.6 Шайба, используемая при испытаниях
Если испытания проводятся в соответствии с требованиями настоящего стандарта, то к шайбе не предъявляются специальные требования.
Для проведения испытаний на определение крутящего момента затяжки, качественные характеристики испытательной шайбы согласовываются между потребителем и изготовителем.
Гайки с размером М5 и более должны иметь четкую и ясную маркировку класса прочности и завода изготовителя. Символ класса прочности должен быть выполнен в соответствии с ГОСТ 1759.0. Символ завода-изготовителя выбирается изготовителем.
Маркировка по выбору изготовителя может быть выпуклой или вдавленной. Выпуклая маркировка не должна выходить за максимальные величины ширины и высоты гайки.
Вдавленная маркировка может располагаться на любой поверхности гайки, но желательно не на опорной.
Выпуклая маркировка на опорной поверхности не допускается.
1 Общие сведения и область применения
В данном приложении дается описание рекомендуемого метода измерения величин крутящего момента и эксплуатационных характеристик гаек с преобладающим крутящим моментом с использованием динамометрических ключей и других приспособлений с малой скоростью вращения. Данный способ предназначен для оценки качества изделий, а также для арбитражных испытаний.
2 Устройство
2.1 Ручные динамометрические ключи (один или два для проверки преобладающего крутящего момента и один – для проверки крутящего момента затяжки, при необходимости) для всего диапазона измеряемых величин. (Наличие механизированного инструмента, имеющего скорость завертывания менее 30 оборотов в минуту, и приспособления для измерения крутящего момента, является обязательным).
2.2 Зажимное приспособление для установки испытательных болта, гайки и испытательной шайбы и для измерения растяжения болта, обусловленного усилием затяжки гайки (наиболее желательно использовать электрические тензодатчики, но можно применять и гидравлические датчики). Один из вариантов приспособления показан на рисунке.
Зажимное приспособление, используемое при испытаниях
Устройство для измерения усилия затяжки
1 – испытательный болт, 2 – испытательное приспособление, 3 - испытательная шайба, 4 - испытательная гайка, P – шаг резьбы
* Провертывание шайбы не допускается
3 Метод испытания
Метод испытания на определение характеристик преобладающего крутящего момента изложен в 5.3.
Допускается изготавливать:
1 Гайки класса прочности 6 с механическими свойствами по таблице 5 с преобладающими крутящими моментами (таблица 4), как для гаек классов прочности 5, 8, 9.
Таблица 5
Размер резьбы d , мм |
Напряжение от пробной нагрузки σ F , Н/мм2 |
Твердость по Виккерсу HV |
Твердость по Роквеллу HRC э |
|||
от |
до |
не менее |
не более |
не менее |
не более |
|
– |
4 |
600 |
150 |
302 |
– |
30 |
4 |
7 |
670 |
||||
7 |
10 |
680 |
||||
10 |
16 |
700 |
||||
16 |
39 |
720 |
170 |
– |
2 Гайки М8 – М39 с мелким шагом классов прочности 5, 6, 8, 9, 10, 12 с преобладающими крутящими моментами (таблица 4 ).
Пробная нагрузка гаек – по ГОСТ 1759.5.
Усилие затяжки, равное 75 % от пробной нагрузки болтов соответствующих классов прочности – по ГОСТ 1759.4.
3 Гайки класса прочности 6 должны применяться с болтами класса прочности 6.8.
4 Гайки класса прочности 6 должны изготавливаться из стали со следующим химическим составом: С, не более – 0,5 %, Р, не более – 0,11 %, S, не более – 0,15 %, Mn – отсутствует.
5 Неметаллические вставки должны изготавливаться из материалов, обеспечивающих стопорящие свойства гаек при температурах, указанных в п. 1.1 настоящего стандарта.
Вставка должна быть зафиксирована в корпусе гайки от проворота.
6 Гайки класса прочности 6 термической обработке не подлежат.
7 Покрытие гаек с неметаллической вставкой производить до завальцовки вставки.
8 На цельнометаллические гайки после покрытия должна быть нанесена смазка СРТ (смазка резьбовая твердая). Смазка нетоксична, не пожароопасна, не агрессивна по отношению к стали и покрытию. Допускаются другие типы смазок, обеспечивающие стопорящие свойства гаек.
При сборочных работах смазка удалению не подлежит.
9 Твердость гаек класса прочности 6 не контролировать при условии обеспечения ее технологическим процессом.
ССЫЛОЧНЫЕ НОРМАТИВНО-ТЕХНИЧЕСКИЕ ДОКУМЕНТЫ
Обозначение НТД, на который дана ссылка |
Номер пункта, раздела, приложения |
ГОСТ 1759.0 -87 |
Разд. 6 |
ГОСТ 1759.4-87 |
4.3; 5.3.5 ; |
Приложение 2 |
|
ГОСТ 1759.5-87 |
Приложение 2 |
ГОСТ 2999 -75 |
5.2 |
ГОСТ 9012 -59 |
5.2 |
ГОСТ 9013 -59 |
5.2 |
ГОСТ 16093 -2004 |
5.3.5.2 |
Затяжка резьбового соединения
Погрешности, возникающие при затяжке резьбового соединения
Резьбовые соединения занимают особое место в конструкциях и технологии производства машин. На их долю приходится до 80% общего количества применяемых соединений, трудозатраты на сборку резьбовых соединений составляют до 10% от общей трудоемкости изготовления изделия. Из-за некачественной сборки резьбовых соединений в эксплуатации до 10% рабочего времени тракторного агрегата и до 40% времени техобслуживания автомобиля может затрачиваться на проверку и подтяжку крепежа.
Качество сборки резьбовых соединений зависит от правильной затяжки болтов и гаек, точности изготовления резьбы, чистоты и перпендикулярности торца болта или гайки и бобышки под них, определяющих величину трения на поверхности соединяемых деталей.
Правильная последовательность закрепления винтов или гаек на шпильках основывается на принципе сокращения упругих деформаций сопрягаемых деталей в направлении от середины к краям или, другими словами, на принципе т.н. “располовинивания” погрешностей. Для этого вначале необходимо закрепить винты или гайки, расположенные на пересечении осей симметрии сопрягаемых поверхностей деталей, затем, в направлении осей симметрии (крест-накрест), переходить постепенно к винтам, расположенным на наиболее удаленных расстояниях.
При монтаже тонкостенных деталей они часто деформируются, что приводит к искажению геометрической формы, особенно в тех случаях, когда соединение осуществляется с натягом. В таких соединениях охватываемая деталь имеет больший наружный размер, чем размер отверстия в охватывающей детали, в результате в материалах соединенных деталей возникают напряжения и силы трения, препятствующие их сдвигу. Вследствие натяга на поверхностях контакта возникают давления, определяющие характер деформирования охватываемой и охватывающей деталей.
Существует несколько способов затяжки резьбовых соединений:
- затяжка до определённого момента,
- затяжка до определённого угла,
- затяжка до предела упругости,
- затяжка в области пластических деформаций и другие.
