Примеры успешного применения: Mobilith SHC 007
Опорный подшипник прошивного стана Timken T921 на трубопрокатном заводе | РоссияОписание
На протяжении двух лет минеральная смазка, производимая одним из наших конкурентов, использовалась для смазки опорных подшипников (стоимость одного подшипника составляет 21 000 долларов США) в регуляторе тяги прошивного стана «450». Оборудование работало непрерывно и на полную мощность, испытывая осевые нагрузки до 350 тонн. Первоначально смазка автоматически восполнялась со скоростью 250 г/час, однако в связи со сбоями в работе подшипников объем подачи пришлось увеличить до 500 г/час. Несмотря на последовавшие за этим улучшения в работе оборудования, износ роликов и сепараторов подшипников предотвратить не удалось. Пять подшипников пришлось заменить, причем два из них стали причиной незапланированного простоя продолжительностью тридцать два часа, что привело к производственным потерям в объеме 1600 тонн продукции. Кроме того, профилактические осмотры приходилось теперь проводить чаще — один раз в два месяца.
Рекомендации
Инженер компании ExxonMobil рекомендовал клиенту использовать Mobilith SHC™ 007 — синтетическую смазку с более низким классом NLGI, обладающую большей глубиной проникновения. Превосходные высокотемпературные характеристики придают этой смазке бóльшую стабильность, а структурная устойчивость в сочетании с особым набором присадок обеспечивают длительную и надежную защиту оборудования.
Преимущества
За 3 года успешной эксплуатации Mobil Vacuoline 525 клиент смог сократить расход масла на 50%. Кроме того, отказы подшипников, связанные с недостаточной смазкой, были устранены. Клиент больше не испытывал проблем с эмульсией или образованием осадка в масле, а также с коррозией оборудования.
* Данное подтверждение эффективности применения основывается на опыте одного клиента. Фактические результаты могут варьироваться в
зависимости от типа используемого оборудования, условий его обслуживания, эксплуатации и окружающей среды, а также типа ранее используемого смазочного материала.
** На сайте mobil.ru/industrial можно получить дополнительную информацию о том, как смазочные материалы Mobil способствуют уменьшению вредного воздействия на окружающую среду. Фактические преимущества будут зависеть от выбранного продукта, условий эксплуатации и оборудования.
Подшипник вполоборота | Журнал Кузов
На первый взгляд опорный подшипник амортизационной стойки может показаться деталью не столь сложной в изготовлении – ведь он за свою жизнь не делает такого большого числа оборотов, как другие подшипники. Однако именно эта специфика работы, в сочетании с критической важностью для безопасности движения, накладывает особые требования.

Неисправность подшипника приводит к нарушению углов установки колес, влияет на безопасность вождения и провоцирует быстрый выход из строя стойки амортизатора.
Действительно, опорный подшипник не вращается, а поворачивается вокруг исходного положения, поскольку автомобиль чаще движется по прямой. В среднем 80% времени тела качения находятся в одном месте, а значит, их износ идет неравномерно. Этим и определяются особые требования к смазке и используемым материалам. Основными факторами износа опорного подшипника являются неровности дорожного покрытия и загрязненность, а не естественная выработка ресурса при работе в штатных условиях.
Движение по неровностям ускоряет естественный процесс износа, а при попадании колеса в глубокие ямы, сопровождавшееся «пробоем» подвески, возможна пластическая деформация деталей подшипника с последующим быстрым выходом из строя. Загрязненность же приводит к абразивному износу или блокировке подшипника в опоре с затруднением рулевого управления.
Нормальный ресурс опорного подшипника в стандартных условиях эксплуатации составляет 70-100 тыс. км, что примерно соответствует ресурсу амортизатора. Поэтому при замене амортизатора рекомендуется заменить и опорный подшипник, поскольку оценка его остаточного ресурса при отсутствии видимых повреждений не представляется возможной. Замена тем более актуальна, что его установка при замене амортизационной стойки не требует дополнительного времени. В противном случае, давая гарантию на новый амортизатор, СТО рискует создать рекламационный случай.
Естественно, на практике указанное правило соблюдается не всегда, либо ранее при замене мог быть использован некондиционный подшипник, поэтому при «тугости» рулевого управления следует осматривать опорный подшипник и прилегающие к нему детали. Наиболее простой способ определить состояние опорного подшипника – открыть капот, взяться рукой за стойку амортизатора в месте ее крепления к кузову и резко покачать из стороны в сторону (или попросить кого-то толкать крыло вбок). Если в подшипнике есть люфт или он рассыпался, стойка будет двигаться относительно кузова с характерными щелчками.
Новый опорный подшипник должен свободно вращаться в руках, без «закусываний» и треска. Правда, такая проверка качества является весьма поверхностной. Лучше все-таки довериться продукции производителя с безупречной репутацией. В этом плане настоящим экспертом по опорным подшипникам является корпорация NTN-SNR, лидирующая в разработке и производстве опорных подшипников для стоек передней подвески МакФерсон с суточным объемом выпуска в 90000 штук.
Чтобы понять, что производство высококачественных опорных подшипников не простая задача, стоит рассмотреть, как новый тип подшипника испытывается в лаборатории NTN-SNR на соответствие техническим спецификациям автопроизводителей. Комплекс предсерийных испытаний длится от одного до трех лет. Определяется жизненный цикл изделия (наработка на отказ) в приближенных к реальным условиям (воздействие грязи, соли, воды). При этом должны сохраняться в целостности уплотнения, обеспечивающие устойчивость к коррозии.
Должен быть строго соблюден момент сил трения, а изменение момента сопротивления вращению на протяжении всего жизненного цикла должно составлять не более 30%. Также на стенде при различных нагрузках проводятся испытания на устойчивость к бринеллированию (возникновению точечных углублений на дорожках качения). Стенд для проведения ресурсных испытаний симулирует работу передней подвески по алгоритмам, моделирующим различные типы дорог и стили вождения.
При конструировании подшипников NTN-SNR использует ПО собственной разработки для моделирования процессов. Подшипники NTN-SNR оснащаются все большим количеством новых функций (седло пружины, упор буфера хода сжатия), в них применяются инновационные подходы: полимерные материалы для снижения веса узла, оригинальные решения по защите от загрязнений и т.д. Основная гамма продукции производится во Франции, также у компании есть производство в Японии и Германии.
Качество подшипников создало фирме репутацию, и потому некоторые производители прибегают к имитации формы и цвета деталей NTN-SNR, чтобы создать впечатление сопоставимости ее по качеству с оригинальной. Однако плохое качество стали, смазки и пластика, неадекватная термическая обработка (закалка) или ее отсутствие – все это может оказать серьезное негативное влияние на срок службы деталей. Использование подобной продукции может привести к повреждению других компонентов подвески и деталей кузова автомобиля.
Помимо низкого качества самого подшипника одной из причин отказов может стать некорректная сборка при замене. Крайне важно использовать при замене все компоненты из набора: винты, болты, гайки и другие компоненты. NTN-SNR включает в свои наборы все компоненты верхней части подвески: подшипники, винты, болты, изолирующие/амортизирующие детали. Каждый компонент испытывается и проверяется сотрудниками отдела контроля качества (тестирование жизненного цикла, анализ твердости материала, анализ химического состава стали).
*Селективная сборка – метод сборки узлов, при котором подбираются сопряженные детали. Поступающие на сборку компоненты сортируются по размерным группам, внутри которых сопрягаемые детали имеют наиболее благоприятные для соединения фактические размеры (с наиболее близкими полями допусков). При изготовлении прецизионных изделий селективная сборка позволяет в разы повысить точность сборки там, где уменьшение допусков уже невозможно технически.
«ТЕХПАРТНЕР» завершил поставку АЦСС для мельниц на «Ковдорский ГОК».
- Главная
- Новости
- «ТЕХПАРТНЕР» завершил поставку АЦСС для мельниц на «Ковдорский ГОК».
13 08.2013
ООО «ТЕХПАРТНЕР» завершил работу для ОАО «Ковдорский ГОК» по проектированию и поставке оборудования автоматических централизованных системы смазки 2-х стержневых мельниц барабанного типа и 2-х шаровых мельниц барабанного типа с приводными шестернями шириной 800мм. с последующей возможностью подключения еще 2-х шаровых и 2-х стержневых мельниц.
Поставленные системы смазки состоит из двух частей:
– Система распыления густой смазки на подвенечную шестерню.
– Система подачи густой смазки на опорные подшипники.
Поставленные системы объединены в единый технологический автоматический комплекс с системой автоматической централизованной заправки всех насосных станций.
Единый технологический автоматический комплекс смазки открытой передачи и опорных подшипников мельниц в сочетании с системой автоматической централизованной заправки всех насосных станций позволяет:
- Гарантированно обеспечить увеличение срока эксплуатации зубчатых венцов и приводных шестерней;
- Исключить возможные потери производства, за счет сокращения количества остановок мельниц связанных с внеплановой заменой приводных шестерней;
- Сократить материальные затраты на приобретение запасных частей;
- Повысить безопасность труда при эксплуатации вновь внедряемого оборудования и улучшить условия труда промышленного персонала;
- Сократить расхода смазочного материала;
- Повысить культура производства;
- В значительной степени снизить загрязнение окружающей среды.
Аналогичный технологический комплекс смазки открытой передачи и смазки опорных подшипников уже был применен на обогатительной фабрике Ковдорского ГОКа в 2009 году для 17 шаровых мельниц, типа МШР 3,6х5,0; МСЦ 3,6х4,5.
Эту работу «ТЕХПАРТНЕР» представлял на конкурсе «Лучший инновационный проект и лучшая научно-техническая разработка года», в рамках Петербургской технической ярмарки – 2009, в номинации «Лучший инновационный проект в области передовых технологий машиностроения и металлургии». И по итогам конкурса она награждена Дипломом 2 степени с вручением серебряной медали.