Основным показателем качества сборки резьбовых соединений является точность контроля усилия затяжки, которая определяет равномерность и стабильность затяжки групповых соединений, являющихся основными в автотракторостроении. Усилие затяжки создает определенное контактное напряжение на стыке соединяемых деталей, которое должно обеспечить необходимую плотность и герметичность стыка при действии внешней нагрузки на соединение, возникающее в процессе работы узла. Равномерность усилия затяжки обеспечивается в процессе сборки. Неточная и, как следствие, неравномерная затяжка может являться причиной повышенной вибрации деталей узлов, самоотвинчивания гаек и деформации стянутых деталей.
Наиболее производительным и простым методом контроля усилия затяжки в условиях автоматизированной сборки является контроль крутящего момента на ключе резьбозавертывающего инструмента.
Однако следует отметить, что величина усилия затяжки при контроле этим методом зависит от точности и правильности выбора коэффициентов трения в резьбе и на опорной поверхности гайки (головки винта), а также необходимо учитывать, что величины этих коэффициентов зависят от таких факторов, как скорость затяжки, шероховатость поверхностей крепежных и соединяемых деталей, точности их изготовления, видов и материалов применяемых покрытий и смазок, самого усилия затяжки, метода и времени измерения крутящего момента, так как его величины различны при измерении в процессе затяжки и после ее окончания.
Для обеспечения механизированной сборки необходимого качества изделий с групповыми резьбовыми соединениями необходимо выполнение следующих требований, возникших из практики сборки изделий:
- погрешности осевых сил затяжки резьбовых соединений не должны превышать 6% от номинальных значений;
- синхронная затяжка соединений должна начинаться одновременно.
При механизированной сборке используют одношпиндельные завинчивающие устройства, которые различаются по принципу действия, конструктивно, а главное, – по точности обеспечения осевых сил затяжки, погрешности которых могут колебаться в пределах 30…70% от требуемого значения.
Применение в производстве этих гайковёртов показало, что они эффективны только при жёстком скреплении узлов и деталей там, где не требуется обеспечивать высокую точность осевых сил затяжки, герметичности стыков и одновременного плотного прижатия скрепляемых узлов и деталей.
На практике качественную сборку изделий с групповыми резьбовыми соединениями обеспечивают за счёт высокой квалификации сборщика, который осуществляет затяжку при помощи моментного ключа путём неоднократной затяжки и ослабления соединений.
Многошпиндельные гайковерты, которые работают от одного привода, или такие, у которых каждый шпиндель имеет автономный привод, имеют погрешность осевых сил затяжки до 20% от требуемого значения. Они также не обеспечивают качественную, с учётом герметичности стыков, сборку групповых соединений в связи с неодинаковой продолжительностью завинчивания резьбовых деталей до момента начала затяжки из-за неодинаковой глубины ручного наживления и разной длины нарезанной резьбы, исключая синхронность затяжки.
Существуют различные конструкции многошпиндельных завинчивающих устройств, применяющихся в промышленности для закрепления резьбовых соединений. Они подразделяются на:
- устройства с упругими накопителями энергии (накопители момента),
- устройства с активными обратными связями;
- устройства на основе муфт предельного момента
В устройствах с накопителями энергии упругие элементы закручиваются угол, пропорциональный моменту сопротивления на шпинделе. В пределах профиля кулачка обеспечиваются различные деформации упругих элементов в зависимости от моментов сопротивления на шпинделе. Под воздействием момента сил упругости механизм свободного хода стремится повернуться в обратную сторону и запасенный момент упругих сил прикладывается к шпинделю.
Точность момента затяжки данного завинчивающего устройства в основном зависит от люфтов муфты свободного хода. Данные устройства обеспечивают малые моменты затяжки и могут применяться для завинчивания и затяжки шпилек с диаметром резьбы не более 4 мм. Конструктивно устройство может одновременно завинчивать только две резьбовые детали.
В системе с обратными связями используются следующие виды контроля:
- контроль максимального крутящего момента. В этом случае фактическое максимальное значение момента сравнивается с допустимыми нижними и верхними пределами.
- контроль соотношения «крутящий момент – угол поворота». При этом контролируется величина момента при заданном значении угла и наоборот.
- контроль отклонения функции «момент – угол поворота» от линейной зависимости. При этом назначается допуск на отклонение от линейности в заданном диапазоне по моменту и углу.
При использовании последних двух способов завинчивание болта прекращается в тот момент, когда напряжения в нем превысят предел текучести. Использование этих методов контроля уменьшает разброс усилий затяжки.
Недостатком подобных систем является необходимость проведения их периодических тарировок, сложность изготовления и эксплуатации, а также высокая стоимость, и, вследствие, низкая рентабельность применения.
Завинчивающие устройства на основе муфты предельного момента работают следующим образом: при достижении определенного момента сил сопротивления на шпинделе, больше, чем момент, на который настроена муфта, ее полумуфты начинают проскальзывать. Шпиндели будут вращаться с одинаковой «медленной» скоростью синхронно. Поворот шпинделей на одинаковый угол обеспечивается системой отсчета, которая при «прощелкивании» муфты предельного момента передает замыканиям контакта электрические сигналы на счетчик импульсов, который при помощи реле отключает питание двигателя.
Данное устройство также не удовлетворяет требованиям качественной сборки, из-за низкой точности осевых сил затяжки (погрешность более 15%) и имеет ограниченное применение, т.к. можем иметь только четное число шпинделей.
Из этого следует, что существующие средства механизированной сборки изделий с групповыми резьбовыми соединениями, не обеспечивают качественную сборку из-за низкой точности осевых сил затяжки, невозможности одновременного прижатия соединяемых узлов и деталей по плоскостям их сопряжения и отсутствием синхронной затяжки соединений.
Затяжка с помощью головки болта или гайки
Часто задают вопрос: следует ли затягивать гайку или головку болта. В Ответ зависит от того, какой процесс затяжки используется. Для затяжки с контролируемым моментом затягивается ли гайка. и головка болта удерживается, или головка болта затягивается и гайка держится, может иметь значение.
Общая цель от затяжки Процесс заключается в достижении постоянной предварительной нагрузки болта.Контролирующий крутящий момент при затяжке и завершении последующего осмотра проверяет, что достигается заданный крутящий момент, являются распространенными способами достижения этой цели.
При приложении крутящего момента и возникающем в результате натяжении (предварительном натяжении) в болт измеряется во время затяжки и наносится на график, существует линейная зависимость между крутящим моментом и напряжение.Натяжение болта напрямую зависит и пропорционально к, приложенный крутящий момент. Это иллюстрируется графиком, который основан на экспериментальных результатах, что показано на диаграмму выше. По таким результатам испытаний можно установить соответствующий крутящий момент для требуемого предварительного натяга болта это может потребоваться.