Опорные подшипники скольжения – Энциклопедия по машиностроению XXL
Эта схема в простейшем виде воспроизводит движение смазочного слоя опорного подшипника скольжения, применяемого, например, в опорах гидрогенераторов и других машин. На примере этой задачи выясняются причины появления поддерживающей силы в подшипниках скольжения.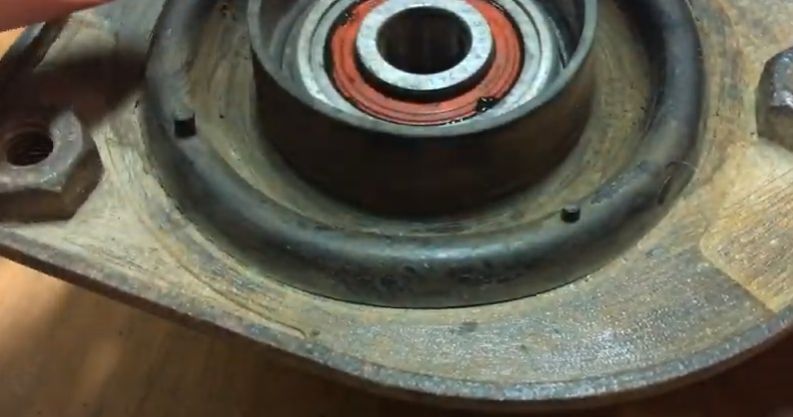
Полиамидные вкладыши опорных подшипников скольжения выполняют в виде монолитных неразрезных либо разрезных втулок. Получают более широкое распространение подшипники с расширительным швом [3, 4, 57], которые имеют ряд преимуществ. Подшипники с расширительным швом подходят для валов с различными допусками на изготовление. Шов компенсирует температурно-влажностные изменения зазора в соединении и одновременно он служит в качестве смазочной канавки. Для уменьшения коэффициента трения применяют различные смазки. [c.242]
Этот насос имеет опорные подшипники скольжения с кольцевой смазкой и двухрядный упорный шариковый подшипник. Сальники насоса снабжены гидравлическим затвором. [c.371]
Автор, однако, не обольщается этим результатом и считает, что только тщательно и широко поставленный эксперимент поможет осветить обилие темных мест в расчетном подходе к работе опорных подшипников скольжения.
[c.66]
Ротор насоса состоит из вала, в середине которого на шпонках насажено рабочее колесо с радиальными лопатками. Колесо фиксируется на валу упорными втулками. Вал вращается в опорных подшипниках скольжения, корпуса которых нижними по- [c.222]
В опорном подшипнике скольжения диаметр отверстия больше диаметра цифры, в результате между цапфой и вкладышем образуется клиновой серповидный зазор. При вращении цапфы смазывающая жидкость вовлекается силами вязкости в сужающийся зазор, что приводит к повышению давления в слое жидкости. При достаточных вязкости смазочного материала и скорости на окружности цапфы в слое масла создается давление, необходимое для отделения цапфы от вкладыша — цапфа как бы всплывает на тонком слое масла. Центр цапфы смещается от начального положения. Давление в слое масла поддерживается насосным действием вращающейся цапфы. [c.84]
Под самоустановкой понимают следование оси опоры за осью вала. В опорных подшипниках скольжения этого добиваются двумя путями 1) выполнением опорной поверхности вкладыша сферической формы или в виде узкого цилиндрического пояска 2) установкой подшипника на эластичной опоре или выполнением его с упругим корпусом. [c.342]
Контроль в отверстии кольца 446 Опорные подшипники скольжения — см. [c.1080]
Аналогичный Т-образный профиль имеет и второй червячный сектор 7, скользящий в направляющих корпуса 24 и прижимаемый дугообразными планками 23. Поворот червячного сектора ( Дфг,) осуществляется посредством червяка 15 при помощи ручки 17. Этот второй червяк также имеет опорные подшипники скольжения и возможность выборки люфта при помощи шарикового подпятника 8. [c.133]
Технические данные питательных, конденсатных, циркуляционных и масляных насосов приведены в разд. 1. Центрирование, монтаж опорных подшипников скольжения и качения, сальниковых уплотнений, уравновешивание роторов приведено в разд. 6 т. 1 Справочника. [c.396]
Насос НШ-32Э показан на рис. 52. Ведущая и ведомая шестерни 8 и 9 изготовлены заодно с валами. Шестерни заключены в алюминиевый корпус 7, который закрывают крышкой 5, прикрепляемой болтами 10. Плавающие втулки 6 являются опорными подшипниками скольжения для валов и одновременно выполняют роль упорных подшипников для торцов шестерен 8 я 9. Положение одной втулки относительно другой фиксируют лысками и проволокой. [c.75]
Опорные подшипники скольжения. В современных турбокомпрессорах с опорами скользящего трения используются следующие конструкции цилиндрических подшипников [c.111]
Ротор турбины покоится на опорных подшипниках скольжения б и 7, к которым подается обильная смазка под давлением для предохранения их от недопустимого нагрева горячими патрубками турбины. С ротором турбины посредством жесткой муфты 8 соединяется ротор компрессора 10, что позволяет компенсировать осевые усилия, возникающие в турбине и компрессоре, направляя потоки воздуха и газа навстречу друг другу.. Неуравновешенное осевое усилие воспринимается упорным подшипником 16, расположенным на выходе вала из компрессора. [c.486]
Сущность этого процесса заключается в кратковременном нагреве поверхностного слоя на глубину 1—3 мм металла, который подвергается закалке. Остальная часть металла не нагревается, что исключает деформацию шпинделя. Нагрев и охлаждение закаливаемых поверхностей происходят при помощи специальных индукторов. Обычно подвергаются закалке поверхности наружного конуса под патрон и конического отверстия в переднем конце. Опорные шейки закаливаются при применении подшипников скольжения. [c.370]
Посадки со значительными гарантированными зазорами fJ/e, E/h имеют зазоры примерно в 2 раза большие, чем у посадок H/f. Они обеспечивают свободное вращение при повышенных режимах работы (значительная нагрузка, высокие скорости вращения). Эти посадки применяют для подшипников скольжения разнесенных опор, много-опорных валов или валов большой длины, для неподвижных регулируемых соединений невысокой точности с большими зазорами. [c.198]
Подшипники скольжения имеют цилиндрическую, коническую или сферическую форму опорной поверхности и работают в условиях сухого или жидкостного трения. Простейшим подшипником скольжения является отверстие, просверленное в корпусе механизма. Часто в это отверстие вставляют вкладыш (втулку) из другого материала. Подшипниковый материал должен обладать малым коэффициентом трения, иметь малый износ трущихся поверхностей и выдерживать необходимые ударные нагрузки. [c.115]
Трение в подшипниках скольжения. Потери на трение оцениваются коэффициентом трения [. На рис. 3.141 показана диаграмма изменения [ в зависимости от характеристики режима работы подшипника ро)/р, где р—динамическая вязкость смазки ш — угловая скорость вала р — среднее давление на опорную поверхность. Диаграмма имеет три характерных участка. Участок /о — 1 характеризуется примерно пос- [c.408]
По принципу работы различают подшипники скольжения, в которых цапфа вала скользит по опорной поверхности, и подшипники качения, в которых между поверхностью вращающейся детали и опорной поверхностью расположены тела качения. [c.220]
На рис. 8.5.2 представлен шип вала (опорная часть вала), который покоится на подшипнике скольжения. [c.110]
Насосы типа МВ (рис. 9.33) — центробежные, вертикальные, секционные, погружного типа. Базовой деталью насоса является составной цилиндр 6 с опорной плитой. К нижнему фланцу цилиндра крепится насос. Подво.п, 2 насоса выполнен в виде осевого конфузорного патрубка с направляющими лопатками, а отвод 1 — в виде колеса. Секции насоса 3 с направляющими аппаратами соединяются между собой стяжными болтами. Уплотнение стыков секций осуществляется металлическим контактом уплотнительных поясков. Ротор 4 насоса — трехопорный. Нижняя и средняя опоры выполнены в виде подшипников скольжения. В качестве верхней опоры предусмотрен сдвоенный радиально — упорный шарикоподшипник 7, который фиксирует положение ротора по отношению к статору и воспринимает остаточные осевые усилия и вес ротора. Подшипники смазываются перекачиваемой жидкостью, нижний и средний — за счет перетекания смазки. К верхнему подшипнику масло подводится от напорного патрубка. [c.285]
Расчет пластмассовых опорных подшипников скольжения по Платонову [6]. Под действием нагрузки Р напряжения в подшипнике распределяются неравномерно (рис. 110) напряжение колеблется в пределах от нуля до максимального значения (Jniax- Величина СТ, ах значительно выше среднего условного удельного давления р ,,, которое конструктор обычно учитывает [6. Значение Рср определяют из уравнения (152). [c.225]
Подшипники из текстолитов [2, 7, 8, 10, 12, 14, 15, 20]. Текстолитовые опорные подшипники скольжения в виде монолитных втулок и сегментных конструкций с продольными и поперечными сегментами обычно применяют в тяжелонагруженных узлах трения машин и механизмов, например, в узлах экскаваторов, прокатных станов, тяговых двигателей и т. п. Втулки изготовляют навивкой и прессованием заготовок с последующей их окончательной механической обработкой или вытачивают из полуфабрикатов, имеющих вид труб, прутков или плит. Наилучшими антифрикционкыми свойстваг 5и обладают втулки из витых и прессованных трубок. Втулки из плит имеют несколько худшие антифрикционные свойства и поэтому их применяют реже, преимущественно при изготовлении небольшого количества подшипников в индивидуальном и несерийном производстве. [c.232]
Ротор турбокомпрессора спроектирован из отдельных дисков, несущих лопатки компрессора и ГТ. Центрирование дисков между собой и передней и задней концевыми частями осуществляется по хиртовым поясам. Общая жесткость ротора обеспечена центральной стяжкой. Ротор турбогруппы опирается на два опорных подшипника скольжения с антифрикционным покрытием. [c.228]
Коэффициент трення качения валков по горячекатаному стальному листу составляет / 0,8 из цветного металла / 0,Зн-0,4, Коэффициент трення скольжения для листа из горячекатаной стали Лс 0,2, для холоднокатаного листа Не 0,12 л = = 0,05 0,08 — коэффициент трения в обычных опорных подшипниках скольжения с бронзовыми вкладышами (по данным Е, Н. Мошннна). [c.103]
Подобные системы смазывания универсальны и пригодны для подачи различных смазочных материалов, в том числе и пластичных. Несмотря на повышенную стоимость и сложность монтажа, эти системы находят широкое распространение, причем даже для смазывания опорных подшипников скольжения КГШП. [c.181]
Опорные подшипники скольжения выполняются с неподвижными опорными поверхностями и с подвижными опорными сегментами. К первому типу относятся одноклиновые (по-другому — цилиндрические, половинные ), двухклиновые (по-другому — эллиптические, лимонные ). Подшипники с большим числом неподвижных поверхностей опирания в отечественном турбиностроении не применяются. [c.298]
Опора барабана на катки (ролики) обеспечивает свободный доступ внутрь мельийцы и позволяет оперативно изменять параметры разгрузочных устройств. Этйм же преимуществом обладают и мельницы с расположением опорных подшипников скольжения на барабане мельницы. [c.210]
Описание конструкций. На рис. 13.1. изображен подшипник скольжения, который состоит из корпуса 1, крышки 2, нижнего 3 и верхнего 4 вкладышей и стяжных болтов 5 с гайками 7. Масло для смазки поступает из масленки (на чертеже ие потазана) через отверстие в патрубке, имеющемся в верхнем вкладыше, растекается по канавкаМ, обргвованным на опорной поверхностн вкладыша. [c.354]
Валы и оси вращаются в опорах, в качестве которых служат подшипники качения или скольжения. Опорные части вало и шщ назВшают цапфами, 2при этом концевые цапфы для подшипников скольжения называют шипами, а промежуточные — шейками [c.418]
Существует очень много конструкций подшипников скольжения, которые подразделяются на два вида неразъемные и разъемные. Неразъемный подшипник (рис. 13.1) состоит из корпуса и втулки, которая может быть неподвижно закреплена в корпусе подшипника или свободно заложена в него ( плавающая втулка ). Неразъемные подшипники используют главным образом, в тихоходных машинах, приборах и т. д. Их основное преимущество — простота конструкции и низкая стоимость. Если корпус подшипника выполнен в виде фланца с опорной плоскос1ью, нормальной к оси вала, то такой подшипник называют фланцевым. [c.221]
Ведомый (турбинный) ротор гидромуфты (рис. 9.10) образован валом 1 с насаженным на него двусторонним турбинным диском 2, лопастная система которого выполнена аналогично насосным дискам. На передний конец ведомого вала насажены внутренняя обойма роликового подшипника 5 и уплотнительная втулка 4. С другой стороны вал имеет шейку 5 опорно-упорного подшипника скольжения и втулку зубчатой муфты 6 для соединения его с валом редуктора. Приведенная схема регулирования работы гидромуфты носит название жиклерной. [c.236]
Подшипники скольжения и их смазка
Подшипники скольжения или скольжения состоят из вала или шейки, которые свободно вращаются в опорной металлической втулке или кожухе. В этих подшипниках нет тел качения. Их конструкция и конструкция могут быть относительно простыми, но теория и работа этих подшипников могут быть сложными.
В этой статье рассматриваются подшипники скольжения с жидкостной пленкой, смазываемые маслом и консистентной смазкой; но сначала краткое описание пальцев и втулок, сухих и полусмазываемых опорных подшипников и подшипников качения.
Тихоходные пальцы и втулки представляют собой форму опорных подшипников, в которых вал или вкладыш, как правило, не совершают полного вращения. Частичное вращение на низкой скорости перед типичным изменением направления на противоположное не позволяет сформировать полную пленку жидкости, и, таким образом, контакт металл-металл действительно происходит внутри подшипника. Пальцы и втулки постоянно работают в режиме граничной смазки.
Эти типы подшипников обычно смазываются противозадирной (ЕР) смазкой, которая помогает выдерживать нагрузку.Твердый дисульфид молибдена (молибден) включен в консистентную смазку для повышения несущей способности смазки.
Во многих приложениях для наружного строительства и горнодобывающего оборудования используются пальцы и втулки. Следовательно, ударные нагрузки и загрязнение водой и грязью часто являются основными факторами их смазки.
Рис. 1. Kingsbury Radial
и упорный подшипник
Сухие опорные подшипники состоят из вала, вращающегося в сухой втулке, обычно из полимера, который может быть смешан с твердыми частицами, такими как молибден, графит, ПТФЭ или нейлон.
Эти подшипники предназначены только для приложений с низкой нагрузкой и низкой поверхностной скоростью. Полусмазываемые опорные подшипники состоят из вала, вращающегося в пористой металлической втулке из спеченной бронзы или алюминия, в которой смазочное масло содержится в порах пористого металла. Эти подшипники рассчитаны на низкие нагрузки, скорость от низкой до средней и температуру до 100 ° C (210 ° F).
Подшипники с поворотными подушками или поворотными башмаками состоят из вала, вращающегося внутри корпуса, состоящего из изогнутых подушек.Каждая колодка может поворачиваться независимо и совпадать с кривизной вала. Схема подшипника с наклонной подушкой представлена на рисунке 1.
Преимущество этой конструкции заключается в более точном совмещении опорной оболочки с вращающимся валом и повышении устойчивости вала. 1
Подшипники скольжения включают подшипники скольжения, скольжения, вкладыши и баббитовые подшипники. Термин баббит на самом деле относится к слоям более мягких металлов (свинец, олово и медь), которые образуют металлическую контактную поверхность вкладыша подшипника.Эти более мягкие металлы накладываются на более прочную стальную опорную оболочку и необходимы для защиты оболочки от более твердого вращающегося вала.
Простые опорные подшипники скольжения воспринимают только радиальную нагрузку, перпендикулярную валу, как правило, из-за веса или нагрузки вала, направленной вниз. Осевые или осевые нагрузки вдоль оси вала также могут восприниматься опорными подшипниками, предназначенными для этой цели. На рис. 1 показан подшипник с наклонной подушкой, способный воспринимать как радиальные, так и осевые нагрузки.
Рис. 2. Слои конструкции подшипников скольжения
Подшипники скольжения работают в граничном режиме (контакт металл-металл) только во время пуска и останова оборудования, когда частота вращения вала (шейки) недостаточна для создания масляной пленки. Именно во время пуска и останова происходит почти полное повреждение подшипника. 2
Гидростатическая подъемная сила, создаваемая подачей масла под внешним давлением, может использоваться для смещения больших тяжелых цапф перед запуском (вращение вала) для предотвращения такого типа повреждений.Во время нормальной работы вал вращается с достаточной скоростью, чтобы протолкнуть масло между соответствующими изогнутыми поверхностями вала и кожуха, тем самым создавая масляный клин и гидродинамическую масляную пленку.
Эта полностью гидродинамическая пленка жидкости позволяет этим подшипникам выдерживать чрезвычайно тяжелые нагрузки и работать с высокими частотами вращения. Обычные скорости на поверхности от 175 до 250 метров в секунду (от 30 000 до 50 000 футов в минуту). Температуры часто ограничиваются используемым смазочным материалом, поскольку свинцово-оловянный баббит может достигать температуры 150 ° C (300 ° F).
Важно понимать, что вращающийся вал не центрируется в вкладыше подшипника при нормальной работе. Это расстояние смещения называется эксцентриситетом подшипника и создает уникальное место для минимальной толщины масляной пленки, как показано на Рисунке 3.
Рисунок 3. Движение вала при запуске
Обычно минимальная толщина масляной пленки также является динамическим рабочим зазором подшипника. Знание толщины масляной пленки или динамических зазоров также полезно при определении требований к фильтрации и чистоте поверхности металла.
Обычно минимальная толщина масляной пленки в зоне нагрузки во время работы составляет от 1,0 до 300 микрон, но значения от 5 до 75 микрон чаще встречаются в промышленном оборудовании среднего размера. Толщина пленки будет больше в оборудовании с валом большего диаметра.
Лица, которым требуется более точное значение, должны искать информацию о числе Зоммерфельда и числе Рейнольдса. Более подробное обсуждение этих расчетов выходит за рамки данной статьи.Обратите внимание, что эти значения значительно превышают значения в один микрон, встречающиеся в подшипниках качения.
Давления в зоне контакта опорных подшипников значительно ниже, чем в подшипниках качения. Это происходит из-за большей площади контакта, создаваемой соответствующими (схожей кривизной) поверхностями шейки и гильзы.
Среднее давление в зоне нагрузки опорного подшипника определяется силой на единицу площади или, в данном случае, весом или нагрузкой, поддерживаемой подшипником, деленными на приблизительную площадь нагрузки подшипника (диаметр подшипника, умноженный на длину опоры). несущий).В большинстве промышленных приложений эти значения находятся в диапазоне от 690 до 2070 кПа (от 100 до 300 фунтов на квадратный дюйм).