Одним из недостатков использования управления крутящим моментом является то, что может быть значительное изменение достигнутого предварительного натяга болта для заданного значения крутящего момента.На это есть несколько причин например неточность в приложении крутящего момента, размерные отклонения изменения размера резьбы и отверстия среди других. Тем не мение, преобладающий фактор обычно связан с изменением трения который присутствует между контактными поверхностями, которые повернутый.
Из испытаний известно, что примерно 50% затяжки крутящий момент рассеивается при преодолении трения под болтом головка или грань гайки (какая бы грань ни вращалась).Обычно на самом деле только от 10% до 15% от общего крутящего момента. используется для затяжки болта, остальное используется для преодоления трения в резьбе и на вращающейся поверхности контакта (торец гайки или головка болта). Это показано на круговой диаграмме. показано выше. Относительно небольшие изменения трения торца гайки может существенно повлиять на предварительный натяг болта. Как более крутящий момент, возможно, необходим для преодоления трения, остается меньше для удлинения болта и, следовательно, в результате неблагоприятного воздействия уменьшение предварительной нагрузки.Если трение под торцом гайки уменьшается, то для данного крутящего момента предварительный натяг болта будет повысился.
приведенная сбоку диаграмма – это, пожалуй, самая распространенная ситуация где верхняя и нижняя пластины стыка сделаны из тот же материал, одинаковая отделка и размер отверстий одинаково для обеих пластин. Для такого стыка, когда размеры торца гайки и головки болта имеют одинаковый диаметр и закончить, не имеет значения, головка болта или гайка затягивается.Некоторые люди считают, что, ужесточая головка болта, а не гайка, она будет влиять на скручивание в хвостовик болта. Кручение стержня болта зависит от момент трения резьбы. Для данного состояния отделки трение нити связано с некоторым разбросом, но не будет зависеть от того, затянуты ли гайка или головка болта. Если момент трения резьбы остается прежним, торсионный в хвостовике будет одинаковым независимо от того, затягивается головка болта или гайка.
На схеме сбоку показана ситуация, когда пластины в состав соединения входят разные материалы (например, один из стали, а другой из алюминия) или иметь различную отделку (например, одна пластина оцинкована, а другая окрашена). В таких ситуациях, как правило, важно затягивается ли головка болта или гайка.Причина в том, что у каждой грани будет разный коэффициент трения. Если затянутый момент был определен либо путем испытаний, либо путем осмотра повысить фрикционные характеристики поверхности, скажем, на основе на поверхности ореха, то вероятно, что поверхность головы будет иметь другой коэффициент трения. Если бы у него было более низкое значение трения, то предварительный натяг будет увеличен, если головка болта была затянута.В крайнем случае, если фрикционный отличия были большими, возможна поломка болта.
На схеме сбоку показан случай, когда зазор отверстие в верхней пластине отличается от отверстия в нижней пластина. Такие ситуации относительно обычны. Существует эффективный радиус трения на вращающейся детали (гайка или головка болта), которое обычно принимается как среднее значение зазора отверстия и радиусы внешней поверхности подшипника.Поскольку эти радиусы будут быть больше для головки болта, чем для гайки в положении показано, что затяжка болта приведет к меньшему предварительному натягу болта. голову, а не гайку, другие факторы, такие как трение, такой же. Отсюда еще один пример ситуации относительно того, гайка или головка болта затянуты.
Рисунок сбоку в том случае, когда есть стиль и размерные различия между головкой болта и гайкой.Эффект аналогичен тому, что происходит в предыдущем кейс. Различия радиусов трения между головками болтов и интерфейс гайка-шайба приводит к влиянию предварительного натяга какой элемент затягивается. В случае, показанном здесь, там вероятно также будет разница между коэффициентом трения это присутствует, когда гайка затягивается на шайбе и головку болта на шарнир.Это увеличило бы изменчивость еще дальше.
Шайбы иногда используются как средство уменьшения трения разброс помимо общей причины снижения подшипника напряжение на суставе лица. Условие трения между поверхность шайбы и гайки можно достаточно хорошо определить и контролировать, больше, чем обычно могут соединительные поверхности. Контролируя трение, предварительная нагрузка может быть достигнута более надежно.К делайте это последовательно, необходима плотная посадка изнутри диаметр шайбы. Один из способов достижения этого за счет использования блока SEMS (в котором шайба удерживается на стержне болта). То же самое можно сделать с помощью KEPS. блок (на гайке закреплена шайба).
В общем, при использовании контроля крутящего момента затяжка
болт вращением головки болта или гайки может иметь значение.это
рекомендуется указать, какую часть следует затянуть, чтобы
что изменение предварительного натяга болта сведено к минимуму.
На эту тему есть статья, которая также может вас заинтересовать.
Что должно быть затянул гайку или головку болта? Опубликовано в номере за март 2006 г. крепежа и крепления в Европе, в этой статье обсуждается вопрос о том, должна ли гайка или головка болта подтянуться и имеет ли это какое-то значение? В ответ зависит от того, какой процесс ужесточения использовал.Для затяжки с контролируемым моментом затяжки гайка затягивается, и головка болта удерживается, или головка болта затянуто и удерживается гайкой, может иметь большое значение. Общая цель от Процесс затяжки заключается в достижении постоянного предварительного натяга болта. Контроль крутящего момента во время затяжки и завершения последующие инспекционные проверки, чтобы убедиться, что указанные крутящий момент достигается, распространены способы, которыми это цель реализована. В этой статье показано, что в как правило, при использовании контроля крутящего момента затягивание болта поворотом головки болта или гайки может иметь значение. Это Хорошая практика – указать, какая часть должна быть затянута так что изменение предварительного натяга болта сведено к минимуму. В обсуждаются затронутые вопросы. |
Чтобы помочь инженеру в преодолении связанных с этим проблем с применением резьбовых соединений и болтовых соединений, Болт Наукой разработано компьютерных программ .Эти программы разработаны так, чтобы их было легко использовать, чтобы инженер без детальных знаний в этой области можно решить проблемы связанные с этой темой.
Что такое гаечный фактор и как он влияет на крутящий момент?
Когда вы затягиваете болт в болтовом соединении, вы используете крутящую силу, называемую крутящим моментом. Крутящий момент связан с затяжкой болта, но многие дополнительные факторы, такие как трение, объединенные в один «фактор гайки», могут иметь значительное влияние на соотношение крутящего момента и плотности болтового соединения.
Вот как это работает: По мере затяжки болта между головкой болта и верхней частью гайки возникает напряжение. Это натяжение фактически заставляет болт немного растягиваться, как при натяжении пружины. Подобно растянутой пружине, которая пытается вернуться в расслабленное состояние, растянутый болт пытается уменьшить напряжение, возвращаясь к своей исходной длине. Результатом является сжатие или усилие зажима, которое притягивает головку болта и гайку друг к другу, сжимая соединение вместе.