При таком низком давлении вязкость масла в зоне контакта подшипника практически не увеличивается из-за давления. Подшипники автомобильных поршневых двигателей и некоторые сильно нагруженные промышленные применения могут иметь среднее давление от 20,7 до 35 МПа (от 3000 до 5000 фунтов на квадратный дюйм). При таких уровнях давления вязкость может немного увеличиться. Максимальное давление, с которым сталкивается подшипник, обычно примерно вдвое превышает среднее значение, вплоть до максимального примерно 70 МПа (10 000 фунтов на квадратный дюйм).
Масляный вихрь – это явление, которое может возникать в высокоскоростных подшипниках скольжения, когда положение вала внутри корпуса становится нестабильным, и вал продолжает менять свое положение во время нормальной работы из-за сил жидкости, создаваемых внутри подшипника. Масляный завихрение можно уменьшить, увеличив нагрузку или изменив вязкость, температуру или давление масла в подшипнике.
Постоянное решение может включать новый подшипник с другим зазором или другой конструкцией. Масляный выброс возникает, когда частота масляного вихря совпадает с собственной частотой системы.Результатом может стать катастрофический отказ. 3
Смазка маслом
Масла используются в опорных подшипниках, когда требуется охлаждение или когда необходимо смыть загрязнения или мусор с подшипника. Высокоскоростные опорные подшипники всегда смазываются маслом, а не консистентной смазкой. Масло подается в подшипник либо системой масляного насоса под давлением, либо масляным кольцом, либо манжетой, либо фитилем. Канавки вкладыша подшипника используются для распределения масла по поверхностям подшипников.
Требуемый класс вязкости зависит от частоты вращения подшипника, температуры масла и нагрузки. Скорость подшипника часто измеряется строго по оборотам вала в минуту, без учета поверхностной скорости вала, согласно значениям «nd m », рассчитанным для подшипников качения. В таблице 1 приведены общие рекомендации по выбору правильного класса вязкости по ISO.
Указанный номер класса ISO является предпочтительным для диапазона скорости и температуры.Масла классов ISO 68 и 100 обычно используются в помещениях с подогревом, а масла класса 32 используются для высокоскоростных (10000 об / мин) агрегатов и некоторых наружных низкотемпературных применений.
Обратите внимание на таблицу, что чем выше частота вращения подшипника, тем ниже требуемая вязкость масла; и чем выше рабочая температура агрегата, тем выше требуемая вязкость масла. Если возможна вибрация или незначительная ударная нагрузка, следует рассмотреть более высокий сорт масла, чем тот, который указан в Таблице 1.
Скорость подшипника | Температура подшипника / масла (° C) | |||
(об / мин) | От 0 до 50 | 60 | 75 | 90 |
От 300 до 1500 | – | 68 | От 100 до 150 | – |
~ 1,800 | 32 | 32 по 46 | 68 к 100 | 100 |
~ 3,600 | 32 | 32 | 46 по 68 | 68 к 100 |
~ 10 000 | 32 | 32 | 32 | 32 по 46 |
Таблица 1.Выбор класса вязкости опорного подшипника ISO
Другой метод определения надлежащей степени вязкости – применение критериев минимальной и оптимальной вязкости к графику зависимости вязкости от температуры. Общепринятая минимальная вязкость масла при рабочей температуре для подшипников скольжения составляет 13 сСт, хотя в некоторых конструкциях допускается использование масла толщиной от 7 до 8 сСт при рабочей температуре.
Оптимальная вязкость при рабочей температуре составляет от 22 до 35 сСт для подшипников с умеренной скоростью вращения, если не происходит ударных нагрузок.Оптимальная вязкость может достигать 95 сСт для низкоскоростных, сильно нагруженных или ударных подшипников скольжения.
Использование этого метода требует определенных знаний о температуре масла в подшипнике в рабочих условиях, которую бывает сложно определить. К счастью, точная температура масла не требуется для большинства определений вязкости. Обычно определяют температуру внешней поверхности труб, по которым масло идет к подшипнику и от него.
Температура масла внутри труб обычно выше (от 5 до 10 ° C, от 10 до 18 ° F), чем на внешней металлической поверхности трубы.Температуру масла внутри подшипника можно принять как среднее значение температуры масла на входе и температуры на выходе из подшипника. 4
Третий, более сложный метод – это расчет вязкости масла, необходимой для получения удовлетворительной толщины масляной пленки. Лица, желающие узнать больше об этом методе, должны искать информацию относительно уравнения Зоммерфельда и либо коэффициентов эксцентриситета, либо чисел Рейнольдса. 4
Если выбранное масло имеет слишком низкую вязкость, из-за недостаточной толщины пленки будет выделяться тепло, и произойдет некоторый контакт металла с металлом.Если масло имеет слишком высокую вязкость, снова будет выделяться тепло, но из-за внутреннего жидкостного трения, создаваемого внутри масла. Выбор масла слишком высокой вязкости также может увеличить вероятность кавитации.
Зоны высокого и низкого давления, которые создаются в масле с каждой стороны зоны минимальной толщины пленки, могут вызвать кавитацию масла в этих подшипниках. Кавитация – это результат расширения растворенного воздуха или пара (воды или топлива) в зоне низкого давления подшипника.
Образовавшийся пузырь лопается, вызывая повреждение, поскольку он проходит через часть подшипника, находящуюся под высоким давлением. Если схлопывание или схлопывание пузырька пара происходит рядом с поверхностью металла, это может вызвать кавитационное точечное повреждение металла. Если взрыв пузыря происходит внутри масла, может возникнуть микрогорячее пятно или микродизель, что может привести к покрытию лаком внутри системы.
Обычно в маслах, используемых в этих областях, используется система присадок, ингибирующих ржавчину и окисление (R&O).Также могут присутствовать антипенные добавки и присадки, понижающие температуру застывания. Противоизносные (AW) гидравлические масла также могут использоваться, если не превышен предел высокой температуры цинкового компонента AW и не присутствует избыточное количество воды.
Масла R&O, как правило, обладают лучшими характеристиками водоотделения, что является преимуществом, а свойства AW гидравлического масла будут полезны только во время пуска и останова, если предполагается, что подшипник работает правильно.
Консистентная смазка
Консистентная смазка используется для смазки опорных подшипников, когда охлаждение подшипника не имеет значения, как правило, если подшипник работает на относительно низких скоростях.Смазка также полезна, если возникает ударная нагрузка или если подшипник часто запускается и останавливается или меняет направление.
Консистентная смазка почти всегда используется для смазки пальцев и втулок, поскольку она обеспечивает более густую смазку, чем масло, для выдерживания статических нагрузок и защиты от вибрации и ударных нагрузок, которые являются обычными для многих из этих применений.
Литиевое мыло или загустители на основе литиевого комплекса являются наиболее распространенными загустителями, используемыми в консистентных смазках, и отлично подходят для большинства применений в подшипниках скольжения.Используемая консистентная смазка обычно относится к классу № 2 по NLGI с вязкостью базового масла приблизительно от 150 до 220 сСт при 40 ° C.
В консистентных смазках для низкоскоростных, высоконагруженных и высоких температур, а также для пальцев и втулок может использоваться базовое масло с более высокой вязкостью, и в их состав входят противозадирные и твердые присадки. Консистентные смазки для повышения водостойкости могут быть изготовлены на основе более тяжелых базовых масел, различных загустителей и специальных составов присадок.
Консистентные смазки для лучшего нанесения при низких температурах могут включать базовое масло с более низкой вязкостью, произведенное в соответствии со спецификацией NLGI # 1.Подшипники, смазываемые централизованной системой подачи консистентной смазки, обычно используют консистентную смазку №1, 0 или 00.
Кажущаяся вязкость консистентной смазки изменяется в зависимости от сдвига (давления, нагрузки и скорости), то есть консистентные смазки являются неньютоновскими или тиксотропными. Внутри вращающегося опорного подшипника, поскольку подшипник вращается быстрее (увеличивается скорость сдвига), кажущаяся вязкость консистентной смазки уменьшается и приближается к вязкости базового масла, используемого в консистентной смазке.
На обоих концах вкладыша подшипника давление ниже, поэтому кажущаяся вязкость остается выше.Образовавшаяся более густая смазка на концах подшипников действует как встроенное уплотнение, уменьшая проникновение загрязняющих веществ.
Процедуры смазки
Процедуры смазки подшипников скольжения, пальцев и втулок не так четко определены или критичны, как для подшипников качения, поскольку смазка не подвергается взбалтыванию, создаваемому телами качения.
Объем впрыскиваемой смазки и частота нанесения больше зависят от метода проб и ошибок.Как правило, большинство опорных подшипников нельзя чрезмерно смазывать. Следует соблюдать осторожность при нагнетании консистентной смазки в подшипник с уплотнениями, чтобы они не были повреждены или смещены под действием силы и объема поступающей смазки.
Суровые условия окружающей среды, ударные нагрузки и особенно рабочая температура будут основными факторами при определении частоты повторного смазывания.
Подшипники скольжения обычно имеют более простую конструкцию и их не так сложно смазывать, как подшипники качения.Правильная вязкость, соответствующая условиям эксплуатации, и чистая и сухая смазка, как правило, достаточны для образования полностью жидкой смазочной пленки и обеспечения длительного срока службы подшипников.
Список литературы
Стрекер, Уильям. «Поиск и устранение неисправностей в упорных подшипниках качения». Machinery Lubrication, журнал , март-апрель 2004 г.
Стрекер, Уильям. «Анализ отказов подшипников скольжения.» Machinery Lubrication, журнал , июль-август 2004 г.
Берри, Джеймс. «Неустойчивость масляного вихря и хлыста в подшипниках скольжения». Machinery Lubrication, журнал , май-июнь 2005 г.
Справочник по трибологии . Глава 61, Конструкция и анализ подшипников скольжения. Хонсари, М. CRC Press, 1997.
Примечание редактора:
Части этой статьи были ранее опубликованы в разделе «Общество трибологов и инженеров-смазчиков» (STLE), Альберта, , Базовый справочник по смазке , второе издание, 2003 г.