Чтобы обеспечить надежность соединения, необходимо создать определенное усилие зажима – слишком большое может привести к деформации соединения или поломке болта, а слишком маленькое может привести к ослаблению и незакреплению соединения. Но как полевой оператор, затягивая болт, определяет, когда было достигнуто достаточное натяжение, чтобы создать нужное усилие зажима?
Связь между напряжением и крутящим моментом
Прямое измерение натяжения болтового соединения традиционно было трудным. Промышленная практика заключалась в измерении крутящего момента, необходимого для затяжки болта, а затем в попытках соотнести этот крутящий момент с натяжением.
Было разработано «краткое» уравнение для преобразования крутящего момента в напряжение:
T = K × F × D
где T – измеренный крутящий момент, K – коэффициент гайки, F – натяжение, а D – диаметр болта. С помощью этого уравнения, если вы знаете K, F и D, вы можете умножить их, чтобы получить крутящий момент, необходимый для затягивания болта, чтобы он имел правильную величину натяжения.
Фактор гайки, K, суммирует комбинированные эффекты многих переменных, влияющих на сложность затяжки болта, таких как трение.Некоторые из этих факторов включают тип и материал болта, шайбы и гайки; наличие и тип покрытия, покрытия или смазки; шаг или угол резьбы болта; и коррозия и износ.
Поскольку очень много переменных влияют на коэффициент гайки, значение коэффициента гайки может изменяться каждый раз, когда болт затягивается, даже если условия кажутся одинаковыми. Таким образом, точное определение коэффициента затяжки для расчета правильной величины крутящего момента, применяемого к болтовому соединению, становится сложной задачей.
Гаечный фактор колеблется
Часто полевой персонал использует таблицу, прилагаемую к динамометрическому ключу, для определения величины крутящего момента, который они должны приложить к болтовому соединению, чтобы получить нужную величину натяжения. Однако эти графики крутящего момента обычно основаны на предположении, что K = 0,2, и эксперименты показывают, что это предположение часто может быть неточным.
Один из способов напрямую определить, будет ли болт затянут должным образом с заданным значением крутящего момента, – это использовать датчик нагрузки, такой как Skidmore-Wilhelm.
Вот пример. Если вы установите гайку и болт в датчике нагрузки Скидмора-Вильгельма и затянете болт до определенной величины отсечки с помощью динамометрического ключа, фактическое измеренное натяжение не обязательно будет соответствовать натяжению, указанному в таблице крутящего момента. Если вы повторите этот процесс несколько раз, используя одни и те же болт, гайку, гаечный ключ и отрезные приспособления, натяжение может каждый раз измеряться разной величиной.
Тот факт, что показания натяжения непостоянны и их трудно предсказать, указывает на то, что коэффициент гайки менялся от одного раза к другому.Поскольку истинный коэффициент затяжки гайки может варьироваться в довольно широких пределах, использование характеристик крутящего момента для определения затяжки иногда может повлиять на герметичность болтового соединения. Это может привести к выходу из строя болтов, что может привести к дорогостоящим простоям или даже несчастным случаям.
Освобождение от орехового фактора
К счастью, теперь есть простой способ обеспечить безопасность болтовых соединений. Вместо использования динамометрических инструментов и сомнительных характеристик крутящего момента пользователи могут измерять фактическое натяжение болта во время установки, а затем постоянно контролировать болты на предмет потери натяжения во время эксплуатации.Болты с индикатором прямого натяжения – это надежный способ измерить натяжение болта без учета крутящего момента. Больше никаких динамометрических ключей, таблиц крутящего момента, коэффициента затяжки или краткого уравнения – даже никаких опасений по поводу чрезмерной или недостаточной затяжки.
Чтобы полностью обойти измерение коэффициента затяжки гаек и крутящего момента, вы можете измерить натяжение болта напрямую с помощью SmartBolts®. Запатентованная система визуальной индикации ™ измеряет величину растяжения, создаваемого затянутым болтом, чтобы гарантировать постоянное усилие зажима на критически важных болтовых соединениях.
Для получения дополнительной информации о том, как коэффициент гайки соотносится с крутящим моментом в болтовом соединении, см. Нашу предыдущую запись в блоге: Проблема гайки.
Индикатор SmartBolts изменится с красного на черный, когда будет достигнуто надлежащее натяжение, и станет полностью обратимым в течение всего срока службы застежки.
Спецификации крутящего момента для крепежа
Крутящий момент прилагается к крепежному элементу, чтобы упруго деформировать стержень болта. В случае болтов и гаек эта упругая деформация между головкой болта и гайкой имеет решающее значение для создания натяжения или зажимного усилия, удерживающего соединение вместе.Величина прилагаемого крутящего момента является функцией сил трения и диаметра болта и обычно рассчитывается с использованием зажимной нагрузки, равной 60-70% от текучести. Ниже приведены руководства, которые показывают эти расчеты для различных материалов, размеров болтов и количества резьбы в различных условиях трения.
ПРИМЕЧАНИЕ: Фактическая нагрузка зажима зависит от множества факторов, включая материал, состояние крепежа, качество поверхности, смазку и т. Д. Приведенные проценты иллюстрируют то, что можно было бы ожидать, и их следует использовать только в качестве общего руководства. .* Предел текучести, используемый для расчета значений крутящего момента, основан на типичном текучести. *
ВНИМАНИЕ! формула для соотношений крутящий момент / натяжение. Крутящий момент – лишь косвенный показатель напряжения. Недостаточная / чрезмерная затяжка креплений может привести к дорогостоящему отказу оборудования или травмам. Все данные, включенные в эту таблицу, носят рекомендательный характер, и их использование кем-либо является добровольным.Приведенные данные следует использовать в качестве ориентировочных, но фактическая прочность материала и условия крепления могут отличаться. Разрабатывая эту информацию, Extreme Bolt & Fastener, LLC приложила решительные усилия для точного представления ее содержания.
Крепление. (2009). [Иллюстрация растяжения: зависимость напряжения от деформации] Конструкция болтового соединения: механические свойства стальных крепежных изделий в эксплуатации.
Спецификация крутящего момента A-286
Спецификация крутящего момента AL-6XN
Спецификация крутящего момента сплава 20
Спецификация крутящего момента сплава 330
Duplex Характеристики крутящего моментаХастеллой C276 Характеристики крутящего момента
Характеристики крутящего момента Incoloy que Технические характеристикиХарактеристики крутящего момента для молибдена
Технические характеристики крутящего момента для молибдена TZM
Характеристики крутящего момента Monel 400 и K500
Момент затяжки CP 2.Характеристики крутящего момента 5% WХарактеристики крутящего момента для титана Gr2 и Gr5
Характеристики крутящего момента Waspaloy
Цирконий 702 и 705 крутящего момента
Калькулятор – определение правильного момента затяжки болта Правильный расчет крутящего момента до болтовБолты и винты настолько распространены, что невозможно полностью сформулировать их важность или применение.Эти застежки буквально скрепляют мир вокруг нас. От суровых условий промышленности до грохота автомобилей, поездов и самолетов, до мебели, которая украшает наши дома и офисы, болты играют неотъемлемую роль в сборке материалов, которые структурируют нашу жизнь.