Смазка подшипников скольжения
Подшипники скольжения
Сегодня в машиностроении используются два основных типа подшипников: подшипники скольжения и подшипники качения. В этой статье рассматриваются особые требования к смазке подшипников скольжения, также известных как подшипники скольжения и опорные подшипники.
Подшипник скольжения состоит из вала, также называемого цапфой, и опорного компонента, который может представлять собой оболочку вокруг вала, называемую втулкой, половину корпуса, в которую входит вал, две половинки вкладыша (верхняя и нижняя части) или составная оболочка.
Подшипники скольжения используются для высоких радиальных нагрузок (перпендикулярных оси вала) и от низких до высоких скоростей. Типичные области применения включают турбины, большие фрезерные системы, кривошипы двигателей, компрессоры, коробки передач, опоры подшипников вала и т. Д.
Каждый подшипник скольжения имеет некоторые общие конструктивные характеристики, как показано на Рисунке 2.
Компоненты, которые разделены масляной пленкой в подшипнике скольжения, – это вкладыш подшипника и вал.Вал изготовлен из высококачественной, износостойкой, конструктивно прочной стали. Вкладыш подшипника может быть однослойным или многослойным, в зависимости от конструктивных особенностей оборудования (рисунок 3).
Режим смазки
В нормальных условиях эксплуатации режим смазки будет гидродинамической жидкой пленкой. Гидродинамическая пленка возникает, когда между смазываемыми поверхностями в точке нагружения имеется достаточно смазки для образования жидкого клина, разделяющего поверхности скольжения.В этом состоянии смазанные компоненты не соприкасаются друг с другом, что снижает трение и износ.
Это состояние представлено уравнением ZN / P, где Z = вязкость, N = скорость (об / мин) и P = нагрузка. Это уравнение представлено на рисунке 4. Кривая на этом графике называется кривой Штрибека. Это классическое представление о соотношении скорости, нагрузки и трения.
Условия смешанной пленки возникают, когда очевидна потеря пленки, приводящая к мгновенному контакту между двумя поверхностями.Это может происходить в ответ на мгновенные изменения нагрузки, называемые ударной нагрузкой, которые могут разрушить пленку, что приведет к физическому контакту противоположных выступов.
Еще одно условие, которое может произойти, – это смазка граничной пленкой. Это когда пленка, разделяющая поверхности, претерпевает значительные потери, что приводит к большой нагрузке на контакт металла с металлом. Это происходит каждый раз, когда относительное движение поверхностей компонентов происходит медленно и масляная пленка не образуется.
Смазка подшипника скольжения
Подшипник скольжения, работающий при надлежащей скорости, площади поверхности, вязкости и объеме масла, может выдерживать очень большие нагрузки.Баланс между этими условиями важен. При изменении нагрузки или скорости необходимо отрегулировать вязкость смазочного материала, чтобы компенсировать это изменение. Не существует простой формулы, которая использовалась бы для расчета требований к вязкости для подшипников скольжения с масляной смазкой, но формула ZN / P демонстрирует результаты сложных расчетов, используемых для определения надлежащего зазора.
Критерии, которые следует учитывать после определения надлежащего класса вязкости, включают стойкость к окислению, ингибирование коррозии, защиту от износа, свойства разделения воды и воздуха и т. Д.Поскольку подшипники скольжения могут использоваться в самых разных областях, единого набора критериев, который следует использовать, не существует. Выбор зависит от конструкции оборудования и условий эксплуатации.
Подшипники скольжения обычно смазываются маслом, но могут смазываться консистентной смазкой для тихоходного оборудования, особенно если они подвержены частым запускам и остановкам или если до подшипников физически трудно добраться.
Тип и количество смазки зависят от постоянного пополнения массы смазки, которая удерживается в пределах динамических зазоров (пустые пространства во время вращения подшипника), чтобы поддерживать эффективное состояние смазки и гидродинамический подъем.Для оборудования с плохими уплотняющими характеристиками может потребоваться более тяжелый смазочный материал и более частые циклы пополнения.
При ручном (периодическом) повторном смазывании объем и частота зависят от условий эксплуатации, качества смазки и времени, доступного для выполнения задачи. Выбор пластичной смазки начинается с рассмотрения используемого масла. Тяжелые масла используются для создания консистентных смазок, используемых для ручной смазки подшипников скольжения в тяжелых условиях эксплуатации.
После выбора масла с подходящей вязкостью учитываются мыльный загуститель, характеристики окисления и ржавчины, свойства консистенции после обработки, прокачиваемость (для автоматических систем) и свойства несущей способности (EP / AW).Для длительных интервалов и очень больших нагрузок могут быть добавлены твердые добавки, такие как дисульфид молибдена или графит. Твердые добавки служат для механического предотвращения контакта металла в условиях смешанной пленочной и граничной смазки.
Смазку следует закачивать в подшипник перед зоной нагрузки и в местах канавок для смазки, используемых для распределения смазки (рисунки 5 и 6).
Рисунок 6 |
Виды износа и отказов подшипников скольжения
Есть несколько факторов, которые могут стереть или повредить поверхность подшипника скольжения.Абразивный износ – один из самых распространенных. Если износ вызван трением твердых частиц между смазываемыми поверхностями, это называется трехкомпонентным износом. Износ, вызванный неровностями на одной поверхности, режущей другую поверхность, называется двухкомпонентным истиранием.
Износ также может быть результатом недостаточного объема смазки (голодание, ведущее к граничным условиям), перегретой смазки (вязкость при рабочей температуре не может выдержать нагрузку, вызывая нагревание при трении и дополнительное разжижение масла), шероховатых поверхностей (неровности на шейке вызывают трение), дисбаланса ( неправильная нагрузка опорного элемента, вызывающая ударную нагрузку), эксцентриситет шейки (яйцевидная шейка вызывает трение о выступах) и усталость металла из-за неправильной металлургии.Износ подшипников скольжения можно эффективно контролировать с помощью масла и феррографического анализа.
Контрольные индикаторы, которые могут указывать на условия высокого износа, включают большое количество металлических частиц (на два уровня выше нормы), потемневшие металлические поверхности, вороненые металлические поверхности и металлы износа, сформированные в виде спиралей или пластинок. По мере того, как масла стареют и загрязняются влагой или кислотными окислительными соединениями, мы можем видеть признаки коррозии и окисления металлов на неподвижных поверхностях коллектора.
Подшипники скольжения – обзор
2.1 Введение
Назначение подшипника – выдерживать нагрузку, обычно прикладываемую к валу, при этом обеспечивая относительное движение между двумя элементами машины. Два основных класса подшипников – это опорные подшипники, также известные как подшипники скольжения или скольжения, и подшипники качения, иногда также называемые шарикоподшипниками.Цели данной главы – описать диапазон технологий подшипников, обозначить, какой тип подшипников использовать для конкретного применения, а также познакомить с конструкцией опорных подшипников с особым вниманием к подшипникам с граничной смазкой и полнопленочным гидродинамическим подшипникам. Выбор и использование подшипников качения рассматривается в главе 3.
Термин «подшипник» обычно относится к контактирующим поверхностям, через которые передается нагрузка. Подшипники могут катиться, скользить или делать то и другое одновременно.Диапазон доступных типов подшипников обширен, хотя их можно в общих чертах разделить на две категории: подшипники скольжения, также известные как подшипники скольжения или скольжения, движение в которых облегчается тонким слоем или пленкой смазочного материала, и подшипники качения, где движению способствует комбинация качения и смазки. Смазка подшипника часто требуется для уменьшения трения между поверхностями и отвода тепла. На рис. 2.1 показаны два наиболее известных подшипника: опорный подшипник и радиальный шарикоподшипник.Общая классификационная схема для различения типов подшипников представлена на рис. 2.2, основанная на таксономии, первоначально разработанной Hindhede et al. (1983).
Рисунок 2.1. Опорный подшипник и радиальный шарикоподшипник.
Рисунок 2.2. Классификация подшипников.
Как видно из рис. 2.2, выбор подшипников широк. Для конкретного применения можно использовать подшипники разных типов. В небольшом газотурбинном двигателе, вращающемся, скажем, со скоростью 50 000 об / мин, можно использовать либо подшипники качения, либо опорные подшипники, хотя оптимальный выбор будет зависеть от ряда факторов, таких как срок службы, стоимость и размер.Рис. 2.3 может быть использован для указания того, какой тип подшипника имеет максимальную нагрузочную способность при данной скорости и размере вала, а в таблице 2.1 приведены характеристики различных типов подшипников для некоторых критериев, кроме грузоподъемности.
Рисунок 2.3. Выбор типа подшипника по грузоподъемности и скорости.
Предоставлено Neale, M.J. (ed.). (1995). Справочник по трибологии . Баттерворт Хайнеманн.Таблица 2.1. Сравнение характеристик подшипников при непрерывном вращении.
Тип подшипника | Точное радиальное расположение | Совместная осевая и радиальная нагрузка | Низкий пусковой крутящий момент | Бесшумный ход | Доступны стандартные детали | Простота смазки |
---|---|---|---|---|---|---|
Плохо | В большинстве случаев | Плохо | Удовлетворительно | Некоторое | Отлично | |
Пористые металлические подшипники скольжения с пропиткой маслом | Хорошо | Немного | Хорошо | Отлично | Да | Отлично |
Гидродинамические подшипники с жидкостной пленкой | Удовлетворительно | No.Требуется отдельный упорный подшипник | Хорошо | Отлично | Некоторое | Обычно требуется система рециркуляции |
Гидростатические подшипники | Отлично | Нет. Требуется отдельный упорный подшипник | Отлично | Отлично | Нет | Плохое специальное система необходима |
Подшипники качения | Хорошо | Да, в большинстве случаев | Очень хорошо | Обычно удовлетворительно | Да | Хорошо при консистентной смазке |
С любезного разрешения Neale, M.Дж. (Ред.). (1995). Справочник по трибологии . Баттерворт Хайнеманн.