Возможно, именно из-за их повсеместности болты так недооцениваются как механический компонент. Слишком часто выбор болтов производится в спешке. Покупатель считает, что проблема сборки решена после рассмотрения всего нескольких параметров.Какой диаметр и длина хвостовика мне нужны? Метрическая или британская? Шаг резьбы?
Когда соединение, скрепляемое болтами, выходит из строя, не только разрушаются детали, но покупатель не понимает, почему это соединение вышло из строя. Что еще хуже, недовольный покупатель часто перекладывает вину на неисправное оборудование или посредственного поставщика.
Но поставщик, обладающий превосходными знаниями о продуктах и превосходным обслуживанием клиентов, может оказать огромное влияние на чистую прибыль вашей компании. Bayou City Bolt имеет более чем 50-летний опыт оказания помощи клиентам в поиске подходящего оборудования для любого приложения.Заказы на крепеж от Bayou City Bolt поступают вовремя; болты всегда соответствуют спецификации и доступны любой организации.
Почему крутящий момент имеет значениеПочему это соединение вышло из строя? Скорее всего, это была проблема недостаточного крутящего момента. Правильная затяжка имеет жизненно важное значение для функционирования болта и определяется несколькими, часто противоречащими друг другу факторами.
Материал правильно затянутого болта слегка растянут, но не превышает предел упругости. Материал болта, чаще всего сталь, сопротивляется этому естественному растяжению и создает усилие зажима на собранных основаниях.Точно так же материалы подложки сопротивляются сжатию, чтобы уравновесить давление зажима; это называется предварительным натягом сустава. Правильно затянутый болт распределяет предварительную нагрузку с деталями.
Болт с чрезмерной затяжкой, растянутый за пределы своего предела упругости, сильно ослаблен, что снижает его полезную нагрузочную способность. Недостаточно затянутый болт или винт допускают незначительное расстояние между деталями, что поначалу кажется тривиальным, но после постоянной динамической нагрузки или других рабочих нагрузок зазор между деталями будет увеличиваться.Зазор в соединении означает отсутствие предварительного натяга соединения. Без обратной силы сжатых субстратов, болт используется исключительно для сборки соединения – условие, которое неизбежно приводит к разрушению соединения.
Как определить подходящий крутящий момент к соотношению болтаДаже опытные мастера затягивают болты с повышенным или недостаточным крутящим моментом. По правде говоря, информация о продукте редко предоставляет значения крутящего момента. Общие значения крутящего момента болтов можно найти, но найти точную справочную информацию не всегда легко.Момент затяжки болта можно проверить с помощью такого инструмента, как динамометрический ключ, но без значения в качестве ориентировочного значения динамометрический ключ не дает никаких преимуществ. Чтобы получить правильное значение крутящего момента, сначала необходимо найти несколько других значений.
Два принципа влияют на правильное давление зажима для каждого болта, известное как зажимная нагрузка. Во-первых, диаметр болта. Второй – это класс болта, определяемый его прочностью на растяжение, которая, в свою очередь, определяется материалом конструкции. К счастью, организации по стандартизации объединили стандартные значения прочности на разрыв для обычных болтов в простые в использовании стандарты.SAE J429 регулирует британские размеры, а ISO 898 – метрические размеры.
SAE J429 | |||
Марка болта | Материал болта | Диаметр болта | Минимальная прочность на разрыв |
2 класс | Углеродистые стали от низкого до среднего класса | от 1/4 до 3/4 дюйма > 3/4 – 1 1/2 дюйма | 74000 фунтов на кв. Дюйм 60,000 фунтов на кв. Дюйм |
5 класс | Среднеуглеродистые стали, подвергнутые закалке и отпуску | от 1/2 до 1 дюйма > от 1 до 1 1/2 дюйма | 120,000 фунтов на кв. Дюйм 105000 фунтов на кв. Дюйм |
8 класс | Среднеуглеродистые стали, подвергнутые закалке и отпуску | от 1/4 до 1 1/2 дюйма | 150 000 фунтов на кв. Дюйм |
18-8 классы | Нержавеющая сталь | от 1/4 до 1 1/2 дюйма | 65000 фунтов на кв. Дюйм |
ISO 898 | |||
Класс болтов | Материал болта | Диаметр болта | Минимальная прочность на разрыв |
Класс 8.8 | Среднеуглеродистые стали, подвергнутые закалке и отпуску | <16 мм от 16 до 72 мм | 800 МПа 830 МПа |
Класс 10.9 | Легированные стали , прошедшие закалку и отпуск | от 5 до 100 мм | 1040 МПа |
Класс 12.9 | Легированные стали , прошедшие закалку и отпуск | от 1,6 до 100 мм | 1220 МПа |
Класс A-2 | нержавеющая сталь | Все через 20 мм | 500 МПа |
Для болтов с дюймовой шкалой наиболее распространены классы 5 и 8.Болты, соответствующие стандарту SAE J429, будут иметь радиальную маркировку на головке болта, которая указывает класс болта. Болт степени 2 не имеет маркировки, болт степени 5 будет иметь три маркировки, а болт степени 8 будет иметь шесть линий. Метрические болты идентифицируются проще: класс явно указан на головке болта.
Другие стандарты регулируют конкретные типы или области применения болтов, и с ними следует обращаться по мере необходимости. Примеры включают, но не ограничиваются приведенными в сопроводительной таблице.
Стандартный | Характеристики болтов | Диаметр болта | Минимальная прочность на разрыв |
ASTM A325 | Стандартные спецификации на конструкционные болты, сталь, термообработанные | ½ до 1 дюйма > 1–1½ дюйма | 120,000 фунтов на кв. Дюйм 105000 фунтов на кв. Дюйм |
ASTM A490 | Стандартные спецификации на конструкционные болты из легированной стали с термообработкой | ½ – 1½ дюйма | 150 000 фунтов на кв. Дюйм |
ASTM A193 B7 | Стандартные спецификации для болтовых соединений из легированной и нержавеющей стали для работы при высоких температурах или высоком давлении и других специальных применений | До 2 ½ дюйма > от 2½ до 4 дюймов | 125000 фунтов на кв. Дюйм 115000 фунтов на кв. Дюйм |
Используя информацию о классе болта, зажимную нагрузку болта можно определить с помощью следующего уравнения.
P = St x As
Где:
P: зажимная нагрузка
St: прочность на разрыв болта
As: зона растягивающего напряжения
Значение площади растягивающего напряжения можно определить по формуле:
As = π / 4 x (D – (.938194 x p)) ²
Где:
D: диаметр болта
p: 1 / ниток на дюйм (TPI)
Усилие зажима обычно составляет около 75% от испытательной нагрузки болта; то есть наибольшее напряжение, которое болт может выдержать перед пластической деформацией. Сама испытательная нагрузка обычно составляет от 85% до 95% предела текучести болта, но зажимная нагрузка значительна, поскольку именно она в конечном итоге обеспечивает зажимное давление. После определения нагрузки зажима найти правильное значение крутящего момента для болта станет одним простым расчетом.
T = K x D x P
Где:
K: коэффициент трения (определяемый обработкой поверхности болта)
Общие значения коэффициента трения:
Поверхность болта | К |
Без покрытия, черная отделка | 0,3 |
оцинковка | 0,2 |
со смазкой | 0.18 |
с кадмиевым покрытием | 0,16 |
В качестве примера мы можем использовать уравнение, чтобы найти правильное значение крутящего момента для оцинкованного тяжелого конструкционного болта, в данном случае принадлежащего ASTM A325 с диаметром дюйма и 10 TPI.
As = π / 4 x (3/4 дюйма – (.938194 / 10)) ²
As = 0,3383 дюйма²
Используя это значение, теперь можно определить усилие зажима.
P = 85000 x 0,3382
P = 28 747 фунтов.
И, наконец, значение крутящего момента для этого болта может быть
T = 0,2 x 3/4 x 28 747
T = 4,312 дюймов – фунт
Во многих отношениях Bayou City Bolt похожи на болты, которые мы продаем: они изготовлены с соблюдением принципов целостности, полностью надежны и являются фундаментальной частью операционной стабильности. В дополнение к непревзойденному каталогу труднодоступных крепежных изделий с минимальными затратами, Bayou City Bolt является ведущим поставщиком оборудования на юге Соединенных Штатов. Убедитесь сами в том, что наши клиенты уже знают: мельчайшие компоненты могут иметь наибольшее значение в любой отрасли.
Скачать PDF
Крутящий момент против зажима – и что это означает для целостности соединения и устойчивости к вибрации
Крутящий момент против зажима – и что это означает для целостности соединения и устойчивости к вибрации 25 апреля 2018 г.Кирсти Хёрн, исполнительный директор по маркетингу, Arconic Крепежные системы и кольца
Для большинства случаев применения тяжелого оборудования инженеры-конструкторы сосредоточили внимание на стабильном, неизменно герметичном соединении, обеспечивающем долговечность и устойчивость к вибрации.В то же время крутящий момент долгое время был стандартом, по которому измеряется герметичность и, возможно, даже общая целостность соединения.
Это традиционное мышление было основано на идее о том, что чем больше силы, прилагаемой к гайке и болту в виде крутящего момента, тем более плотно, надежно и устойчиво к вибрации соединение. И, как выясняется, как и многие традиционные представления, мнение о том, что более высокий крутящий момент приводит к более надежному и прочному соединению, было ошибочным.
Крутящий момент применительно к крепежным деталям – это крутящая сила, необходимая для закручивания гайки вдоль резьбы болта.Основная формула для крутящего момента: T = (KDP) / 12, где T = крутящий момент в фунтах-футах, D = номинальный диаметр в дюймах, P = желаемая нагрузка зажима или натяжение в фунтах и K = коэффициент трения. Проблема с этим уравнением заключается в том, что K чрезвычайно трудно предсказать или измерить, поскольку на него влияет широкий спектр переменных, таких как текстура поверхности, масло, ржавчина, мусор, тип резьбы, материал и даже влажность.
Еще одним элементом уравнения соединения, натяжением, является растяжение или удлинение болта, обеспечивающего зажим соединения.Дальнейшее объяснение определило бы натяжение как нагрузку на соединение, вызванную стягиванием компонентов застежки вместе. Решающее значение для процесса соединения, натяжение по большей части не связано с крутящим моментом. В лучшем случае крутящий момент – это косвенное измерение усилия, приложенного к болту.
Зажим – реальная мера целостности соединения
Зажим, определяемый как нагрузка на соединение, вызываемая стягиванием компонентов крепежа, практически не связана с крутящим моментом.Фактически, продолжающиеся исследования зажима с использованием сложного оборудования для испытаний перед нагрузкой Skidmore-Wilhelm четко установили, что даже когда крутящий момент между двумя или более гайками и болтами абсолютно одинаков, величина зажима этих креплений может варьироваться более чем на 30% ( Диаграмма первая). Для сравнения, стопорный болт HuckBolt® будет отличаться на 5% или меньше. Это важный момент, учитывая тот факт, что зажим является критическим элементом целостности и долговечности соединения.
Зажим не только является истинным показателем качества соединения, но и имеет решающее значение для его долговечности.Если зажим слабый или непоследовательный, болт может испытывать ту же рабочую нагрузку, что и соединение. При ослабленном болте на болт прикладывается циклическая нагрузка, которая вызывает его усталость. Такая модель разрушения обычно возникает при высокочастотной нагрузке, и часто требуется всего несколько циклов для медленного распространения трещины по поперечному сечению болта. Гайка и болт либо ослабнут, либо выйдут из строя, когда уменьшенная площадь поперечного сечения болта станет достаточно низкой, чтобы он больше не мог выдерживать нагрузку.
Точно так же, если в соединении несколько болтов и между ними существует непоследовательный зажим – у одних болтов их больше, чем у других – результат будет проблематичным. Болты с большим зажимом будут нести большую рабочую нагрузку. Болты, которые менее зажаты, вносят небольшой вклад в прочность соединения или вообще не вносят никакого вклада по сравнению с болтами, имеющими надлежащий зажим. Например, в приложении, где только три болта из шести имеют надлежащий зажим, эти три крепежа с надлежащим зажимом вынуждены нести большую часть нагрузки.Поскольку конструкция соединения предусматривает использование шести болтов, соединение фактически поддерживается только тремя из шести болтов, изначально предусмотренных в конструкции. Поскольку эти три болта несут большую часть нагрузки, рассчитанной на шесть болтов, они очень склонны к выходу из строя.
- Болт или гайка затянут с предписанным крутящим моментом.
- Болт растянут.
- Требуемый зажим достигнут.
Однако процесс обычно не протекает таким предсказуемым образом. X-фактор – это коэффициент трения K, который сильно варьируется в зависимости от многих факторов, перечисленных ранее. Основываясь на многих вариациях K, после затяжки болта до расчетного значения могут иметь место следующие сценарии:
- Болт можно растянуть, но не до необходимой длины.
- Болт может быть чрезмерно растянут, превышая предел текучести.
- Выход инструмента может не соответствовать требуемому крутящему моменту.
Эти и многие другие неуправляемые переменные могут и будут приводить к непредсказуемым результатам.
Крепление с прямым натяжением – самый надежный метод обеспечения надежного зажима
Сегодня многие инженеры отходят от обычного крепления гаек и болтов, при этом даже различные стопорные шайбы и гайки считаются недостаточными для обеспечения необходимого постоянного зажима и надежной фиксации для приложений с высокой вибрацией.Болты HuckBolts с прямым натяжением, предлагаемые Arconic Fastening Systems and Rings, чаще используются для обеспечения надежности надежного зажима и устойчивости к вибрации.