В этой и следующей главах представлены общие сведения о подшипниках. Подшипники скольжения с масляной пленкой представлены в разделе 2.2, конструкция подшипников с граничной смазкой, которые обычно используются для низкоскоростных приложений, рассмотрена в разделе 2.3, конструкция подшипников с полной гидродинамической смазкой описана в разделе 2.4 и главе 3. Компания «Подшипники качения» рассматривает подшипники качения.Для дальнейшего чтения тексты Khonsari and Booser (2017), Harris (2001) и Brandlein et al. (1999) дают обширный обзор подшипниковых технологий.
Указатели производительности: подшипники скольжения – Часть 1 – Совет недели – Lube Talk
Многие операторы знакомы с роликовыми подшипниками или подшипниками качения, поскольку они используются в повседневной жизни. Подшипники качения, от роликовых коньков до подшипников автомобильных колес, делают повседневную жизнь возможной.
Но что вы знаете о подшипниках скольжения (или опорных подшипниках)?
Они отличаются тем, что уменьшают трение и опорные нагрузки, как и антифрикционные подшипники, но работают только с движением скольжения.В этой серии наконечников, состоящей из двух частей, объясняются принципы работы подшипников скольжения и скольжения, а также их принцип работы, где они используются и как смазываются.
Конструкция подшипника скольжения / скольжения
Простейшие типы подшипников скольжения представляют собой конструкцию «целиком в блоке». Есть верхняя половина и нижняя половина, причем последнюю часто называют «несущей». Часть вала, проходящая через отверстие подшипника, называется «цапфой», и поэтому подшипник скольжения часто называют «подшипником скольжения».”
Конструкция подшипника скольжения или опорного подшипника зависит от механических факторов. К ним относятся:
- Отношение длины подшипника к его диаметру: Длина подшипника зависит от нагрузки. Отношение длины к диаметру обычно составляет от 1,5 до 4.
- Площадь проекции подшипника: Осевая длина подшипника, умноженная на диаметр, составляет площадь. Большая площадь выдерживает большие нагрузки.
- Зазор между подшипником и шейкой: Отверстие подшипника должно быть немного больше, чем шейка, чтобы обеспечить поток смазки, тепловое расширение, прогиб вала и несоосность.
- Материалы подшипников: Материалы подшипников обычно включают в себя цинк, медь, олово и свинец, нанесенные слоями, включая поверхностный слой, более толстый твердый поддерживающий слой и связующий слой оболочки. Слои должны быть устойчивыми к царапинам, достаточно мягкими, чтобы впитывать частицы мусора, и соответствовать неровностям вала и
- Обработка поверхности: Шероховатость поверхности от пика до впадины составляет от 4 до 60 микрометров, в зависимости от требуемой точности.
- Обработка канавок: Для облегчения доставки смазки в зону нагрузки подшипники скольжения часто имеют канавки. Канавки могут быть осевыми, диагональными, окружными и иметь скошенные края, в зависимости от нагрузки и требуемой подачи масла.
Как смазываются подшипники скольжения или скольжения?
Подшипники скольжения смазываются маслом или консистентной смазкой. Однако этот раздел касается типа пленки, которая образуется при смазке маслом, в «гидродинамическом» или «гидростатическом» режиме.
Гидродинамическая смазка: Для обеспечения гидродинамической смазки масло должно иметь правильную вязкость и подаваться в достаточном количестве. Это позволит смазке заполнить зазоры, обеспечивая подъемную силу, необходимую для создания зазора и уменьшения пускового трения. Как только шейка начинает вращаться, образуется масляный клин, стабильность которого зависит от скорости вала, нагрузки и вязкости масла. Увеличение вязкости или скорости увеличивает толщину масляной пленки, а увеличение нагрузки уменьшает масляную пленку.
Гидростатическая смазка: В режиме гидростатической смазки используется система подачи масла, так что масло под давлением доступно для распределения смазки по опорным поверхностям. Давление подаваемого масла помогает выдержать нагрузку. Эта система используется для установления условий равновесия между нагрузкой, маслом и поверхностями подшипников и шейки.
Все подшипники скольжения или скольжения работают в режимах граничной, полной жидкой пленки или граничной или смешанной смазочной пленки, которые обсуждались в других советах недели.
Мы надеемся, что это было полезным введением в подшипники скольжения (опорные). В следующей статье этой серии мы обсудим состав подшипников скольжения и уделим больше времени передовым методам смазывания.
А пока поставьте лайк этой статье, если вы сочли ее полезной, и оставьте комментарий ниже, если у вас есть какие-либо вопросы.
Наука о простоте Самосмазывающиеся подшипники скольжения линейного перемещения
Простота ® подшипники скольжения для линейного перемещения обладают реальными преимуществами по сравнению с другими типами подшипников для линейного перемещения; такие как самосмазывающееся качество гильзы Frelon® подшипника, а также очищающее действие на валу, которое обеспечивает плавное линейное движение.Эти возможности позволяют системе линейного перемещения не только избежать катастрофического отказа, но также продлить срок службы системы.
Что такое самосмазка?
Самосмазка характеризуется способностью подшипника переносить микроскопические количества материала на сопрягаемую поверхность. Этот процесс переноса создает пленку, которая обеспечивает смазку и снижает трение по длине рельса или вала. Самосмазка имеет несколько преимуществ по сравнению с традиционными подшипниками со смазкой.Самосмазывающиеся подшипники экономят время и деньги на профилактическое обслуживание и не требуют опасных отходов смазочного материала, утилизации или очистки. Самосмазка обеспечивает постоянство сил трения в подшипниках и системе привода, и не требуется добавление смазки или масла, которые могут притягивать загрязнения, разрушающие обычные подшипники.
Процесс передачи
Процесс переноса – это постоянная динамическая функция самосмазывающегося подшипника, которая будет продолжаться на протяжении всего срока его службы.
Первым и наиболее важным этапом процесса является период обкатки. Это когда происходит первоначальный перенос материала на сопрягаемую поверхность. Количество материала подшипника, затронутого во время переноса, зависит от множества факторов, включая скорость, нагрузку, длину хода и т. Д. Для приложения. Обычно начальный процесс переноса выполняется за 50-100 ходов непрерывной работы.
На вторичной и продолжающейся фазе переноса самосмазка наиболее эффективна.
Что делает систему самосмазывающейся?
- Смазка является неотъемлемой частью материала подшипника.
- Смазка (обычно масло или консистентная смазка) НЕ добавляется к оригинальной конструкции подшипника.
- Смазка НЕ выйдет из строя и со временем станет неэффективной (старение смазки).
- Смазка равномерно нанесена на поверхность вала.
- Дополнительные компоненты не увеличивают стоимость всей системы.
Чтобы действительно быть самосмазывающейся, подшипниковая система должна выполнять именно то, что подразумевает ее название. Он должен обеспечивать собственную смазку на протяжении всего срока службы системы и не иметь какого-либо внешнего источника, облегчающего смазку в течение определенного периода времени. Он должен быть спроектирован и изготовлен из материала подшипника с самого начала.
Распространенные заблуждения о самосмазке
Умные рекламные уловки и неточные учебные материалы часто заявляют о возможности «самосмазывания» или «смазки на весь срок службы» для систем или компонентов, которые не подходят под определение смазки как неотъемлемого элемента материала подшипника.Хотя эти системы могут быть временно «самосмазывающимися», в конечном итоге смазка будет использована и ее необходимо будет заменить. Многие подшипники с «пожизненной смазкой» на самом деле не смазываются на весь срок службы, их просто «смазывают на долгое время».
Обычные несамосмазывающиеся системы
Системы роликового элемента: Сюда входят поворотные (шариковые и роликовые) подшипники, линейные шарикоподшипники с круговым движением и монорельсовые конструкции с профилем роликового типа. Для работы всех этих систем требуется какая-то внешняя смазка.Контакт металла по металлу тела качения с дорожкой качения требует постоянного присутствия смазки или масла. Если эта внешняя смазка отсутствует, шарик или ролик начнет непосредственно контактировать с материалом вала или рельса, что приведет к истиранию и повреждению бринелингом. Многие производители пытаются преодолеть этот недостаток конструкции, добавляя пропитанные маслом уплотнения на концах подшипника или корпуса. Такой подход может привести к некоторому увеличению срока службы подшипника качения.
Бронза, пропитанная маслом: Подшипники из бронзы очень пористые и имеют легкое масло, пропитанное материалом. В оптимальных условиях это масло всасывается к поверхности подшипника, создавая слой смазки между подшипником и валом.
Бронза с графитовой пробкой: Графит – хорошая твердая смазка, которую обычно добавляют в подшипники из бронзы. В отверстия в основном бронзовом материале обычно вставляются твердые заглушки из графита.
Материалы с тефлоновым покрытием: ПТФЭ можно использовать для покрытия поверхностей подшипников несколькими способами.Может применяться в составе порошка, просто присыпающего подшипник. Это может быть распыленная смесь, которая прилипает к опорной поверхности. Или это может быть часть жидкости или консистентной смазки, нанесенной на подшипник. Любой из этих методов приводит к очень тонкому слою реальной смазки, который быстро изнашивается и становится неэффективным.
Пластмасса, пропитанная маслом: Здесь снова к основному материалу добавляется легкое масло для облегчения смазки подшипников. В результате сначала снижается трение, но старение и рассеяние смазки быстро снижает ее эффективность.