, предлагаемые в широком диапазоне размеров (до 36 мм) и из различных материалов, зарекомендовали себя в некоторых из наиболее сложных областей применения оборудования, включая тяжелый транспорт, сельское хозяйство и горнодобывающую промышленность. Эти застежки, состоящие из штифта и хомута, устанавливаются методом прямого натяжения, при котором штифт вытягивается, а хомут одновременно вдавливается в фиксирующие канавки штифта.Основываясь на своей конструкции и уникальной установке прямого натяжения, HuckBolts обеспечивает надежный зажим для прочного и долговременного стабильного соединения. Сравнение различных способов установки крепежа приведено в таблице ниже:
Устранение воздействия вибрации
Помимо обеспечения наиболее надежного зажима, HuckBolts имеет несколько конструктивных элементов, которые также обеспечивают их максимальную устойчивость к воздействию вибрации. При обычных установках гайки и болта зазоры между резьбой гайки и болта встречаются повсеместно, что дает возможность ослабления в условиях высокой вибрации.Напротив, конструкция Huck, в которой буртик полностью вставлен в стопорные канавки штифта, не создает такого проблемного зазора (диаграмма 2).
Вместо глубокой резьбы, необходимой для обеспечения посадки с допуском между обычными гайками и болтами, для штифта HuckBolt требуются только неглубокие стопорные канавки, в которые зажимается кольцо. Неглубокая конструкция стопорных канавок позволяет получить гораздо больший радиус основания, что значительно увеличивает усталостную прочность – до 5 раз по сравнению с обычной гайкой и болтом.В целом, стопорный болт HuckBolt обеспечивает превосходную устойчивость к вибрации, как показано в исследовании, приведенном ниже (диаграмма 3).
Устойчивость к вибрации означает отсутствие необходимости в обслуживании.
Поскольку передовая технология крепления марки Huck® доказала свою стойкость к воздействию вибрации без ослабления, болты HuckBolts не нуждаются в проверке, затяжке или повторной затяжке. Преимущества, которые дает эта способность противостоять воздействию вибрации, значительны:
- Устраняется один дорогостоящий аспект обслуживания башни, поскольку нет необходимости тратить рабочую силу и время, необходимые для периодической проверки, затяжки и затяжки имеющихся креплений.
- Кроме того, башню, собранную с помощью HuckBolts, никогда не придется отключать для проверки и восстановления креплений.
- Наконец, использование устойчивых к вибрации болтов HuckBolts практически исключает возможность возникновения проблем с безопасностью из-за неисправного крепежа.
Уникальные вибростойкие характеристики HuckBolts дополнительно подтверждаются тем фактом, что BobTail® HuckBolt – единственный в своем роде крепеж, сертифицированный престижным институтом DIBt как не требующий обслуживания (12 мм, 14 мм, 16 мм, 20 мм и 1 мм). дюймовые диаметры).На основании этой сертификации теперь можно использовать расширенный BobTail; безопасен тем, что соответствует высоким стандартам Института как для статических, так и для динамических приложений гражданского строительства.
BobTail® – HuckBolt для ветряных башен
Сертифицированный DIBt HuckBolt доказал свою ценность при производстве ветряных башен. Помимо проверенной устойчивости к вибрации, эта усовершенствованная застежка со стопорным болтом обеспечивает в пять раз большую усталостную прочность по сравнению с обычными болтами и гайками.BobTail доступен в размерах от 10 мм до 36 мм, что делает его применимым к широкому спектру креплений, связанных с ветряными мачтами.
В отличие от обычных стопорных болтов, BobTail не требует снятия штифта в процессе установки, что устраняет потенциальную проблему коррозии в открытой области поломки штифта. Кроме того, эргономичная оснастка BobTail не подвергает персонал, выполняющий монтаж, постоянным сотрясениям, которые возникают, когда обычный стопорный болт защелкивается.Рабочие гораздо более продуктивны и, безусловно, менее подвержены повторяющимся стрессовым ситуациям, которые могут возникнуть в результате сотрясения, возникающего при щелчке шилом.
Существует ряд других преимуществ, связанных с
, использующим технологии крепежа BobTail при изготовлении ветроэнергетических конструкций. Установка выполняется быстро и легко, и монтажный персонал требует очень небольшого обучения. Кроме того, все, что требуется для точной установки крепежа, – это быстрый визуальный осмотр.
Предварительный натяг от момента затяжки и снятия
Крепежные детали с резьбой продолжают находить широкое применение в конструкциях, машинах и механизмах. Во многих случаях их функция заключается в обеспечении предварительного натяга в суставе. Наиболее распространенный метод создания предварительной нагрузки в болтовом соединении – это контроль (то есть приложение и измерение) момента затяжки крепежа с помощью динамометрического ключа [1,2,3,4]. Разработчик определяет момент затяжки на основе ранее полученных данных о крутящем моменте и натяжении для крепежа в данном соединении, чтобы достичь желаемого предварительного натяга в пределах диапазона, диктуемого неопределенностью предварительного натяга в результате использования управления моментом затяжки.Эта неопределенность предварительного натяга указана [2] как плюс и минус 35% для крепежных изделий без смазки или в состоянии поставки. Оно снижается до плюс и минус 25% для крепежных деталей со смазкой, т. Е. Со смазкой, нанесенной на поверхность раздела резьбы и поверхность гайки (или поверхность болта при использовании вставок). В качестве альтернативы, неопределенность может быть определена путем испытания образцов аппаратного обеспечения крутящим моментом – растяжением и статистического анализа [2]. Образец оборудования включает те же крепежные детали, смазочные материалы, оборудование для сборки и процесс установки, что и при сборке приложения.
Номинальный предварительный натяг, F p , определяется с точки зрения монтажного момента затяжки T t , как
$$ F _ {\ text {p}} = \ frac {{T _ {\ текст {t}}}} {kD} $$
(1)
Здесь k – коэффициент гайки, определенный из данных крутящего момента и натяжения, а D – номинальный диаметр болта. Минимальный и максимальный предварительный натяг определяются из номинального предварительного натяга F p и погрешности Γ ,
$$ \ begin {array} {* {20} c} {F _ {{{\ text {p}} \, \ hbox {min}}} = (1 – \ varGamma) F _ {\ text {p}}} \\ {F_ {p \, \ hbox {max}} = (1 + \ varGamma) F _ {\ text {p}}} \\ \ end {array} $$
(2)
Погрешность указывается или определяется на основе данных крутящего момента и натяжения.Уравнения для минимальной и максимальной предварительной нагрузки часто включают дополнительные параметры для учета изменения предварительной нагрузки из-за релаксации, ползучести и изменения температуры [1,2,3].
В качестве примера разработчик указывает момент затяжки 60 дюймов на фунт для крепежных деталей 0,25–28 без смазки для достижения номинальной предварительной нагрузки 900 фунтов с погрешностью плюс и минус 35%. Это означает, что момент затяжки 60 дюймов на фунт обеспечит предварительный натяг между минимальным предварительным натягом в 585 фунтов (т. Е. 900 минус 35%) и максимальным предварительным натягом в 1215 фунтов (900 плюс 35%).В процессе проектирования необходимо проверить, что минимальная предварительная нагрузка достаточна для удержания соединения вместе, а максимальная предварительная нагрузка не слишком велика, чтобы повредить крепежные детали или соединение. Этот пример иллюстрирует, почему некоторые конструкторы используют номинальный предварительный натяг 65% предела текучести болта. А именно, максимальный предварительный натяг от номинального предварительного натяга плюс 35% неопределенности соответствует 100% пределу текучести болта.
Менее распространенные методы достижения предварительного натяга основаны на контроле угла поворота или растяжения болта. Они обеспечивают меньшую неопределенность, но требуют использования менее распространенного и более дорогого оборудования по сравнению с динамометрическим ключом, а также дополнительного обучения, техники и подготовки.
Неопределенность предварительного натяга при использовании измерения угла поворота для предварительного натяга указана [2] как плюс и минус 25% или как определено при испытании на угол поворота образцов оборудования и статистическом анализе.
Измерение растяжения болта производится с помощью специальных штангенциркулей или микрометра, ультразвукового оборудования или тензодатчиков. Все это требует дополнительной подготовки крепежа, такой как обработка концов болтов или приспособлений для тензодатчиков и приборов. Неопределенность предварительного натяга при использовании измерения растяжения болта для предварительного натяга указана [2] как плюс и минус 10% или как определено в результате тестирования образцов оборудования и статистического анализа.
Из трех перечисленных методов затяжка с моментом затяжки имеет то преимущество, что для реализации требуются общие инструменты, методы и обучение, но имеет самую высокую неопределенность, тогда как методы угла поворота и растяжения болта обеспечивают меньшую неопределенность, но обычно более дороги и требуют дополнительных инструменты, подготовка, техника и обучение.
В этой статье представлен новый подход к определению предварительного натяга по крутящему моменту. Вместо того, чтобы использовать только момент затяжки с существующими данными о крутящем моменте и натяжении для достижения предварительной нагрузки, при установке используются измерения момента затяжки и момента снятия.Никаких существующих данных о крутящем моменте и натяжении не требуется. Предварительный натяг пропорционален моменту затяжки за вычетом момента снятия. Подход основан на уравнениях крутящего момента. Приведены данные испытаний, которые показывают, что этот подход является жизнеспособным с меньшей неопределенностью по сравнению с использованием одного момента затяжки. Приведены причины уменьшения неопределенности.
Шпильки – Таблицы моментов затяжки – Таблица 2
Таблицы крутящих моментов основаны на конкретных предположениях относительно коэффициента затяжки болта и гайки. Перед использованием данной таблицы крутящего момента следует проверить эти допущения, чтобы убедиться, что они подходят для конкретного применения.
Даже если все предположения верны, результаты могут отличаться в зависимости от реальных условий. Многие факторы вызывают разброс результатов или увеличивают вариабельность процесса болтового соединения. К ним относятся вариации орехового фактора; состояние болта, фланца и гайки; калибровка и состояние оборудования; перпендикулярность болта, гайки и фланца; пр.
Значения в таблицах основаны на уравнении:
T = значение крутящего момента, (фут-фунт) F = предварительная нагрузка болта, (фунт) k = коэффициент затяжки в зависимости от используемого смазочного материала d = номинальный диаметр болта, (дюйм.) |
Фактор гайки – это не коэффициент трения.
Это экспериментально полученная константа, которая включает влияние трения.
фут-фунт в нм = 0,737562149277
нм в фут-фунт = 1,3558179
Таблица 2 / Крутящий момент FT-LBS – Болты шпильки ASTM 193, класс B7 и ASTM 193, класс B16 | |||
БОЛТ ДИАМЕТР | Крутящий момент FT-LBS | ||
30% начальный Крутящий момент | 70% Крутящий момент | 100% Окончательный Крутящий момент | |
1/2 | 17 | 39 | 55 |
9/16 | 24 | 55 | 80 |
5/8 | 33 | 77 | 110 |
3/4 | 59 | 137 | 195 |
7/8 | 93 | 217 | 310 |
1 | 140 | 325 | 465 |
1.1/8 | 205 | 480 | 685 |
1¼ | 288 | 672 | 960 |
1,3 / 8 | 391 | 915 | 1305 |
1½ | 518 | 1208 | 1725 |
1,9 / 16 | 588 | 1372 | 1960 |
1,5 / 8 | 668 | 1558 | 2225 |
1¾ | 840 | 1960 | 2800 |
1.7/8 | 1044 | 2436 | 3480 |
2 | 1280 | 2985 | 4265 |
2¼ | 1850 | 4315 | 6165 |
2½ | 2565 | 5985 | 8550 |
2¾ | 3121 | 7282 | 10400 |
3 | 4080 | 9520 | 13600 |
Таблица 2 / Крутящий момент, Нм – Шпильки ASTM 193, класс B7 и ASTM 193, класс B16 | |||
БОЛТ ДИАМЕТР | Момент Нм | ||
30% начальный Крутящий момент | 70% Крутящий момент | 100% Окончательный Крутящий момент | |
1/2 | 23 | 53 | 75 |
9/16 | 33 | 75 | 108 |
5/8 | 45 | 104 | 149 |
3/4 | 80 | 186 | 264 |
7/8 | 126 | 294 | 420 |
1 | 190 | 441 | 630 |
1.1/8 | 278 | 651 | 929 |
1¼ | 390 | 911 | 1302 |
1,3 / 8 | 530 | 1241 | 1769 |
1½ | 702 | 1638 | 2339 |
1,9 / 16 | 797 | 1860 | 2657 |
1,5 / 8 | 906 | 2112 | 3017 |
1¾ | 1139 | 2657 | 3796 |
1.7/8 | 1415 | 3303 | 4718 |
2 | 1735 | 4047 | 5783 |
2¼ | 2508 | 5850 | 8359 |
2½ | 3478 | 8115 | 11592 |
2¾ | 4232 | 9873 | 14101 |
3 | 5532 | 12907 | 18439 |
Примечания:
- Момент затяжки для достижения 50% -ного предела текучести болта при гаечном коэффициенте, K = 0.16
- Эта таблица применима к пасте Never-Seize и смазке Fel-Pro, K = 0,16.
- Приведенная выше таблица применима только для шпилек ASTM A320 класса L7, A193 класса B7 и A193 класса B16.
- Значения крутящего момента утверждены для прокладок со спиральной навивкой из графита и ПТФЭ, прокладок из графитового листа типа GHE и GHR, кольцевых соединений, прокладок с двойной рубашкой и прокладок Camprofile с графитом и футеровкой из ПТФЭ.
- Окончательное значение крутящего момента учитывает ослабление болта на 10%.
- Эта таблица не подходит для болтов и гаек с покрытием из ПТФЭ, см. Таблицу 5.