Процесс обкатки
Процесс обкатки и передачи самосмазывающегося линейного подшипника Frelon обеспечивает максимальную эффективность работы. Чтобы правильно интегрировать подшипник в систему линейного перемещения, вал линейного перемещения необходимо очистить маслом типа 3-в-1®, чтобы обеспечить чистую передачу материала. Затем подшипник должен пройти несколько циклов по валу, чтобы фрелон нанес на вал микроскопическую пленку, заполнив впадины в отделке поверхности и создав условия работы фрелона на фрелоне, которые действительно являются самосмазывающимися.
В определенных ситуациях подшипник скольжения может нуждаться в дополнительной смазке. Для подшипников PBC Linear’s Simplicity рекомендуются следующие смазочные материалы:
- Масла Waylube
- Легкие масла на нефтяной основе
- Масла типа 3-в-1
- Легкие консистентные смазки на нефтяной основе
Некоторые смазочные материалы, которых следует избегать при использовании подшипников Simplicity, включают:
- WD-40®
- Распылители из ПТФЭ
- Масла, смазки или спреи, содержащие фторуглероды или силикон
- Масла моторные / масла с присадками
Подшипники Simplicity могут быть сконфигурированы с дополнительной системой смазки, механически обработанной для дополнительной смазки.Войлочный фитиль врезан во внутренний диаметр подшипника, который предназначен только для использования с маслами – при использовании консистентной смазки удалите войлочный фитиль, чтобы создать резервуар для консистентной смазки. Установленные в корпусе агрегаты имеют крепление в стене, позволяющее подавать смазку к фетровому фитилю на внутренней стороне подшипника.
Найдите свое идеальное решение для линейного перемещения:
(PDF) Исследование опорного подшипника с консистентной смазкой и частичной текстурой поверхности
соответственно.Но нагрузка одновременно снижается на 0,07
и 5,731 процента для случаев 9 и 10 соответственно. Кроме того,
для случая 10, пиковое давление также значительно снижено. Что общего у
корпусов 9 и 10, так это то, что давление на
меньше, чем в нетекстурированном корпусе, прежде чем давление достигнет
своего пикового значения. Чем больше угол
r
, тем меньше будет пиковое давление
и скорость увеличения давления.Трехмерное распределение давления
для случая 7 показано
на Рисунке 17 (d).
Следует отметить, что коэффициент эксцентриситета постоянен в
моделирования для упрощения реализации в Fluent по сравнению с
постоянной нагрузкой. А по тем факторам, которые не включены в этот документ
, таким как температура и упругая деформация и так далее,
, если возможно, они будут изучены и представлены в будущем.
5.Заключение
С помощью метода вычислительной гидродинамики в данной статье проведено исследование
характеристик подшипников с консистентной смазкой
с частичной текстурой поверхности.
Грузоподъемность, коэффициент трения и трения подшипников
вычисляются и сравниваются для различных конфигураций текстуры
. Основные выводы таковы:
1 Текстура треугольника (T) имеет максимальную несущую способность
и трение; он также имеет минимальный коэффициент трения
по сравнению с другими случаями (S1, S2, Sp и G).
И форма текстуры имеет минимальное влияние на коэффициент трения
относительно несущей способности и трение
.
2 Расположение текстуры на поверхности подшипника может существенно повлиять на характеристики подшипника
. И результаты
показали, что расположение текстур в области повышения давления
вдоль направления вращения вала
полезно для улучшения характеристик подшипника. Но более широкий диапазон текстур
не всегда лучше для
, увеличивающего несущую способность подшипников.
3 Оптимальные параметры для коэффициента заполнения площади Sand
отношение глубины текстуры к минимальной толщине пленки
H / h
min
получаются соответственно при условии максимальной несущей способности
.
4 Давление кавитации может сильно повлиять на несущую способность подшипников
. Кроме того, реологические параметры консистентной смазки
в уравнении H-B
имеют аналогичное влияние на нагрузку на подшипник, т.е.е. нагрузка
увеличивается с увеличением реологических параметров
. И реологический индекс n
оказывает более значительное влияние на нагрузку по сравнению с другими
параметрами. Напротив, влияние напряжения сдвига
с
на нагрузку минимально.
Ссылки
Ausas, R., Ragot, P., Leiva, J., Jai, M., Bayada, G. и
Buscaglia, G. (2007), «Воздействие модели кавитации
в анализ микротекстурированных смазанных подшипников
», Journal of Tribology, Vol.129 No. 4, pp. 868-875.
Бакир, Ф., Рей, Р., Гербер, А.Г., Беламри, Т. и
Хатчинсон, Б. (2004), «Численные и экспериментальные
исследования кавитационного поведения индуктора»,
International Журнал вращающихся машин, Vol. 10 № 1,
с. 15-25.
Bauer, W.H., Finkelstein, A.P. and Wiberley, S.E. (1960),
«Свойства текучести модельных смазок на основе стеарата лития как функции концентрации мыла и температуры
», Proc
ASLE Transactions, Vol.3 No. 2, pp. 215-224.
Бризмер В., Клигерман Ю. и Эцион И. (2003), «Лазер
текстурирует поверхность параллельного упорного подшипника», Трибология
Transactions, Vol. 46 No. 3, pp. 397-403.
Купиллард, С., Главатских, С. и Сервантес, М.Дж. (2008),
«Вычислительный анализ гидродинамики опорного подшипника
с поверхностным текстурированием», Труды Института инженеров-механиков
, Часть J: Журнал инженерной трибологии,
Vol.222 No. 2, pp. 97-107.
Герцос, К.П., Николакопулос, П.Г. и Пападопулос, К.А.
(2008), «CFD-анализ гидродинамической смазки подшипников скольжения
смазкой Bingham», Tribology International,
Vol. 41 No. 12, pp. 1190-1204.
Гамильтон, Д. Б., Валовит, Дж. А. и Аллен К. (1966), «Теория смазки
за счет микронеровностей», журнал
Fluids Engineering, Vol. 88 No. 1, pp. 177-185.
Хао, Л., Менг, Ю. и Чен, К. (2014), «Экспериментальное исследование
эффектов текстурирования поверхности на смазку
начальных контактов линии», Lubrication Science, Vol. 26 No. 5,
pp. 363-373.
Herschel, W.H. и Балкли Р. (1926), «Измерение консистенции
применительно к растворам каучук-бензол», Proc
ASTM, Vol. 26 No. 2, pp. 621-633.
Канго С. и Шарма Р.К. (2010), «Исследования влияния текстуры поверхности
на характеристики гидродинамического подшипника скольжения
с использованием модели степенного закона»,
International Journal of Surfaceence and Engineering, Vol.4
№ 4/6, стр. 505-524.
Канго С., Сингх Д. и Шарма Р.К. (2012), «Численное исследование
влияния текстуры поверхности на характеристики
гидродинамического подшипника скольжения», Meccanica,
Vol. 47 No. 2, pp. 469-482.
Нанбу, Т., Рен, Н., Ясуда, Ю., Чжу, Д. и Ван, К.Дж.
(2008), «Микротекстуры в концентрированном конформном контакте
смазка: эффекты формы дна текстуры и относительного движения поверхности
», Tribology Letters, Vol.29 No. 3,
pp. 241-252.
Петтерссон, У. и Якобсон, С. (2003), «Влияние текстуры поверхности
на скользящие контакты с граничной смазкой», Tribology
International, Vol. 36 No. 11, pp. 857-864.
Шэн, Дж., Чжоу, Дж., Хуанг, С., Мэй, Й., Му, Д., Мэн, X. и
Фан, Дж. (2014), «Характеристика и трибологические свойства
решетки микровзубов, полученные лазерным упрочнением
на сплаве ZCuSn10P1 », International Journal of Advanced
Manufacturing Technology, Vol.76 № 5/8, стр. 1285–1295.
Сух, Н.П., Мосле, М., Ховард, П.С. (1994), «Контроль трения
», Wear, Vol. 175 № 1/2, стр. 151–158.
Тала-Игил, Н., Маспейрот, П., Фийон, М. и Боуниф, А.
(2007), «Влияние текстуры поверхности на характеристики подшипников скольжения
в установившемся режиме работы»,
Труды Института инженеров-механиков, часть J:
Журнал инженерной трибологии, Vol. 221 No.6,
с. 623-633.
Вада, С., Хаяси, Х. и Хага, К. (1974), «Поведение твердого тела Бингема
в гидродинамической смазке: Часть 3, приложение
к опорному подшипнику», Бюллетень JSME, Vol. 17
№ 111, стр. 1182-1197.
Подшипник скольжения с консистентной смазкой
Руфей Ю, Пей Ли и Вэй Чен
Промышленная смазка и трибология
Том 68 · Номер 2 · 2016 · 149 –157
156
Загружено доктором Руфей Ю в 01:24 19 Апрель 2018 (ПТ)
Назначение и способ смазки | Базовые знания подшипников
Смазка – один из наиболее важных факторов, определяющих рабочие характеристики подшипников.Пригодность смазки и метод смазки имеют решающее влияние на срок службы подшипников.
Функции смазки:
- Для смазки каждой части подшипника, а также для уменьшения трения и износа
- Для отвода тепла, выделяемого внутри подшипника из-за трения и других причин
- Для покрытия поверхности контакта качения надлежащей масляной пленкой с целью продления усталостной долговечности подшипников
- Для предотвращения коррозии и загрязнения грязью
Смазка подшипников в целом подразделяется на две категории: консистентная смазка и масляная смазка. Таблица 12-1 дает общее сравнение между ними.
Таблица 12-1 Сравнение консистентной и масляной смазки
Артикул | Смазка | Масло |
---|---|---|
Уплотнительное устройство | Легко | Немного сложный и требует особого ухода для обслуживания |
Смазывающая способность | Хорошо | Отлично |
Скорость вращения | Низкая / средняя скорость | Применяется также на высоких скоростях |
Замена смазки | Слегка хлопотная | Легко |
Срок службы смазки | Сравнительно короткий | Длинный |
Охлаждающий эффект | Без охлаждающего эффекта | Хорошо (необходим тираж) |
Фильтрация грязи | Сложная | Легко |
12-1-1 Консистентная смазка
Смазка консистентной смазкой широко применяется, поскольку нет необходимости в пополнении в течение длительного периода после заполнения консистентной смазкой, и для устройства уплотнения смазочного материала может быть достаточно относительно простой конструкции.
Есть два метода консистентной смазки. Один из них – это закрытый метод смазки, при котором консистентная смазка заранее заливается в экранированный / герметичный подшипник; другой – метод подачи, при котором подшипник и корпус сначала заполняются смазкой в надлежащих количествах, а затем пополняются через регулярные промежутки времени путем пополнения или замены.
В устройствах с многочисленными впускными отверстиями для консистентной смазки иногда используется централизованный метод смазки, при котором впускные отверстия соединяются с помощью трубопроводов и совместно снабжаются консистентной смазкой.
1) Количество смазки
Обычно смазка должна заполнять от одной трети до половины внутреннего пространства, хотя это зависит от конструкции и внутреннего пространства корпуса.
Следует иметь в виду, что чрезмерная смазка будет выделять тепло при взбалтывании и, следовательно, изменится, испортится или размягчится.
Однако, когда подшипник работает на малой скорости, внутреннее пространство иногда заполняется консистентной смазкой на две трети полностью, чтобы
2) Пополнение / замена смазки
Метод пополнения / замены смазки во многом зависит от метода смазки.Какой бы метод ни использовался, следует соблюдать осторожность, чтобы использовать чистую смазку и не допускать попадания грязи или других посторонних предметов в корпус.
Кроме того, желательно доливать смазку той же марки, что и была залита вначале.
При повторной заливке смазки необходимо ввести новую смазку внутрь подшипника.
Рис. 12-1 дает один пример метода подачи.
Рис. 12-1 Пример способа подачи смазки (с использованием сектора для смазки)
В этом примере внутренняя часть корпуса разделена смазочными секторами.Смазка заполняет один сектор, затем течет в подшипник.
С другой стороны, смазка, текущая изнутри, вытесняется из подшипника центробежной силой смазочного клапана.
Когда смазочный клапан не используется, необходимо увеличить пространство корпуса на напорной стороне для хранения старой смазки.
Корпус открыт, и старая смазка удаляется через определенные промежутки времени.
3) Интервал подачи смазки
При нормальной работе срок службы смазки следует рассматривать примерно так, как показано на Рис.12-2 , и пополнение / замена должны выполняться соответственно.
Рис. 12-2 Интервал подачи смазки
4) Срок службы смазки в экранированном / закрытом шарикоподшипнике
Срок службы смазки можно оценить по следующей формуле, если однорядный радиальный шарикоподшипник заполнен консистентной смазкой и закрыт щитками или уплотнениями.
Условия для применения уравнения (12-1) следующие:
12-1-2 Масляная смазка
Масляная смазка применима даже при высокой скорости вращения и несколько высоких температурах, и она эффективна для снижения вибрации и шума подшипников.Таким образом, масляная смазка используется во многих случаях, когда консистентная смазка не работает. Таблица 12-2 показывает основные типы и методы смазки маслом.
Таблица 12-2 Тип и метод масляной смазки
① Масляная ванна
- Самый простой способ погружения подшипников в масло для эксплуатации.
- Подходит для низкой / средней скорости.
- Датчик уровня масла должен быть предоставлен для регулировки количества масла.
(В случае горизонтального вала)
Около 50% самого нижнего тела качения должно быть погружено в воду.
(В случае вертикального вала)
Примерно от 70 до 80% подшипника должно быть погружено. - Лучше использовать магнитную пробку, чтобы частицы износостойкого железа не рассеивались в масле.
② Капель масла
- Масло капает с помощью смазочного устройства, а внутренняя часть корпуса заполняется масляным туманом под действием вращающихся частей. Этот метод имеет охлаждающий эффект.
- Применяется при относительно высокой скорости и средней нагрузке.
- Обычно используется от 5 до 6 капель масла в минуту.
(Трудно отрегулировать капельницу до 1 мл / ч или меньше.) - Необходимо предотвратить скопление слишком большого количества масла на дне корпуса.
③ Брызги масла
- В этом типе смазки используется шестерня или простой отражатель, прикрепленный к валу для разбрызгивания масла. Этот метод позволяет подавать масло в подшипники, расположенные вдали от масляного бака.
- Может использоваться на относительно высоких скоростях.
- Необходимо поддерживать уровень масла в определенном диапазоне.
- Лучше использовать магнитную пробку, чтобы частицы износостойкого железа не рассеивались в масле.
Также рекомендуется установить экран или перегородку для предотвращения попадания загрязняющих веществ в подшипник.
④ Принудительная циркуляция масла
- В этом методе используется система маслоснабжения циркуляционного типа.
Подаваемое масло смазывает внутреннюю часть подшипника, охлаждается и отправляется обратно в резервуар по трубопроводу для выпуска масла. Масло после фильтрации и охлаждения перекачивается обратно. - Широко используется при высоких скоростях и высоких температурах.
- Лучше использовать маслоспускной патрубок примерно в два раза толще, чем маслозаборный трубопровод, чтобы предотвратить скопление слишком большого количества смазки в корпусе.
- Необходимое количество масла: см. Замечание 1.
⑤ Маслоструйная смазка
- В этом методе используется форсунка для впрыскивания масла под постоянным давлением (от 0,1 до 0,5 МПа), и он очень эффективен при охлаждении.
- Подходит для высоких скоростей и больших нагрузок.
- Обычно сопло (диаметром от 0,5 до 2 мм) располагается на расстоянии 5-10 мм от стороны подшипника.
Когда выделяется большое количество тепла, следует использовать от 2 до 4 форсунок. - Поскольку при струйной смазке подается большое количество масла, старое следует сливать с помощью масляного насоса, чтобы предотвратить чрезмерное количество остаточного масла.
- Необходимое количество масла: см. Замечание 1.
⑥ Смазка масляным туманом (смазка распылением)
- В этом методе используется генератор масляного тумана для создания сухого тумана (воздух, содержащий масло в виде тумана).Сухой туман непрерывно направляется поставщику масла, где он превращается во влажный туман (липкие капли масла) с помощью сопла, установленного на корпусе или подшипнике, а затем распыляется на подшипник.
- Этот метод обеспечивает и поддерживает наименьшее количество масляной пленки, необходимой для смазки, и имеет преимущества предотвращения загрязнения масла, упрощения технического обслуживания подшипников, продления усталостной долговечности подшипников, снижения расхода масла и т. Д.
- Требуемое количество тумана: см. Замечание 2.
⑦ Масло / воздушная смазка
- Дозировочный насос подает небольшое количество масла, которое смешивается со сжатым воздухом с помощью смесительного клапана. Примесь подается в подшипник непрерывно и стабильно.
- Этот метод позволяет количественно контролировать масло в очень малых количествах, всегда добавляя новое смазочное масло. Таким образом, он подходит для станков и других приложений, требующих высокой скорости.
- Сжатый воздух и смазочное масло подаются к шпинделю, увеличивая внутреннее давление и помогая предотвратить загрязнение, смазочно-охлаждающую жидкость и т. Д.от входа. Кроме того, этот метод позволяет смазочному маслу проходить через подающую трубу, сводя к минимуму загрязнение атмосферы.
Замечание 1 Требуемая подача масла при принудительной циркуляции масла; методы смазки масляной струей
Значения коэффициента трения
μТип подшипника | μ |
---|---|
Радиальный шарикоподшипник | 0,0010 – 0,0015 |
Радиально-упорный шарикоподшипник | 0.0012 – 0,0020 |
Подшипник роликовый цилиндрический | 0,0008 – 0,0012 |
Конический роликоподшипник | .0,0017 – 0,0025 |
Подшипник роликовый сферический | 0,0020 – 0,0025 |
Значения, полученные с помощью приведенного выше уравнения, показывают количество масла, необходимое для отвода всего выделяемого тепла, без учета тепловыделения.
В действительности поставляемое масло обычно составляет от половины до двух третей расчетной стоимости.
Тепловыделение широко варьируется в зависимости от области применения и условий эксплуатации.
Чтобы определить оптимальную подачу масла, рекомендуется начинать работу с двух третей расчетного значения, а затем постепенно уменьшать масло, измеряя рабочую температуру подшипника, а также подаваемое и сливаемое масло.
Замечание 2 Примечания к смазке масляным туманом
1) Требуемое количество тумана (давление тумана: 5 кПа)
В случае высокой скорости ( d m n ≧ 40 万) необходимо увеличить количество масла и повысить давление тумана.
2) Диаметр трубопровода и конструкция смазочного отверстия / канавки
Когда скорость потока тумана в трубопроводе превышает 5 м / с, масляный туман внезапно конденсируется в масляную жидкость.
Следовательно, диаметр трубопровода и размеры смазочного отверстия / канавки в корпусе должны быть рассчитаны таким образом, чтобы скорость потока тумана, полученная по следующему уравнению, не превышала 5 м / с.
3) Масло тумана
Масло, используемое для смазки масляным туманом, должно соответствовать следующим требованиям.
- способность превращаться в туман
- обладает высокой устойчивостью к экстремальным давлениям
- хорошая термоокислительная стабильность
- нержавеющая
- осадок маловероятен
- Превосходный деэмульгатор
(Смазка масляным туманом имеет ряд преимуществ для подшипников с высокой скоростью вращения. Однако на его характеристики в значительной степени влияют окружающие конструкции и условия эксплуатации подшипников.
Если вы планируете использовать этот метод, обратитесь в JTEKT за советом, основанным на многолетнем опыте JTEKT в области смазывания масляным туманом.)